What Does Industry 4.0 Mean for U.S. Manufacturing?
The Fourth Industrial Revolution is transforming global production and supply chains, but the future depends on how well the industry’s human leaders can understand its machines.
Q1 2018
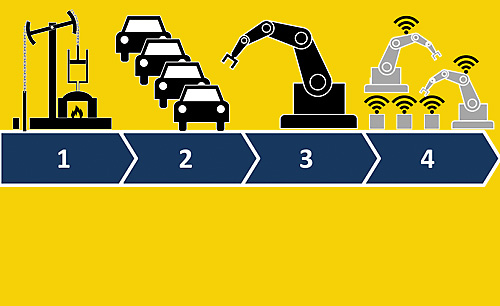
All this has become possible in just the few short years since the Fourth Industrial Revolution began. So what does the future of Industry 4.0 spell for U.S. industrial leaders?
For one, it means an opportunity to ramp up productivity and profit. By 2020, Gartner analysis predicts Internet of Things (IoT) technology will be in 95 percent of electronics for new product designs. For industrial leaders who can master these new tools, this means the chance to boost productivity by as much as 30 percent, fuel predictive maintenance, and ultimately generate all-new sources of revenue, according to Accenture.
To date, U.S. production structure, innovation, and a culture of automation make its industrial sector “well positioned for the future,” according to the World Economic Forum’s (WEF) 2018 Future of Production assessment. It was here, after all, that the moving assembly line originated, and it is here, too, that a mere two in five industrial employees are directly involved in hands-on production. Yes, the U.S. is already home to one of the key resources needed to drive successful technology adoption: a skilled and educated workforce.
And yet, the U.S. share of global manufacturing value has declined over time, from 29 percent in the early ’80s to 18.6 percent in 2015, with slower growth than seen in China, South Korea, Germany, and Mexico. To maintain its competitive edge in the global arena, the U.S. will need to ensure both its machines and its people become even more productive.
U.S. production structure, innovation, and a culture of automation make its industrial sector well positioned for the future. World Economic Forum’s (WEF) 2018 Future of Production assessment Disrupting Warehouse Design Now, With All New Levels of Connectivity
When the full gamut of material-handling and production systems can be connected and automated — from loading/offloading trucks and organizing inventory, to preparing synthetic goods — then the industrial facilities that house them can be configured differently, too.
For instance, when human safety (and height) is not a concern, warehouses can grow up, rather than out. Adding floors to distribution facilities in pricy urban markets can help add capacity in a key market without the need to invest in more land. U.S. developers are staying ahead of this curve, so far, with the average ceiling height for a Class A distribution center moving well beyond 32 or 36 feet clear.
Increased automation also means aisles can be made narrower, since humans and human-driven lift trucks won’t have to worry about freely and safely navigating around the shelves. Once upon a time, the space between columns averaged 30 feet, whereas today we’re looking at an average hovering around 54 feet — which of course means more storage capacity in the same space.
Human-free warehouses and factories are still a long way off, however, making strong human-machine collaboration a must-have in today’s industrial buildings.
Humans, Meet Data
The U.S. manufacturing sector is the second-largest in the world, with a manufacturing value added (MVA) of nearly $2 trillion in 2016, according to the WEF report cited above. The report describes the nation’s assets, including American’s ability to innovate and leverage the emerging technologies of the Fourth Industrial Revolution, while attracting and retaining advanced human capital.
Indeed, IoT-fueled automation and robotics are already being used to spare personnel from time spent on more menial tasks, while at the same time creating new need for human interpretation. This interpretation piece is critical, considering the volumes of new data now deluging the industry. The ability to measure processes in far greater detail, along with more rigorous KPI (Key Performance Indicator) quantifications, is a game-changer from an industrial real estate perspective. Robotics and automation are changing the way we work by taking on some of the workload and improving safety, focus, and productivity. They also bring in more information than current analytics platforms can reasonably handle.
Data points are flooding supply chain networks throughout the production and distribution cycles, from materials sourcing to equipment efficiency, and humans are still needed to make sense of as much of it as possible. This, in turn, makes tech-savvy talent a must-have — and tech-forward cities a must-have location.
By 2020, Internet of Things (IoT) technology will be in 95 percent of electronics for new product designs. Gartner analysis Cities where skilled STEM talent is nurtured and easily found are, therefore, likely to retain their appeal, including established innovation hubs like the San Francisco Bay Area, Boston, or the Research Triangle in North Carolina. But other markets could also fare well where civic leaders are successfully championing smart-city principles, investing in economic development, job training, and academic initiatives. Austin, Denver, Pittsburgh, Detroit, and Cincinnati, for example, are all emerging hotspots in the tech-talent world, and other municipalities are also working to actively train and nurture up-and-coming tech talent.
At this point in time, winning with technology still means winning over those who can master it. That’s true for today’s capabilities, as well as for whatever advance may be coming down next in the pipeline. As AI, augmented reality, and predictive analytics technologies improve, expect more emphasis on the human-machine interface. And as more people begin to work alongside more (and more sophisticated) machines, the highly centralized production model of the past will be upended even further, in favor of a more decentralized, collaborative environment unlike anything we’ve seen in the past.
Room for Improvement on the Road Ahead
To stay ahead through Industry 4.0, manufacturing and supply chain leaders must continue to invest in advanced technologies and human capital. But there are other areas of opportunity, too. While the WEF ranks the U.S. highly — top five or better — in most categories, it does indicate improvement is needed in areas like institutional framework (based on regulatory uncertainty and legal systems) and sustainability (based on the impact of production on the environment).
Industry 4.0 could take manufacturing and distribution to all new heights of efficiency and innovation than ever before. Key to fulfilling that potential, however, will be the human understanding of what is possible, and what is not, in the fast-changing Internet of Things.
Project Announcements
AMfg Labs Expands Belmont County, Ohio, Production Operations
11/25/2024
Shapeways Holdings Expands Livonia, Michigan, Operations Complex
07/07/2023
Germany-Based Becker Robotic Equipment Plans Canton, Georgia, Manufacturing Complex
12/07/2022
LEGO Group Plans Chesterfield County, Virginia, Manufacturing Plant
06/17/2022
Scotland-Based PowerPhotonic Plans Sahuarita, Arizona, U.S. Headquarters-Production Campus
04/04/2022
A. Duie Pyle Plans Manassas-Richmond-Roanoke, Virginia, Cross Dock Service Centers
03/15/2022
Most Read
-
20th Annual Area Development Gold and Silver Shovel Awards
Q2 2025
-
First Person: Joe Capes, CEO, LiquidStack
Q2 2025
-
The Legal Limits of DEI in Incentives Agreements, Hiring, and Contracting
Q2 2025
-
From Silicon to Server: Mapping the Data Center Supply Chain
Q2 2025
-
39th Annual Corporate & 21st Annual Consultants Surveys: What Business Leaders and Consultants Are Saying About Site Selection
Q1 2025
-
Rethinking Life Sciences Site Selection in a Resilient and Dynamic Market
Q2 2025
-
First Person: David Robey, Co-CEO of QTS Data Centers
Q2 2025