The resurgence of manufacturing across North America is creating a new kind of complexity for companies evaluating sites. Reshoring and nearshoring are no longer abstract strategic concepts—they are active, time-sensitive decisions influenced by policy and resulting in wage inflation, energy demands, and a dwindling supply of viable real estate.
Manufacturers are now forced to make tradeoffs between lower-cost labor and rising labor strain, between faster timelines and infrastructure limitations, between regions that once felt like defaults and markets that now require hard second looks. One of the most frequent conversations we have with clients today revolves around the U.S.-Mexico tradeoffs. And the answer is more complicated than ever.
Mexico continues to offer a compelling cost advantage. Across the board, wage differentials for manufacturing labor—whether direct or indirect—can reach up to 80 percent compared to the U.S., even when factoring in the more generous benefits packages that Mexican workers expect. In Mexico, it's not uncommon for companies to cover employee transportation, offer cafeteria plans, or provide attendance bonuses. These benefits aren’t optional. They’re essential to talent retention, especially given the market saturation, and can amount to 100 percent of an employee’s base salary.
Site readiness is now just as much about power availability as it is about pad grading.
Despite the wage gap, labor availability in Mexico is tightening. Companies are continuing to locate high-labor operations there, and the building strain is clear. Across skill levels, from direct labor to engineering and maintenance, employers face persistent turnover and fierce competition. Though brand attachment and employer loyalty can go far in Mexico, it doesn’t solve the systemic pressure.
In the U.S., labor is more expensive but not quite as saturated. U.S. regions still offer emerging labor markets with lower turnover and stronger community ties. In these markets, workforce development programs, coordination between employers, and long-standing ties within the community can provide an edge. One region might be more established but face high turnover as workers chase small wage increases. Another might be less developed but offer a more collaborative culture and better employee retention. The key is understanding the nuance.
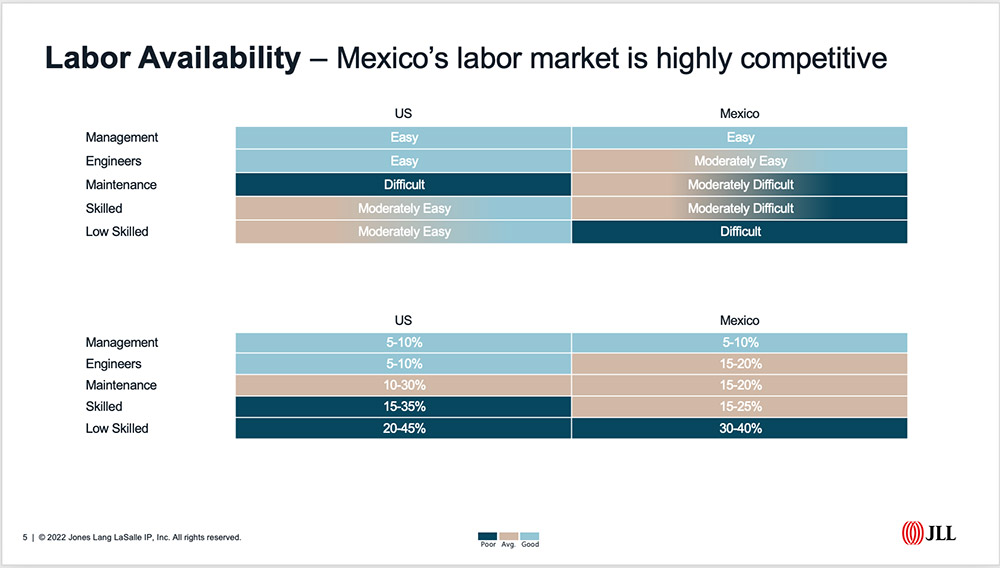
Utilities are becoming a bigger factor in site selection models with electricity often being the driving factor. In Mexico, challenges are emerging not just around cost but around reliability and access. Delays in securing new electricity contracts are common, and communication with providers can still depend on physical mail rather than email or phone calls. Furthermore, some providers will limit electricity capacity depending on the size of the operations. For companies that require higher loads, like EV suppliers or advanced manufacturing, grid limitations can delay expansion timelines significantly. In some areas, buyers must purchase the rights to electricity in addition to paying for usage. This can mean millions in upfront costs before construction even begins.
In the U.S., the utility process is rarely seamless, but the baseline expectations around reliability and communication are still stronger. That difference matters more as companies push for higher energy loads, faster connections, and more aggressive timelines. Site readiness is now just as much about power availability as it is about pad grading.
80%
Site selectors are recalibrating their processes as real estate scarcity becomes the norm. The model that used to begin with regional preferences and end with a short list of sites is shifting. Now, many projects start with a scan of which viable sites exist across a wide range of markets, followed by an evaluation of how to make those specific regions work. Clients have been forced to flip their thinking. That’s how scarce plug-and-play options have become, and how important time-to-market is. If a site has the land, the utilities, and a clear path to development, companies are willing to solve for workforce, training, and supply chain logistics accordingly. The constraint is no longer geographic preference. It’s site availability.
Mexico is no longer the default choice for labor-intensive operations.
Investments into both the U.S. and Mexico have surged in recent years, but the kinds of projects going into each country tell a deeper story. Mexico continues to attract automotive manufacturing and other labor-intensive operations, especially in the northern and central regions. The U.S., by contrast, is seeing a sharp increase in capital-intensive investments, particularly in sectors like semiconductors and renewables. The CHIPS and Science Act and the Inflation Reduction Act have fueled billions in new investment and turned the U.S. into a destination for high-tech, high-energy manufacturing.
International capital flows confirm the shift. Chinese investment into Mexico has doubled in recent years, driven by a combination of strained U.S.-China relations and Mexico’s proximity to U.S. consumers. Meanwhile, U.S. investment into China has dropped by 75 percent. U.S. companies are now reinvesting at home at the highest rate in decades and increasingly looking to.
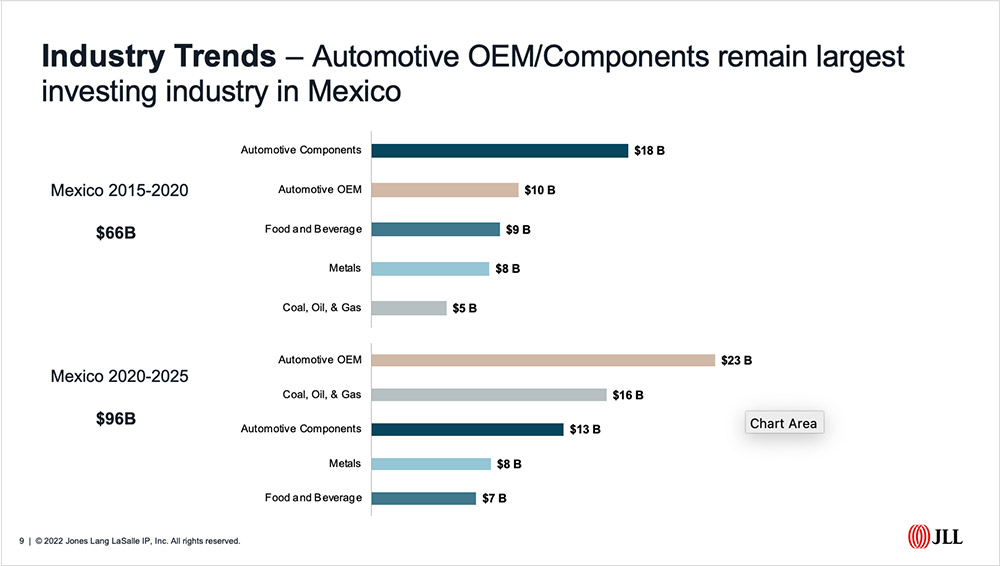
Other trends are compounding the challenge. Wage inflation in Mexico is rising, especially in manufacturing hubs. Pending legislation could reduce the standard work week from 48 hours to 40, without a corresponding reduction in pay. That would drive up effective labor costs even more. Meanwhile, larger projects—especially in data, battery, and chip manufacturing—are asking for hundreds of acres and hundreds of megawatts of power in the U.S. Even in markets with favorable conditions, infrastructure simply can’t keep up with the demand curve.
Clients have been forced to flip their thinking. The constraint is no longer geographic preference.
Recently, the U.S. outlined its reciprocal tariff policy on a broad list of countries around the world. In modeling the cost impact of such tariffs for our clients, it is clear the tariffs are going to have a significant impact on the cost of operations abroad versus in the U.S. By way of example, a few months ago, a client evaluating sites in both the U.S. and Mexico asked our team to run a standard model without factoring in tariffs and then remodel the output assuming a number of tariff impacts. In one case, assuming 25 percent of their product did not comply with USMCA and carried a 25 percent tariff, the project costs rose but the overall rankings remained the same with Mexico being the lowest cost option. However, when we assumed 50 percent non-compliance, the model flipped. Suddenly, the lowest-cost U.S. site outperformed the Mexican options. Could this indeed stimulate a change in thinking regarding direct investment site selection?
The choice between Mexico and the U.S. used to be simpler for many industries. Now, it’s a matrix of labor availability, utility capacity, tariff risk, construction timelines, and investor confidence. Every company’s supply chain looks different. Every project has its own cost sensitivities. But across the board, companies are placing a higher value on resiliency and certainty than they did five years ago.
Mexico is no longer the default choice for labor-intensive operations. The U.S. has become a serious contender as more companies are at least building it into their initial comparisons—and some are choosing it outright. That shift is real.
Site selectors are responding by getting more granular, more local, and more proactive. The future of North American manufacturing isn’t just about cost. It’s about solving the complexity rooted at the intersection of people, power, policy, and place.
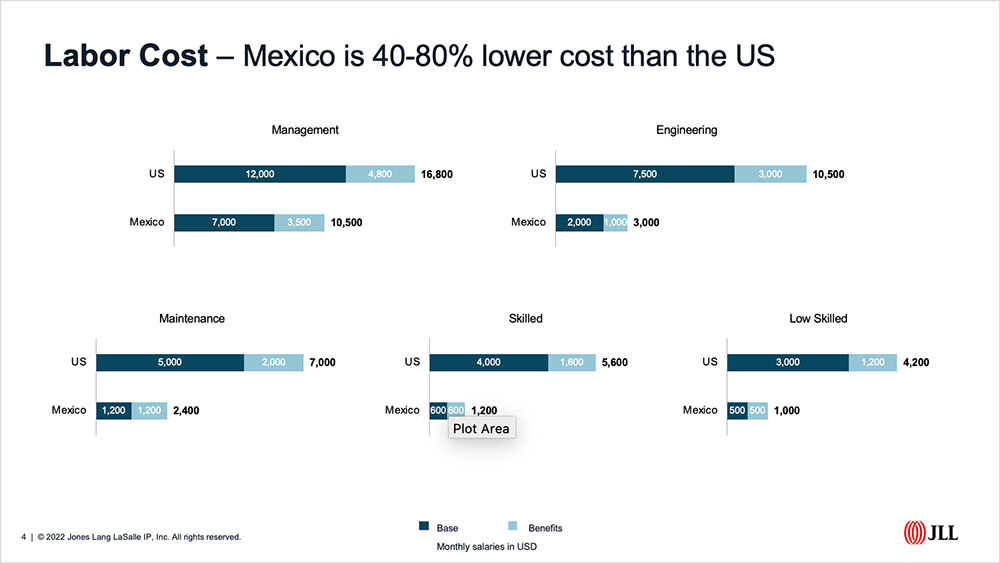