Workforce: A Primary Ingredient in the Evolution of the Food Industry
The global pandemic has accelerated changes occurring in the food and beverage industry, with a heightened focus on worker and consumer safety and automation technologies.
Q4 2020
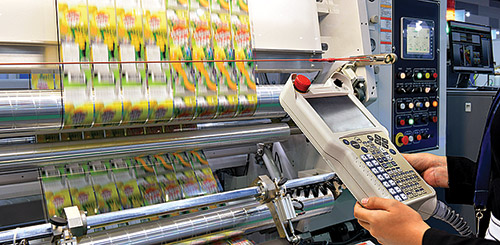
The food and beverage industry, in response, is transforming itself through increasing production times, changing technologies, heightened food safety regulations, and more in-facility work. This evolution has been in the works for some time now and shows no indication of slowing down.
Add COVID-19 to the mix, and this change is taken to an entirely different level, especially as it relates to supply chain disruption. Companies believe the majority of COVID-related changes are here to stay. Manufacturers are making long-term adjustments to support these demands.
Where Are the Workers?
One particular area of focus and concern for the industry is the workforce. Food Processing magazine’s annual survey released earlier this year points out the need for both skilled and unskilled workers. Part of this challenge is certainly due to the baby-boomers retiring, but other factors also exist.
Although M&A activity has slowed in the sector, it was strong for a few years and shook up the workforce with consolidation, and even attrition of specific roles. M&A activity also leads to early retirement and fear of job reduction, thus pushing workers to find jobs elsewhere.
The 2020 State of Food Manufacturing Survey Report from Food Engineering finds almost a quarter of processors stated their workforce decreased compared to last year due to workers leaving and the company not being able to replace them, or the company not being willing to replace them.
In short, workers are scarce, and as recent events have evidenced, the food and beverage sector is essential. The workforce shortage is creating a real challenge for the industry and forcing manufacturers to look to other means and resources to fulfill its growing needs and demands.
Automation to the Rescue
“There is an ongoing need for automation, and specifically artificial intelligence (AI), to help limit human exposure to infections and to enhance overall worker safety, speed, and predictability,” says Tyler Cundiff, president of Gray, Inc. Food & Beverage Market.
To augment the ongoing workforce challenges, food and beverage manufacturers are turning to automation methods to continue their production. Safety has always been paramount for processors, but COVID-19 has resulted in even stronger initiatives.
Automation technologies and strategies are answering the call to enhance safety and help reduce the risk of human cross-contamination. Processors must keep its employees safe in environments where social distancing isn’t always easy to implement.
Food Engineering validates this claim in its report stating that processors are turning to robotics for new safety requirements and staffing challenges, with 22 percent reporting plans to increase budgets in automation and controls hardware and software. Food and beverage manufacturers are rethinking how future plants are designed and built as well as how existing plants can be retrofitted to accommodate new trends that are likely to become standards.
Food Engineering’s survey also found that automation helps manufacturers maintain a competitive edge by speeding up production and efficiency.
The food and beverage industry is transforming itself through increasing production times, changing technologies, heightened food safety regulations, and more in-facility work. In our experience, we’re seeing food companies currently engaged in projects to redesign and retrofit existing employee welfare areas to be more accommodating for social distancing, cleaning, and personal hygiene protocols resulting from COVID-19 regulations and countermeasures.
Gray Solutions, Gray’s digital arm, is seeing process controls trending toward more integration of facility and utility controls systems. New processes are being designed with smart scheduling applications, where computer models schedule individual processing assets based on product run times, availability, total productive maintenance (TPM), and other real-time variables. Automation is continuing the trend toward full robotic solutions for high touch-point areas, sampling systems, and high-volume packaging systems, as well as AS/RS applications.
According to Anderson Dahlen Inc. — a Gray company that specializes in custom fabrication, contract manufacturing, and design-build projects — food processors are upgrading their production operations with increased safety measures, including automation functionality. Some of this is COVID-related, but many of these steps are expected to become permanent shifts to manufacturing processes.
One specific example is the addition of unloader systems for bins and totes. In recent months, Anderson Dahlen has seen a surge in inquiries for these systems since they eliminate manual labor and increase the rate at which inbound materials such as tomato paste and peanut butter can be moved into process. The integration of these systems greatly enhances sanitary procedures, thus creating a safer environment for workers and a safer product for consumers.
F&B Workforce of the Future
To meet the increased demands of the industry, hiring, training, and retaining workers is a must. While automation can fill a void, workers are still desperately needed to meet the challenges of today and tomorrow. For this, an education shift is necessary. Similar to other industrial fields, food manufacturing is still often associated with hard, rigorous labor. The truth is, automation has stepped in to alleviate many of these areas, but the perception for food and beverage manufacturing jobs is still very negative. Food and beverage facilities today are equipped with state-of-the-art robotics and machinery, many of which are run by human operators. Workers are needed to orchestrate the functionality of hardware, software, and tooling.
To augment the ongoing workforce challenges, food and beverage manufacturers are turning to automation methods to continue their production. Greater awareness through training programs and outreach is a necessary component to modifying the inaccurate perception of these careers. Schools that put a greater emphasis on science, engineering, and mathematic (STEM) studies can also push the trend in the right direction.
Gray is working with one of our beverage customers on a new production facility where automation technologies are coupled with an intentional strategy to operate the facility (when complete) with a highly productive workforce. Highly technically-trained employees operate the sophisticated systems and software ensuring the plant runs a safe and highly efficient operation.
In Sum
To sum it up, the workforce is shifting along with the industry. This year alone has brought challenges that no one could predict or prepare for, yet the industry has continued to thrive. Looking ahead, more change will inevitably occur, but I have no doubt that this resilient industry will continue to push itself forward and grow.
“U.S. food companies have had to make sweeping changes to the entire global food delivery system almost overnight, while at the same time maintaining focus on ongoing challenges such as sustainability, food safety, health and wellness, along with their own (front line) employee safety,” points out Cundiff. “These have been MASSIVE challenges. Farmers, processors, and distributors have stepped up to meet these challenges with an eye toward the future to ensure that we will be even better prepared for the next global disruptor, such as the COVID pandemic.”
Cundiff concludes that he has “seen firsthand that during this dynamic time food companies have had to rely on trusted partners throughout all aspects of the industry to help them adjust and recalibrate extremely complicated dynamics that exist within an intricate supply chain system.”
For more information, go to www.gray.com
Project Announcements
Pilgrim’s Plans LaFayette, Georgia, Operations
08/12/2025
Canada-Based Vibrant Health Products Plans Rossville, Tennessee, Manufacturing Operations
08/01/2025
Turkish-Based Kervan USA Expands Lehigh Valley, Pennsylvania, Operations
07/24/2025
Lactalis USA Upgrades Walton-Buffalo, New York, Production Operations
07/18/2025
Fine Organic Industries Limited Plans Jonesville, South Carolina, Operations
07/14/2025
Wayne-Sanderson Farms Establishes Danville, Arkansas, Feed Mill Operations
07/11/2025
Most Read
-
What We’re Getting Wrong About Gen Z’s Future in the Skilled Trades
Q3 2025
-
A New Course for U.S. Shipbuilding
Q3 2025
-
Optimizing Your Rail-Served Transportation Network: Strategy Before Steel
Q2 2025
-
In Focus: AI Is Changing Incentives Math
Q2 2025
-
How to Choose the Right Site for Your Factory in 2025’s Volatile Landscape
Q2 2025
-
Reshoring Reality Check from Construction
Q3 2025
-
The New Math Behind Mexico and U.S. Manufacturing Decisions
Q2 2025