In a recent conversation with one of our clients who recently established their fourth production facility in Mexico, I was told that they are paying very high prices to express ship components from Asia by air to their production operations south of the border. They are doing this precisely because they have learned that it costs more to have a manufacturing line inoperable than to pay a higher price for components and materials. Clearly, this is not a sustainable strategy.
Mexico, the United States’ second-largest trading partner behind Canada, is an outstanding manufacturing location, but it’s not for every company. This article explores both the advantages and challenges of placing a production operation in Mexico.
An Economy Geared for Export
Mexico’s manufacturing economy is geared for export…primarily to the U.S.
Mexico has been gaining ground on China as a key link in the global supply chain for companies serving the U.S. marketplace. During the three-year period of 2018–2021, U.S. imports from Mexico have increased 11.9 percent to $384.6 billion, while those from China have actually decreased by 6.2 percent to $504 billion over the same time period. However, from January through August of this year, imports from China are rebounding — up 18.3 percent compared to the first eight months of last year, while those from Mexico have grown 21 percent over the same time period.
The manufacturing sector provides almost 4.5 million jobs in Mexico, almost two-thirds (65 percent) of which are provided by companies involved in the IMMEX (manufacturing for export) program. Also referred to as “maquiladoras,” these companies lost 123,000 IMMEX jobs during the first four months of the pandemic in 2020. The jobs were fully recovered by Oct 2020, just 7 months into the pandemic. IMMEX manufacturers in Mexico have added more than 200,000 new production jobs since that time and in August 2022 reached their highest level in history at almost 4.458 million.
While two industry segments provide almost half (46.5 percent) of Mexico’s manufacturing employment — food and beverage (1.042 million jobs) and transportation equipment (1.034 million jobs), there is still solid diversity in the country’s manufacturing base. As seen in Figure 1, there are four additional manufacturing sectors that employ at least 250,000 people south of the border.
Mexico, the United States’ second-largest trading partner behind Canada, is an outstanding manufacturing location, but it’s not for every company. Our project activity with companies considering Mexico reflects this diversity. Over the past few years we have worked with producers of industrial equipment, furniture, automotive parts, medical devices, and others who are contemplating operations in Mexico. In fact, almost every one of our clients that is looking to reposition facilities or expand their current capacity requires us to analyze both Mexico and the U.S. for their projected operations.
What types of companies should consider Mexico as a production location? We believe Mexico is wide open for almost any type of manufacturer — especially if it is not hypersensitive to electric and logistics costs. (These two issues are discussed later in the article.) While there are no hard and fast rules about this, any company contemplating an operation with at least 200 production jobs — or at least 15 percent of their total product cost comprised of labor — could potentially benefit from a location in Mexico. Having said that, we have seen companies with smaller headcount and lower labor content also find success there.
From a supply chain perspective, the most important relationship between the U.S. and Mexico is found in the transportation equipment sector, primarily the automotive industry. Automotive OEMs in the United States depended upon Mexican suppliers to provide almost $53 billion in auto parts last year, 41 percent of the total value of all car parts imported into the U.S. Imports from Canada were a distant second with only $13.1 billion. Additionally, Mexico ranks #1 or #2 for imports into the U.S. for other industry segments such as medical devices ($8.5 billion in imports in 2021), consumer electronics ($71.0 billion), electrical equipment and appliances ($34.7 billion), food and beverage ($20.1 billion), and fabricated metal products ($11.3 billion). Clearly, Mexico has shown strength in a wide range of industry segments and is an integral part of the global supply chain equation.
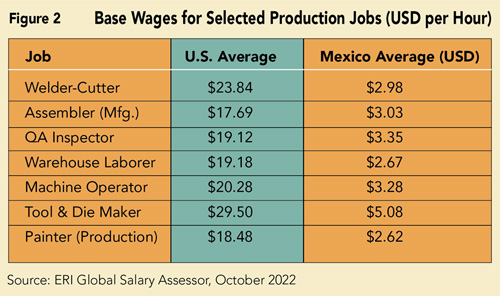
Mexico offers two principal value propositions to a manufacturer — labor cost and proximity to the United States marketplace.
Labor costs in Mexico will be a fraction of those paid in the U.S. Figure 2 depicts average base wages for each country for certain production jobs; however, benefits in Mexico can add another 70 percent to 115 percent to the base wage versus 28 percent to 35 percent in the United States. Common benefits in Mexico include productivity bonuses, attendance bonuses, free transportation to/from work, partially subsidized meals (two per day), on-site doctor or nurse, and others. All of these, plus a whole host of benefits mandated in Mexican federal labor law (housing subsidy, healthcare subsidy, Christmas bonus, etc.) are calculated in the fully burdened wage. Even with the higher benefits load in Mexico, it is not uncommon to see fully burdened labor rates in Mexico that will be 15 percent to 25 percent of fully burdened labor rates in the U.S.
The second advantage to Mexico is its proximity to the United States. You can transport a finished product (component or sub-component) in Mexico from almost any location in the country, cross at one of many ports of entry along the U.S.-Mexico border, and have that product land in almost any community in the United States within a matter of days. Of course, it will take several weeks for that same product, component or sub-component to be shipped from Asia (20–22 days to Long Beach), and then the shipment will encounter additional berthing delays when the container arrives at port. Coupled with truck driver shortages and significant rail backlogs, transit times are often difficult to predict. A location in Mexico doesn’t completely solve this problem, but it does provide a much better solution than purely relying upon suppliers from Asia.
Close to one third (30.9 percent) of IMMEX companies, representing 34.4 percent of IMMEX employment in Mexico, are taking full advantage of logistics by locating in a Mexican city located immediately on the 2,000-mile border with the United States. For most products manufactured in one of these border cities, they are crossing in less than half a day and are on their way to the final destination in the United States.
The most important relationship between the U.S. and Mexico is found in the transportation equipment sector, primarily the automotive industry. An additional benefit of locating on the border is that your management team, engineers, and other professionals can live in a U.S. city and commute to the Mexican operation on a daily basis. Most of these managers will be enrolled in a trusted-traveler program like SENTRI that allows them to experience almost no wait at the border when they cross northbound at the end of the day. Additionally, the cost of living in these U.S. border cities tends to be well below U.S. averages.
Mexico’s Commitment to STEM Higher Education
Although labor cost and proximity to the U.S. are the principal drivers to a Mexican location, the nation has been positioning itself to attract higher value-added operations by investing in STEM education at its institutions of higher education. Today, Mexico is one of the top eight producers of engineering talent in the world, and this past school year (2021–2022), Mexico had over 847,000 students enrolled in engineering and related programs and conferred 135,765 engineering degrees. This was up from 129,600 graduates just three years ago. Higher education south of the border is also doing a good job of responding to the needs of industry by creating special programs related to aerospace, automotive, and biomedical industries to name a few.
A small handful of companies like Aptiv (formerly Delphi) are taking full advantage of this talent. Aptiv’s Mexico Tech Center in Cd. Juarez (on the border across from El Paso, TX) employs a large number of engineers (at one time more than 2,000) who have generated hundreds of pieces of intellectual property in new products, process improvements, and more.
Labor Laws Strongly Favor the Employee
When the USMCA (formerly NAFTA) was adopted during the Trump Administration, Mexican workers were given greater standing in collective bargaining agreements, and many states in Mexico now require companies to formally accept a labor union. A data point we closely monitor is labor disputes that are registered with the appropriate Mexican authorities in each of the cities across the country. We apply the number of annual disputes to a ratio such as “per 100,000 population,” and the higher ratios can be an early warning signal about the potential “militancy” among unions in that area.
Perhaps the most significant HR issue to be aware of is unilateral termination of an employee. There is no “employment at will” in Mexico, like we see in the U.S., so terminations must be “for cause.” Employees that are laid off or otherwise terminated without cause are entitled to severance pay that starts with 12 days of wages for each year of employment. Severance pay may also include proportional amounts of various benefits like a Christmas bonus, vacation pay, and any agreed-to benefits that have not been paid as of the termination date.
On the plus side, federal labor law allows the worker to work eight hours per day and 48 hours per week before overtime is incurred. Overtime pay will be either two or three times the hourly pay rate depending upon the amount of overtime incurred on a daily or weekly basis.
Mexico has been positioning itself to attract higher value-added operations by investing in STEM education at its institutions of higher education. Be aware that labor turnover in Mexico will likely be higher than at your operations in the U.S. Successful labor turnover rates (for your direct and some indirect personnel) will be less than 3 percent per month, a metric that would be deemed unacceptable in most of the U.S. Companies that successfully manage labor turnover will give great attention to three things in the following order of priority:
- Enter Mexico with a strong understanding of the family-oriented culture, and make sure you establish policies and a plant culture that promote this.
- Choose the right location within a given community. Locations that offer lower employee commute times will be more competitive.
- Pay competitive wages and benefits. You do not have to be in the upper echelon of pay and benefits for a given community.
Certain Operating Costs Will Be Higher in Mexico
Due to driver shortages that are even more acute than in the U.S., higher maintenance costs for fleets given lower quality of the infrastructure, and higher insurance costs, transportation lane rates will be higher in Mexico. We typically will budget 20 percent to 25 percent higher per mile costs in Mexico vs. the U.S. and will consider an additional half to one full day of transit time as trucks arrive for northbound clearance at the U.S.-Mexico border.
Electric rates are determined by size of load and time of day use. Rates will be lower in non-peak hours, and manufacturers that can balance their load over a 24-hour period will be rewarded. Still, most electric rates you will incur can fluctuate between $0.10 and $0.20 per kwh, with the average typically around $0.13 per kwh.
Supplier Base Lacks Maturity
If your company depends on suppliers of raw materials or certain types of components, be aware that while the supply base is growing in Mexico, it still lacks maturity. An estimated 75 percent of the value of Mexico’s exports start as a component part or raw material from somewhere else, principally the U.S. or Asia (China). We suspect that this will begin to change somewhat as companies pay more attention to supply-chain resiliency than supply-chain cost by expanding their presence in Mexico.
Multiple Options to Commence Operations
Since Mexico’s manufacturing for export program (maquila) was created in the late 1960s, the country has liberalized its investment laws that allow companies to own 100 percent of the assets related to their production facilities, including land and building. Service providers across the nation have stepped up to offer various types of “soft landing” options to manufacturers seeking to establish a manufacturing presence in Mexico. Contract manufacturers have sprung up across the country (albeit not in large numbers) that can handle every aspect of manufacturing your products.
Due to driver shortages…higher maintenance costs for fleet…and higher insurance costs, transportation lane rates will be higher in Mexico. A more popular option for many companies entering Mexico for the first time is through a “shelter service” provider. These companies will provide a combination of services to include HR support, import/export assistance, environmental compliance, facilities management, transportation services, purchasing and more — and allow you to be operational in a matter of months under their corporate umbrella. Many companies will “graduate” from these programs after a few years, having learned how to successfully operate in Mexico through their shelter service provider.
Whether it is stand-alone, outsourcing to a contract manufacturer, or contracting with a shelter service provider, each option provides a unique blend of cost and risk that companies must assess.