“Nobody is more thorough in their vetting process than P&G was,” observes West Virginia’s Secretary of Commerce Keith Burdette. And no wonder — though the company has more than two dozen plants in 20 U.S. states, this will be only the second new manufacturing facility P&G has built in America since 1971. It’ll employ 300 when it opens next year and 700 when it’s fully operational in 2019. That will make it the company’s fifth-biggest plant in terms of employment.
Workforce Development
Availability of a skilled workforce is often the number-one factor driving location decisions today, and according to state officials, Proctor & Gamble’s decision to locate in West Virginia came about as a result of the state’s determination to develop a responsive workforce development program.
Manufacturing in West Virginia
P&G joins other large manufacturers that have put down roots in West Virginia.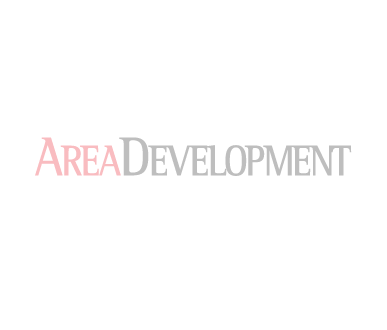
-
Bombardier
Maintains a fleet of hundreds of aircraft through its West Virginia operations
-
Toyota Motor Manufacturing
Has invested well over $1 billion over the course of a couple decades in Buffalo, West Virginia, where it makes hundreds of thousands of Toyota engines and transmissions each year.
-
Proctor & Gamble
Proctor & Gamble’s decision to locate in West Virginia came about as a result of the state’s determination to develop a responsive workforce development program.
-
Pietro Fiorentini
An Italian manufacturer of gauges for the natural gas industry company that has a West Virginia location in Wheeling
The awards are flexible, too. For example, Burdette points out that two West Virginia engineering graduates who had been hired by Pietro Fiorentini — an Italian manufacturer of gauges for the natural gas industry company that has a West Virginia location in Wheeling — received company-specific training in Italy paid for from the Governor’s Guaranteed Work Force Program.
The labor force in this area was one of the primary reasons we decided to site here. Robin Bearden, P&G vice president of Human Resources, Global Product Supply Not that training recipients need to travel that far for quality training in most cases. West Virginia employers make good use of the state’s network of technical and community colleges, and the abundance of short- and long-term training opportunities. That assurance and the critical mass of available workers helped solve the all-important workforce puzzle for P&G, according to Robin Bearden, P&G vice president of Human Resources, Global Product Supply, who spoke at the groundbreaking event: “The labor force in this area was one of the primary reasons we decided to site here.”
That’s a solid endorsement of West Virginia’s successful efforts to deal with workforce challenges, such as its state ranking of 43rd in the percentage of residents with a high school diploma, and 50th in the percentage who have a bachelor’s degree. As the P&G win suggests, traditional measures of educational attainment don’t always reflect a location’s ability to meet the needs of expanding businesses.
Market Proximity, Low Costs
Among the other reasons P&G chose West Virginia is the state’s proximity to markets on the East Coast. Yannis Skoufalos, P&G Global Product Supply officer, confirmed as much when company officials gathered to break ground: “West Virginia offers us a wonderful proximity to the eastern United States of America, which is a significant portion of the consumers that we serve throughout our supply network.”
To that, add the workforce development system and commitment, and the low cost of doing business, including reasonable rates for taxes, labor, and energy. “Our incentives were competitive, but at the end of the day you have to look past incentives. Our cost of doing business is lower than in surrounding states,” Burdette claims.
Our incentives were competitive, but at the end of the day you have to look past incentives. Our cost of doing business is lower than in surrounding states Robin Bearden, P&G vice president of Human Resources, Global Product Supply P&G is a big coup but also one in a string of successes as the state has diversified its economy. There are still plenty of jobs that are fueled by the state’s historically rich resource extraction, including in the energy sector, hardwood products, and building materials. But other key industries range from aerospace and automotive to chemicals and polymers to a wide range of manufacturing and a high-tech biometrics cluster focused on what’s known as identity technology. As the economy has diversified, the state’s employment situation has been recovering. As recently as the spring of 2015, the unemployment rate had bounced back above 7 percent, according to the Bureau of Labor Statistics. A year later, it was just over 6 percent, still higher than before the Great Recession but the lowest it had been since the recession ended.
A Welcoming Attitude
Lots of well-known names have put down roots here through the years, from Bombardier — which maintains a fleet of hundreds of aircraft through its West Virginia operations — to Toyota Motor Manufacturing, which has invested well over $1 billion over the course of a couple decades in Buffalo, West Virginia, where it makes hundreds of thousands of Toyota engines and transmissions each year.
All of those factors that go into a positive business climate certainly have played a role in this kind of ongoing success. There’s also a less tangible but equally important business-friendly culture that makes it easier to get big things done. As Liz Fikes, director-engineer in P&G Product Supply, noted at the groundbreaking, “What really started to stand out is that everybody we worked with — whether it was state, county officials — was just phenomenally welcoming.” Skoufalos agreed. “They’ve been very open…very transparent…very clear to our standards, and we’ve been very clear to our standards, and that has enabled us to understand what they have to offer and, at the same time, what we have to offer.”