A Heightened Focus on Reshoring
As costs and risks of lengthy supply chains become even more apparent in the wake of the COVID-19 pandemic, more U.S. companies may consider reshoring their operations to the Americas.
Q3 2020
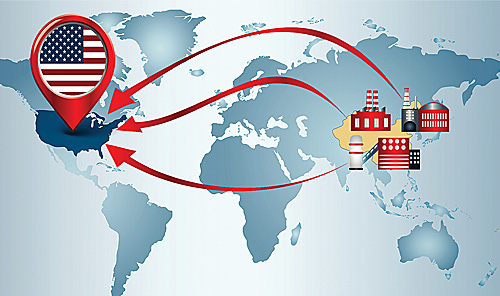
Incentivizing Reshoring
Manufacturing companies accelerated moving production to low-cost manufacturing countries (known as offshoring) in the early 1990s. In the rush to globalize, key manufacturing sectors were abandoned in the United States. But now that the vulnerabilities of doing so have been exposed, there is talk of “de-globalization,” or reshoring.
Reshoring includes not only the relocation of existing manufacturing back to the United States, but new greenfield investment in domestic plants that might have gone overseas. A related term is “near-shoring,” which refers to companies bringing production back to countries near the United States (usually Mexico or Canada).
The European Union (EU), Japan, and United States are among the nations that have publicly discussed decreasing their trade dependency on China. For example, White House economic advisor Larry Kudlow said he’d like to see supply chains based in the United States. Government officials have put forward the idea of paying for moving costs associated with bringing manufacturing facilities back. Commerce Secretary Wilbur Ross told Fox Business Network the COVID-19 outbreak could encourage American manufacturers to return manufacturing to North America. Various legislation has also been introduced that might encourage reshoring.
For the United States, this development follows a pre-existing decline in business relations with China, as the two countries have been in a trade war since 2018. These facts put the United States on a clear trend for incentivizing reshoring. The previous focus on the lowest cost scenario, which led to growth in China and Southeast Asia, will now become more balanced as companies look to reduce risk. This should benefit U.S. locations as more companies seek to locate production facilities close to the customers they serve and increase redundancy.
The Benefits of Reshoring
Having a local supply chain reduces variables that may cause disruption. Local supply chains also tend to be flexible and agile. Ordering from nearby suppliers allows for ordering more (or fewer) quantities on shorter notice — an important factor when unforeseen circumstances happen.
The previous focus on the lowest cost scenario, which led to growth in China and Southeast Asia, will now become more balanced as companies look to reduce risk. Even before COVID-19 challenged the distribution of critical items, manufacturing goods closer to where they are sold had been recognized as a way for companies to achieve lower distribution costs. A tighter supply chain has the benefit of ensuring that quality standards can be met; it is also a safeguard for intellectual property.
A Thomas Industrial Survey conducted in April 2020 found 64 percent of manufacturers considered themselves “likely” to bring manufacturing production and sourcing back to North America. This represented a 10 percent increase in reshoring interest since Thomas’s March 2020 survey.
Some of the incentives that originally drove offshoring have declined in value or even disappeared. Manufacturers based in China have gradually experienced rising costs, especially labor costs. The Trump administration, prior to COVID-19, was focused on investing in apprenticeship programs, reducing regulations, and other pro-business measures.
A downstream benefit of bringing manufacturing back home is a likely jumpstart to the U.S. economy, especially if low-interest loans and tax incentives are available. Reuters has covered the Trump administration’s push to implement tax incentives and potential re-shoring subsidies. Several state commerce departments and regional economic groups are developing incentive packages and soft-landing programs for companies looking to reshore.
Kearney seventh annual Reshoring Index revealed a dramatic reversal of a five-year trend as U.S manufacturing in 2019 commanded a greater share compared to low-cost Asian countries. A new reshoring index developed by the Coalition for a Prosperous America (CPA) reported that the United States regained some of its manufacturing base in 2019, and the share of American-made manufacturing goods consumed in the U.S. market jumped significantly in 2019.
Special Challenges
One factor that drove offshoring in the 1990s was the rising cost of labor in the United States. Since that time, the skilled labor shortage made it harder to find and hire workers. Consequently, building resiliency and bringing manufacturing back to the United States will have to be concurrent with greater use of automation and robots.
Fortunately, U.S. manufacturers have already been investing in automation, robotics, and 3D printing, which will smooth the path for reshoring. For example, auto manufacturers are making use of robots with “vision” to accomplish detailed assembly work on the factory floor, as well as robots with long arms for welding and for coating/sealing. Electronics manufacturers also benefit from the precision robots offer, and the electronics industry has made some of the greatest strides in using automation, with tasks including additive manufacturing and 3D printed electronics.
The Thomas Industrial Survey found that one in four U.S. manufacturers were considering expanding industrial automation as a result of COVID-19.
The Reshoring Decision
Like most aspects of business and capital planning, addressing the unknowns one step at a time is the key to success. Individual manufacturers must conduct a comprehensive cost analysis of the overall benefits of reshoring. They must also consider advantages and disadvantages for every aspect of production.
A downstream benefit of bringing manufacturing back home is a likely jumpstart to the U.S. economy. Hidden costs are a factor. For example, environmental regulations, corporate tax rates, the extent of local infrastructure available to a given site, workforce factors, and more are important variables. Conversely, costs other than labor are relevant when assessing the benefits associated with offshore facilities. According to the Association for Manufacturing Excellence, “Most companies make sourcing decisions based solely on price, oftentimes resulting in a 20 to 30 percent miscalculation of actual offshoring costs.”
Fortunately, many resources are available to help owners and other decision-makers undertake the significant challenge of bringing manufacturing back from overseas. The Reshoring Initiative (RI) offers a free online tool, the total cost of ownership (TCO) estimator, which helps companies compare all relevant factors that will influence costs associated with offshoring, including overhead, balance sheet, risks, corporate strategy, etc.
The Import Substitution Program (ISP), also available through the Reshoring Initiative, helps importing companies produce or source more domestically. According to the RI, “Customized versions of ISP are available for U.S. manufacturing companies, technology suppliers, trade associations, economic development organizations (EDOs), and manufacturing extension partnerships (MEPs). Consistent use of the program would increase domestic manufacturing by about 10 percent.”
Part of the ISP (although it is also available “a la carte”) is the RI’s supply chain gap program. The RI has developed a list of “gaps,” where there is minimal domestic production and a large volume of imports. To participate in the program, manufacturers or EDOs work with RI to identify products that are most desirable to produce domestically. Domestic firms are identified and — assisted by the EDO and RI — supported during the process of opening a local factory.
Another resource is the Reshoring Institute, which has assembled a large body of statistics and research. The Reshoring Institute has invited states to provide economic profiles and descriptions of incentives offered in the state, improving the relevance to firms looking for location-specific reshoring information. The research is made available to the public at no charge.
The U.S. Economic Development Administration, a bureau within the U.S. Department of Commerce, has developed the Americas Competitiveness Exchange (ACE) program, which brings together up to 50 senior-level government, business, policy, and economic decision-makers from across the Americas. These experts establish productive partnerships and collaborations that make on-the-ground progress in developing manufacturing in the Americas.
Once a manufacturer has determined the advisability of updating or building a facility in (or near) the Americas, the company should partner with an industrial contractor during the earliest planning stages. An experienced contractor will have the knowledge base to help define the cost, schedule, and overall scope for a given project to help the owner achieve its desired outcomes.
When executed with caution, bringing all available knowledge to bear on the reshoring process, manufacturers may realize substantial gains by bringing facilities back from overseas. By extension, the entire U.S. economy — not to mention citizens’ welfare — may also reap benefits.
Project Announcements
Hartman Cabinetry Plans Jonesburg, Missouri, Operations
08/14/2025
eBliss Global Plans Utica, New York, Manufacturing Operations
08/14/2025
QTS Data Centers Plans Cedar Rapids, Iowa, Operations
08/14/2025
AbbVie Expands North Chicago, Illinois, Production Operations
08/13/2025
Land ‘N’ Sea Distributing Expands Norfolk, Virginia, Operations
08/13/2025
Arclin Expands Dillon, South Carolina, Operations
08/13/2025
Most Read
-
20th Annual Area Development Gold and Silver Shovel Awards
Q2 2025
-
What We’re Getting Wrong About Gen Z’s Future in the Skilled Trades
Q3 2025
-
A New Course for U.S. Shipbuilding
Q3 2025
-
Optimizing Your Rail-Served Transportation Network: Strategy Before Steel
Q2 2025
-
In Focus: AI Is Changing Incentives Math
Q2 2025
-
How to Choose the Right Site for Your Factory in 2025’s Volatile Landscape
Q2 2025
-
Reshoring Reality Check from Construction
Q3 2025