The Changing Landscape
For starters, the 2008 recession obviously left the U.S. automotive market in turmoil. The “Big 3” in Detroit consisting of Ford, GM, and Chrysler experienced significant declines during this time, while international automakers seized their opportunity to gain market share.
Fortunately, the landscape has since changed as U.S. auto sales are on track to top an annualized rate of 17 million this year, which has not been seen since 2001. This trend is only expected to increase.
Accommodating New Rules and Regulations
Regulations have been another area in which the industry has been altered. As new rules from the Corporate Average Fuel Economy (CAFE) bill continue to be rolled out, the Environmental Protection Agency (EPA) is also imposing fuel economy requirements on mainstream manufacturers. As a result, automakers are being forced to turn to new processes to increase fuel efficiency and reduce gas emissions.
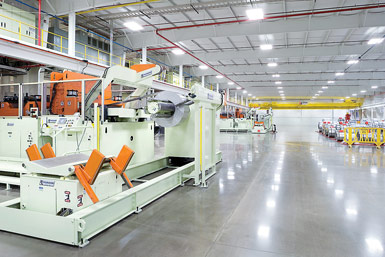
Reducing the weight of vehicles, a concept known as lightweighting, is one such process that has developed in recent years. In a recent issue of the GrayWay, Rick Schreiber, assurance partner in the manufacturing and distribution practice of leading global accounting, tax, and consulting firm BDO USA, LLP, explained the correlation between energy and the use of metals in manufacturing: “Energy is a big cost component for the metals industry and metal manufacturing. With the energy renaissance, we’re seeing growth in the metals space.”
Direct foreign investment into the U.S. is expected to continue and expand for reasons involving energy (both for the abundance and cost-effectiveness), the close proximity to the American consumer, the rising costs of international transportation, and the fact that capital investment in America is much less risky than investing in other countries.
Automakers are looking to different materials such as aluminum, titanium, and carbon fiber to meet these new demands. For instance, Ford utilized aluminum to cut 700 pounds off its 2015 F-150. Thai Summit America Corporation, a Gray customer, supplies the aluminum door panels for the F-150. As a major supplier of stamped parts for the automotive industry, the manufacturer expects this trend in metals to continue. Since lightweighting continues to significantly impact fuel efficiency, it’s inevitable that more auto manufacturers will embrace these lighter materials more aggressively.
Also, automakers are finding that adopting fuel-saving tech like 8-speed transmissions is helping them meet the tightening regulations. This trend is consequently a growing demand for manufacturers such as ZF, one of the 10-largest automotive suppliers worldwide. ZF recently authorized a 458,137-square-foot expansion to its Gray Court, S.C., manufacturing facility to accommodate the production of 8- and 9-speed transmissions due to increasing demand. The 9-speed transmission is actually the first of its kind to be introduced to the global market.
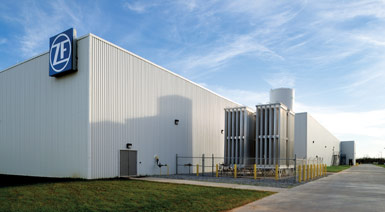
Other technological advances and innovations have had a major effect on the auto industry as well. A decade ago, who would have thought that the debut of the world’s first 3D printed car was in the near future? New technology is also taking us to the place where driverless cars are actually being considered viable. While the latter is still a futuristic concept, the tech capabilities within vehicles today are truly astounding.
Energy is a big cost component for the metals industry and metal manufacturing. With the energy renaissance, we’re seeing growth in the metals space. Rick Schreiber, assurance partner in the manufacturing and distribution practice of leading global accounting, tax, and consulting firm BDO USA, LLP, explaining the correlation between energy and the use of metals in manufacturing The Customers’ Perspective
Though the industry has changed and is continuing to do so, automotive manufacturing is strong. Our customers, which consist of automakers, assemblers, and tiered suppliers, indicate that growth is still very much on the horizon. Expansions are being projected for existing locations, and supplier networks are growing as the supply chain becomes much more complex. Volkswagen, for instance, is one example of an OEM that continues to expand its footprint at its existing location in Chattanooga, Tenn., in order to accommodate new product lines and increasing volumes.
Direct foreign investment into the U.S. is expected to continue and expand for reasons involving energy (both for the abundance and cost-effectiveness), the close proximity to the American consumer, the rising costs of international transportation, and the fact that capital investment in America is much less risky than investing in other countries. The U.S. has come to be known as a safe place for manufacturing investment due to the democratic freedoms the country upholds. Manufacturers can rest assured that the government will not overtake their operations.
Due to their growing demands, our automotive customers prefer more of a turnkey solution for the design and construction of their plants as opposed to more customizable projects. This enables the manufacturers to get their products to market faster, while also ensuring more predictable safety and quality measures.
The start of production (SOP) is always a priority for all our customers, but especially our automotive plant construction customers since they have new models that need to either get to another supplier to finish production or directly to market. If we, as the design-builder, fail to finish on time, we’ve impacted our customer’s schedule, which can be detrimental to their bottom line since it costs them money and potentially sales. This impact is also felt on the economy.
From automakers to suppliers, the pace of the industry is rapidly accelerating, which means that innovation is key to increasing future market share. This also opens the door for new players to enter the market and shake up the industry both for the good and for the challenges.