In today’s high-stakes economy, logistics is no longer a forgotten back-end function — it’s a front-line competitive advantage. As global supply chains grow increasingly complex and consumers demand faster delivery times, the race to modernize logistics infrastructure is beginning to reshape the U.S. economic landscape.
Now more than ever, the ability to move goods efficiently isn’t just a cost consideration; it’s become a critical factor in the calculus of where companies choose to invest, expand and build.
Across the country, states and regions are locked in a new kind of competition — one not just for factories or headquarters, but for logistics supremacy. At the heart of this contest are game-changing investments in inland ports, cold storage facilities, maritime terminals and air cargo hubs that are redefining how companies manage inventory, optimize distribution networks and serve their customers.
These logistical assets are no longer invisible amenities — they are economic anchors. From e-commerce and automotive to food processing and advanced manufacturing, the industries powering the next generation of growth are demanding more robust, resilient and strategically located supply chain solutions. The states that deliver them are seeing a direct payoff in jobs, new investment and long-term competitive advantages.
These logistical assets are no longer invisible amenities — they are economic anchors.
This article explores the shifting dynamics of U.S. logistics infrastructure, spotlighting the regions that are leading the charge, the sectors most impacted by these changes and the strategies economic developers are utilizing to stake their claim in the evolving supply chain economy.
Rise of Inland Ports and Regional Logistics Hubs
As competition heats up in the logistics space, one trend is making a particularly strong mark across the country: the rapid rise of inland ports and intermodal logistics hubs. No longer tethered to coastal regions, the flow of goods across America is increasingly driven by facilities strategically planted deep within inland markets, close to where products are consumed or manufactured.
Inland ports are intermodal logistics centers located away from traditional seaports, designed to connect the interior of the country to global trade routes via rail and highway infrastructure. These facilities allow goods arriving at major seaports to be offloaded, transferred and distributed with a high level of efficiency, while also reducing congestion at coastal gateways and trimming costly last-mile delivery timelines.
Several key factors are propelling this inland migration. The first is the growing congestion at coastal ports, especially on the West Coast, where backlogs and labor disruptions have sometimes snarled supply chains. By shifting part of the logistics operation inland, companies can bypass bottlenecks and assert greater control over timing and distribution.
$20B
Equally important is the strategic advantage of proximity to inland population centers and manufacturing clusters. Logistics hubs located near major highways and freight rail lines offer companies a more rapid and predictable route to market — and increasingly, that’s what primarily drives site selection.
These inland ports are not just rail yards dotted with a sprinkling of warehouses; rather, they’re evolving into vibrant, full-scale industrial ecosystems that support distribution, e-commerce fulfillment, manufacturing and light assembly.
Here are three examples of the trend in action:
Inland Port Greer – South Carolina
One of the Southeast’s most dynamic logistics success stories, Inland Port Greer has emerged as a model for how rail-connected facilities can supercharge regional growth. Operated by the South Carolina Ports Authority, Greer recently underwent a major expansion, adding more than 9,000 feet of new rail to accommodate longer, more frequent trains. With this investment, the port doubled its capacity to handle 300,000 rail lifts annually, dramatically increasing the volume of containers moving in and out of the region and strengthening its role as a strategic gateway to the Port of Charleston.
States and regions are locked in a new kind of competition — one for logistics supremacy.
International Inland Port of Dallas – Texas
In North Texas, Dallas has transformed itself into a key inland logistics hub by leveraging its vast transportation network and business-friendly environment. Over the past decade, the city has made substantial investments in infrastructure, spurring more than 10 million square feet of new development dedicated to distribution, logistics and manufacturing. Anchored by Class I railroads and major interstate highways, the Dallas Inland Port has become a magnet for companies looking to scale operations in the region.
Montgomery Intermodal Facility – Alabama
Alabama is also stepping boldly into the inland logistics game with a transformative project in Montgomery, where a $94 million intermodal facility is taking shape through a partnership between CSX and the Alabama Port Authority, operator of the Port of Mobile. This facility will provide seamless, cost-efficient access to global markets by connecting central Alabama directly to one of the nation’s fastest-growing seaports. More than a transportation hub, the project is a cornerstone of Alabama’s broader strategy to strengthen supply chain infrastructure and attract investment in industries ranging from automotive to aerospace.
Cold Storage Boom: Adapting to New Market Demands
As consumer expectations evolve and supply chains become ever more specialized, cold storage has emerged as one of the hottest segments in logistics real estate. The rise of e-commerce grocery, the pharmaceutical cold chain and consumer appetite for farm-to-table freshness have aligned to create a surging need for temperature-controlled logistics facilities across the nation.
The race is on to build a logistics network that can meet tomorrow’s biggest challenges.
According to Cushman & Wakefield, the U.S. cold storage market surpassed $190 billion in value in 2024, and growth projections remain strong. Developers and investors are moving quickly to stay on top of the game — just look at Americold’s recent $127 million acquisition of a 10.7 million-cubic-foot cold storage facility in Houston, expanding its capacity by more than 35,000 pallet positions.
But with surging demand comes challenges. Much of the nation’s cold storage infrastructure is outdated — the average facility in top markets is more than 30 years old. Meanwhile, the vacancy rate for modern space remains historically low, dropping to 3.4% in the first half of 2024, according to one estimate. This has triggered a wave of build-to-suit and speculative developments, as food processors, pharmaceutical companies and other firms search for high-efficiency, next-generation facilities capable of meeting today's throughput and regulatory standards.
Cold storage should no longer be thought of as a niche. Instead, it represents a critical link in the modern supply chain. States and regions that can deliver on this specialized infrastructure will be well positioned to capture new investment and meet the logistics demands of the next decade.
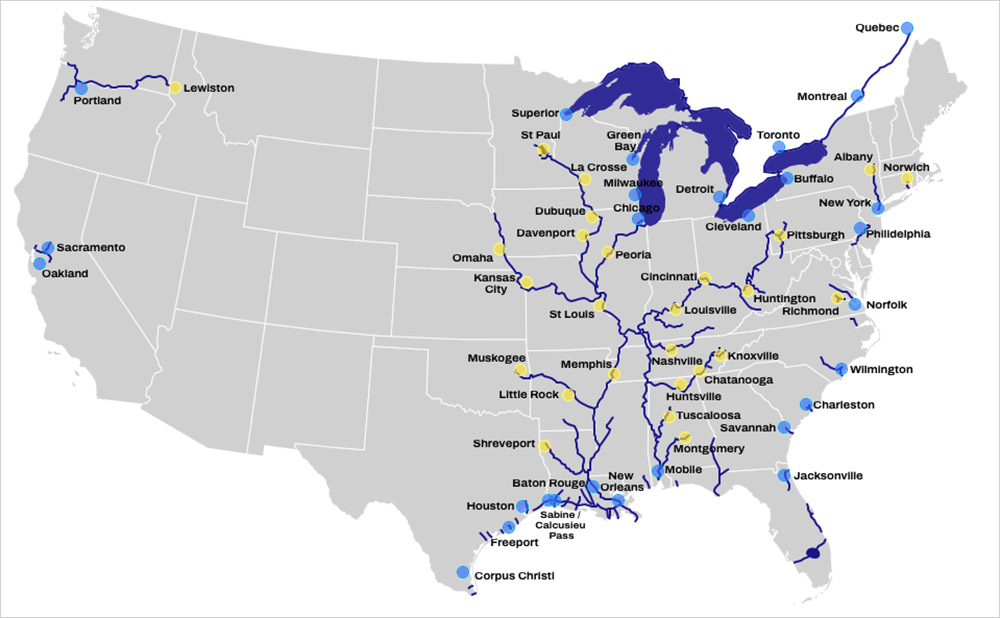
Port of Mobile: Expanding Alabama’s Global Gateway
As the logistics landscape evolves, many traditional seaports are undergoing significant enhancements to solidify their roles as pivotal trade and transportation hubs. The Port of Mobile exemplifies this trend. The Alabama Port Authority recently kicked off the fourth phase of its container terminal expansion, aiming to double the terminal's capacity from 500,000 to more than 1 million 20-foot equivalent units (TEUs) annually. This $104 million project includes the addition of 32 acres to the existing facility and the construction of an interterminal connector bridge to facilitate on-dock rail access, improving operational efficiency and accommodating growing cargo volumes.
In tandem with the terminal expansion, the port is advancing the final phase of its Mobile Harbor deepening and widening project. Upon completion, the harbor will become the deepest port in the Gulf of Mexico, featuring a 50-foot depth and a three-mile passing lane to accommodate larger post-Panamax vessels. This enhancement positions Mobile as a more attractive first port of call for ships transiting the Panama Canal, potentially increasing cargo traffic and economic activity in the region.
300,000
These strategic investments not only elevate the Port of Mobile's capacity and efficiency but also reinforce Alabama's commitment to developing a robust, multimodal logistics infrastructure. By integrating advanced port facilities with inland transportation networks, Alabama is positioning itself to capitalize on emerging supply chain trends and attract future investment in the growing regional economy.
Air Cargo Expansion: Accelerating Supply Chain Efficiency
In an economy increasingly driven by speed and precision, air cargo has become an indispensable link in the logistics chain. Fueled by the surge in e-commerce and rising consumer expectations for rapid delivery, air freight is no longer reserved for high-value goods — it's becoming a baseline requirement for modern distribution strategies. Airports across the U.S. are responding with significant infrastructure investments to expand capacity and streamline operations. One standout example: French shipping giant CMA CGM’s $20 billion investment to grow its logistics and terminal presence in the U.S., which includes a proposed air cargo hub in Chicago that promises to create a high-speed gateway for goods moving throughout the Midwest and beyond.
Cold storage should no longer be thought of as a niche. It represents a critical link in the modern supply chain
The economic ripple effect of air cargo development is substantial. These facilities draw logistics companies, manufacturers and e-commerce players looking to shrink delivery windows and optimize global supply chains. In regions with established cold storage, rail and intermodal assets, air cargo helps knit together a full-spectrum logistics hub that boosts competitiveness and job creation.
Policy and Infrastructure: Navigating the Competitive Landscape
Behind every logistics hub, inland port or cold storage facility is a web of policy decisions and public investments shaping what gets built — and where. At the federal level, initiatives like the Port Infrastructure Development Program (PIDP) are playing a critical role. In 2024, the PIDP allocated $450 million to modernize both coastal and inland waterway ports, reinforcing the backbone of America’s supply chains and enhancing national economic security.
States, too, are rising to the challenge. Across the country, governments are deploying creative strategies — from targeted tax incentives to infrastructure bonds — to attract logistics investment and catalyze development. Public-private partnerships have emerged as vital tools, combining public oversight with private-sector efficiency to fast-track complex projects and share financial risk.
Air freight is no longer reserved for high-value goods — it's becoming a baseline requirement.
Yet, the path forward isn’t without friction. Regulatory hurdles, environmental permitting and community opposition can slow progress, particularly when it comes to large-scale infrastructure projects. At the same time, the sector remains ripe with opportunity. Innovations in automation, AI-driven logistics planning and sustainable design are transforming how facilities are built and operated, creating the potential for smarter, greener and more resilient supply chains.
A Logistics Landscape in Motion
From inland ports and cold storage to air cargo expansion and port modernization, America’s logistics landscape is undergoing a transformation with far-reaching implications. These developments are not just about accelerating the movement of goods. At the core, they are all about unlocking economic potential, reshoring strategic industries and building the infrastructure of the future.
Looking ahead, the regions that succeed will be those that act strategically by investing in connectivity, embracing innovation and aligning smart public policy with ambitious private strategies. As the global economy continues to evolve, the race is on to build a logistics network that can meet tomorrow’s biggest challenges.
For policymakers, business leaders and economic development professionals, the opportunity is crystal clear: by working together to shape a forward-looking logistics ecosystem, we can drive growth, create jobs and position communities to thrive in a rapidly changing world.