Additive manufacturing — sometimes referred to as three-dimensional (3D) printing — is an emerging area in the automotive industry that could not only expand customization options, but also has the potential to influence the design and manufacture of vehicles, parts, and tools, creating many new opportunities in the industry.
A Range of Technologies
Additive manufacturing involves the deposition of material rather than removing material through processes such as cutting, drilling, and grinding. Additive manufacturing actually represents a range of technologies that can be used to create objects composed of diverse materials — polymers, metals, ceramics, wood, and others. In order to create an object, computer-aided design (CAD) drawings representing a 3D object are sent to a machine that precisely deposits material, layer-by-layer, slowly forming an object. The slow nature of forming objects with additive manufacturing and limited materials available have thus far prevented it from becoming more widely adopted in manufacturing operations.
As additive manufacturing continues to mature, some automotive futurists see it as having a bigger role in new production methods. They might suggest that, one day, customers could go to their local 3D printing workshop to print out a new car, custom-built to their preferences, rather than purchasing a standard vehicle from a dealer after it has been shipped halfway across the country from a large assembly plant. While such lofty imaginings of the future may not actually materialize, additive manufacturing is already having a substantial effect on automotive production.
Since the 1980s, the automotive industry has used additive manufacturing technologies to prototype tools and components during product development. The technology allowed designers to use physical models of parts without the high cost and long delay of creating a part using more traditional methods. Most automakers use 3D printing for rapid prototyping of parts at their research, development, and design centers. In more recent years, the proliferation of additive manufacturing technologies, advancement in 3D printers, and creativity of designers and engineers have expanded the use of additive manufacturing outside of vehicle design studios and into other areas. As the technology continues to develop and companies increase their proficiency, new opportunities for additive manufacturing in the automotive industry will become apparent. These opportunities, however, will only emerge if the technology is able to meet cycle time, quality, performance, material option, and cost requirements of automotive companies.
{{SIDEIMAGE1}} The Promise of Additive Manufacturing
Additive manufacturing is slow — producing components through additive manufacturing requires relatively a long processing time compared to incumbent technologies (e.g., metal stamping or plastic injection molding). Additive manufacturing has an advantage, however, when it comes to low volume parts, one-off manufacturing projects, or components with elaborate geometries. Traditional manufacturing methods typically require expensive tooling that is best suited for mass-produced parts, whereas additive manufacturing does not require the use of such tools, making it relatively cost-effective at low volumes and allowing manufacturers to begin production sooner.
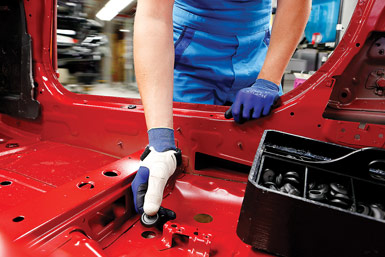
Many Fortune 1000 manufacturing companies, such as Boeing, Ford, General Electric, and Nike, are already using 3D printers to produce tooling and components for commercial products. In an Automotive News article, Mark Tomlinson, CEO of the Society of Manufacturing Engineers, was quoted as saying, “We’re really on the cusp of large manufacturers evaluating the technology as a manufacturing process rather than [to] just use for prototyping.”
Over the last couple years, 3D printing has been widely discussed in the popular media. In 2012, doctors at the University of Michigan made headlines after they saved an infant’s life using an airway splint produced with a 3D printer, a feat that has been repeated multiple times since then. Just as additive manufacturing held promise to save lives, the world became aware that the technology could produce deadly weapons when, in the summer of 2013, it was reported that 3D printers produce inexpensive, plastic guns capable of firing multiple shots.
In December 2014, the National Aeronautics and Space Administration (NASA) announced that it was able to design a ratcheting socket wrench on Earth, transmit the design to the International Space Station, and have the on-board 3D printer successfully produce the tool. Without a 3D printer, the astronauts would have had to wait for months until the next mission to the station was able to deliver the tool from Earth.
In the 2013 State of the Union, President Obama mentioned the National Additive Manufacturing Innovation Institute (now known as America Makes) in Youngstown, Ohio, as a model for a larger network of manufacturing expertise centers in the United States. The center received $70 million in federal funding and matching private funds. It has 140 members drawn from academia, nonprofit organizations, and industry, including many automotive supplier firms.
Rapid Prototyping, Diagnostics, and Newer Applications
Rapid prototyping can save an automaker millions of dollars and allow production to begin months earlier. For example, Ford Motor Company used 3D rapid prototyping to create a cylinder head for its EcoBoost engines. Traditional casting of the part would take four or five months, but using 3D printing, Ford was able to design the part, print the sand mold, and cast the metal in just three months. By saving time and producing higher-quality products, additive manufacturing can help automakers be more successful and retain jobs at factories.
In addition to prototyping and design, additive manufacturing techniques can be used to expedite diagnosing and resolving mechanical issues in vehicles. In 2010, engineers at Ford used additive manufacturing to address a brake noise issue in the Ford Explorer shortly before it was scheduled for launch. If additive manufacturing tools had not been available, the company may have faced a four-month delay in bringing the new Explorer to market.
In 2011, $48 million in revenue was collected for additive manufactured goods in the U.S. automotive industry, representing nearly 20 percent of all U.S. additive-manufacturing shipments that year.As the technology matures and automotive companies begin using additive manufacturing in more activities, shipments will continue to increase. Already, automakers are using additive manufacturing to make tools and parts, for example, assembly tools and automotive body components.
We’re really on the cusp of large manufacturers evaluating the technology as a manufacturing process rather than [to] just use for prototyping. Mark Tomlinson, CEO of the Society of Manufacturing Engineers Additive manufacturing also enables manufacturers to make lighter, customized tools to improve the ergonomics of manufacturing operations for workers. For example, BMW has used additive manufacturing to make custom-designed hand tools used in assembly. These tools have improved ergonomics and reduced weight, cost, and production time compared to hand tools produced using traditional methods. BMW has used 3D printing to produce a lightweight tool used to align and affix the rear name badges to vehicles. Another example of a 3D-printed assembly tool is a reinforced thumb cover, which is customized to precisely fit the hand of each worker. The thumb cover reduces strain on workers who use it to press rubber plugs into vehicle frames.
Automotive startups, such as Kor Ecologic, Local Motors, and Divergent Microfactories, have explored using additive manufacturing to produce vehicle bodies. Oak Ridge National Labs (ORNL), which printed parts for the Local Motors “Strati” model in 2014, used 3D printing to create a replica 1965 Shelby Cobra 427, which was displayed at the 2015 North American International Auto Show in Detroit. The use of 3D printing for vehicle bodies allows for unique designs and reduced vehicle weight. Production of the 3D-printed body parts requires a much longer time than conventional manufacturing methods, but may be cost-effective for low-volume production runs. Another drawback is that large 3D-printed pieces could complicate repairs should a vehicle be damaged. (Instead of removing and replacing a small damaged component, a much larger portion of the vehicle may need to be replaced, leading to higher repair costs).
Opportunities Abound
As with any emerging technology, adoption of additive manufacturing in the automotive industry will be facilitated through greater awareness, a more developed infrastructure, and new standards. Additive manufacturing is already undergoing a paradigm shift, as companies begin using it to make actual parts and tools rather than relegating it to the prototype shop. There are potentially many opportunities for new and already existing automotive suppliers to use additive manufacturing in their production processes. As companies adapt to new technologies and market needs, they will need to invest in new machines and human capital. In addition to investments from automakers and tier-one suppliers, there are many more opportunities throughout the supply chain.
As materials and processes change, all the parts of the supply chain must also change. For instance, 3D printer providers will need to continue improving additive manufacturing technologies to support more materials and more complex operations, faster part production, and higher quality. Material suppliers will need to develop and produce new materials and additives for 3D printers, as well as characterize and model those materials. Tooling providers may need to invest in new equipment and explore new ways of making tools for manufacturers. Community colleges and workforce skills development organizations will need to develop curricula and provide training to ensure that workers are able to meet the requirements of additive manufacturing jobs. And economic developers should focus on assisting existing companies that are transitioning to work with additive manufacturing technologies that may require more complex engineering, enhanced skills, and R&D support.