According to The CFO Survey, conducted by Duke University’s Fuqua School of Business and the Federal Reserve banks of Richmond and Atlanta, 75 percent of the respondents representing businesses across multiple industries anticipate that disruptions — including production delays, shipping delays, reduced availability of materials, and increased materials prices — will continue well into 2022.
These supply chain disruptions combined with continued hiring difficulties are forcing many manufacturing companies to re-evaluate utilization of their production lines and equipment with the goal of increasing output. Owners are investing more in automation to minimize the impact of reduced labor pools. Below is a summary of equipment planning strategies, key challenges, and potential solutions to meet capacity issues in a post-COVID supply chain impacted business environment:
{{RELATEDLINKS}} Forecasting the Future
Perhaps the most challenging aspect of equipment planning is forecasting future production, which defines the production equipment requirements. For example, do you need to increase throughput via a speed-up initiative based on future demand, or will you need to decommission a line to make room for new technology to support production of a new product?
While there is no such thing as a production forecast or equipment planning crystal ball, you can determine future market strength by conducting a sales analysis as well as investigating emerging industry trends that could positively or negatively impact your market: trade policies, energy prices, and inflation will also have a significant impact on the cost of raw materials and finished goods, which can greatly impact annual sales and subsequently the ability to accurately forecast production demand.
Once a decision to invest in new equipment is made, attention must be given to the required site, utility, and facility infrastructure investment that may also be necessary. This may include an investment in a building renovation or expansion, new utility equipment (chillers, compressors, boilers, transformers, etc.) to bring the equipment to life, as well as recruiting talent to operate the equipment. All of these require thoughtful and strategic capacity and master planning effort. It is also important to consider the start of production target date and evaluate lead times for materials, equipment, and construction activities that can be substantial given the current supply chain challenges the industry is experiencing. Early planning with visibility of the long-term business and capacity needs is essential.
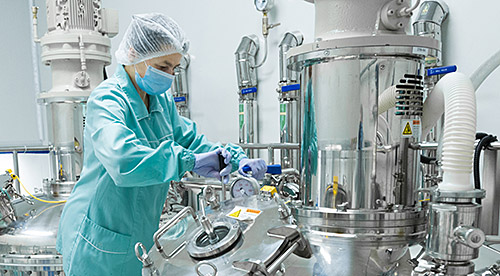
The cost of new manufacturing equipment can be quite a sticker shock for the uninitiated. As a result, equipment capital investment decisions can be a big challenge. Often a single piece of equipment can cost over a million dollars. The cost of the equipment combined with its lifespan will impact production levels for years to come, so it is a decision that needs to be made with as much confidence as possible.
Owners can improve their level of confidence through forecast scenario planning and use of manufacturing facility simulation (“digital twin”) to evaluate possible outcomes (“sensitivity analysis”). Owners want to make the decision to expand or purchase new capital equipment based on data-based analysis.
Equipment Support
It is not just the cost of new equipment that must be considered. In addition to the piece of equipment, remember to calculate the costs to support the new equipment such as utilities: power, compressed air, chilled water, waste treatment, maybe steam, as well as hiring and training technicians to operate it. Often there is a cascading effect downstream, i.e., will additional office space or employee amenities be required?
Supply chain disruptions combined with continued hiring difficulties are forcing many manufacturing companies to re-evaluate utilization of their production lines and equipment with the goal of increasing output. Also, owners want to consider whether material flow will need to change to accommodate the new equipment. New equipment can create a possible need for more raw material, pack material, and finished product storage. At the same time, owners may need to look at alternate storage methodologies to increase storage densification which can, in turn, necessitate more inbound/outbound docks, fork trucks, and operators, etc. These additional facility, utility, and operating costs can quickly add hundreds of thousands of dollars to a new equipment purchase.
Equipment Standardization
Many larger manufacturing entities have invested heavily in standardization and created a global standard equipment platform for production. This improves reliability and facilitates production forecasting; it affords the organization much more flexibility. As an example, it can relocate a line in Brazil to Germany with very little modification, knowing that it will fit in the plant and being confident that it will be easily integrated.
Not all companies are at this level of global standardization, but they often use the same or similar equipment in different plants, so relocating equipment assets is more cost-effective.
Equipment standardization also facilitates modifications and upgrades to production lines. For example, suppose the same product is being manufactured with five different types of machines at different locations. In that case, any product modification will require R&D, design, and fabrication of parts for five separate equipment technology platforms. If all production lines used the same equipment, the organization could do that work one time, ship the modified parts to the plants, write one set of instructions to install and start up. Operator training could be done once at one plant and then all the operators return to a line that is exactly the same. In addition, spare parts (drives, motors, etc.) could be centrally stored and shared among plants.
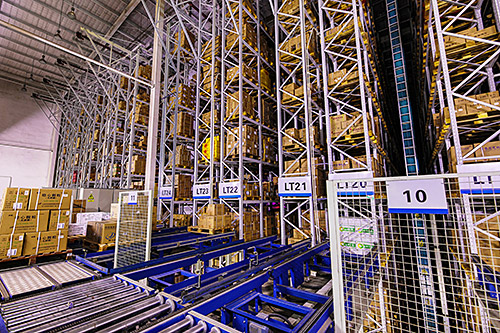
One strategy to mitigate the cost of new equipment is to conduct a utilization study of your existing equipment. There may be existing assets/equipment that are idle at other production facilities that can be relocated to facilities that need new equipment. Use a regional approach for relocation strategies. For example, if five plants are producing the same product on similar lines with similar equipment in a specific region, calculate the regional capacity plan by assessing the capacity of each plant.
Often when production lines have surplus capacity or are idle, an opportunity to relocate equipment to another location may be ideal rather than investing in new equipment. Conduct a thorough cost/benefits analysis prior to relocating equipment and remember to include the cost of taking the line down, transporting it, and reinstalling the equipment. Even with relocation costs included, very often, the cost to relocate is much less than the cost of purchasing new equipment.
There are many financial advantages to this strategy. If you purchase and install new capital equipment, you have to depreciate the full cost of that equipment, which impacts the Total Direct Cost (TDC) of the products being made. If you have a piece of equipment that has been in one plant half its life and then asset transfer it to another plant, it’s already 50 percent depreciated and may be a better opportunity to minimize the impact on TDC.
Faced with ongoing hiring difficulties, manufacturing leaders are embracing equipment automation to ensure production resiliency in the future. For example, a global diaper manufacturer had 23 diaper plants around the world. If volume was down in a particular region, and the forecast was such that the owners didn’t see the volume coming back any time soon, they found it more cost-effective to reallocate a diaper line from one country to another, enabled by global equipment standardization.
Larger manufacturing clients regularly use this approach; however, smaller companies may not have considered this approach and could benefit from taking a holistic view of all their plants and considering an asset reallocation strategy versus a new capital investment.
“Speed Up” Initiative
Instead of buying new equipment, some owners will execute a “speedup initiative” as a means of increasing throughput or implement strategies to improve overall process reliability to increase throughput. Each of these approaches may allow owners to defer a significant capital investment and associated increase in TDC to a future date.
One approach to improving reliability is to conduct a “failure mode analysis.” High-speed advanced manufacturing equipment is very complex, and you may determine through a failure mode analysis the particular operating condition(s) at which failure occurs or specific equipment that consistently fails, allowing mitigation and proactive or predictive maintenance plans to be put in place. If global equipment standardization is in place or an investment in this strategy can be made, then rolling out process and operating reliability improvements to achieve an increase in overall throughput across your production portfolio will be more straightforward.
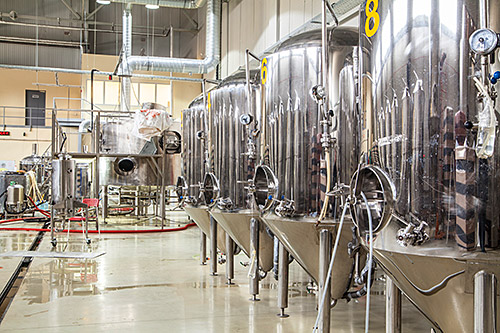
To mitigate supply chain disruption, many manufacturers are now diversifying their material supplier base. While each supplier’s raw and packing materials must meet the specifications supplied by the owner, if you are sourcing materials from three different suppliers, there is likely to be some variability. This material variability may also result in equipment failure modes. Establishing a clear set of supplier and material qualification and testing criteria — and working collaboratively with suppliers to reduce variability in the materials — should be a priority in eliminating production material waste and improving process reliability.
Embracing Equipment Automation
The pandemic has taught manufacturers a valuable lesson in investing in equipment automation when workers were unable or unwilling to come to work. In McKinsey & Company’s global survey of 800 senior executives conducted in July 2020, two-thirds of the respondents indicated an increased investment in automation and AI either somewhat or significantly.
Before the pandemic, the U.S. Bureau of Labor Statistics had projected that as early as 2022, there would be a very small number of job opportunities for humans in manufacturing thanks to the rise of automation. Now, faced with ongoing hiring difficulties, manufacturing leaders are embracing equipment automation to ensure production resiliency in the future. While the initial investment may be high, automation has multiple benefits. Because automated production lines require fewer employees, face-to-face contact is minimized, and safety is improved. It can improve quality as well as mitigate the effects of increased labor cost and may improve throughput and reliability. While automation may be expensive, consider identifying one or two areas that could be automated and proceed modularly.
Preparing for the Next Era of Manufacturing.
Reviewing your equipment planning regularly, researching emerging equipment trends, and implementing a structured equipment maintenance program can help increase production line productivity and capacity and ensure your organization is prepared for the next manufacturing era.