According to a 2012 survey of business leaders by Boston Consulting Group, 57 percent of all respondents indicated the top factor driving future location decisions is cost of labor. This was also the number-one factor in the site and facility planning decisions of more than 90 percent of those responding to Area Development’s 2012 Corporate Survey. “There is no question that the true balancing act in site selection involves maximizing labor and skill set value-add, while minimizing the cost functions surrounding it,” says Thomas Stringer of Business Advisory Services, Ryan & Company.
“Labor tends to dominate the equation for most of our site selection projects,” agrees John Boyd, principal for The Boyd Company, a site selection consulting firm in Princeton, N.J. “In particular, what varies the greatest are the nonexempt labor costs — typically hourly positions — that fall under federal wage and hour legislation mandating overtime compensation. Exempt salaries — those positions in supervisory or management — tend not to vary significantly by geography.”
Costs of being unionized
“Right-to-work” states typically have lower wages and are less unionized — two factors that are highly attractive to manufacturing companies. About half the states are right to work — in December 2012 Michigan became the 24th right-to-work state.
According to reporting by The Wall Street Journal, “Private-sector employees in right-to-work states earned an average of $738.43 a week in the past 12 months, 9.8 percent less than workers in states without such laws; according to Labor Department data, that didn’t include healthcare and other benefits.” As might be expected, manufacturing employment grew 4.1 percent in right-to-work states over the past three years, compared with less than 3 percent in other states. However, some economists also say that, when differences in cost of living are taken into account, wages are roughly the same — or even higher — in right-to-work states.
Labor Productivity
The Economics and Statistics Administration (ESA) indicates that American workers continue to increase their productivity. U.S. unit labor costs dropped nearly 17 percent between 2000 and 2011, meaning that productivity rose faster than labor costs. “This is not the situation in many countries that historically have been considered attractive destinations for outsourcing,” states ESA economist David S. Langdon. “In the case of China, for example, wage increases have easily outpaced labor productivity growth. As a result, economy-wide unit labor costs in China have ballooned by more than 85 percent since 2000. Canada and South Korea also face rising unit labor costs, with gains of 21 percent and 9 percent, respectively.”
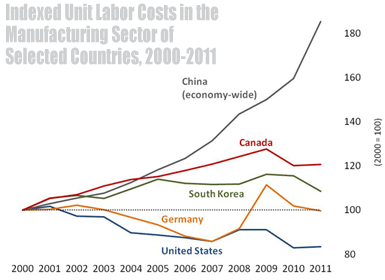

Source: Economics and Statistics Administration analysis of data from Bureau of Labor Statistics, International Labor Comparisons program and National Bureau of Statistics of China"
Langdon agrees. “Some companies have found the expected savings from foreign labor have been whittled away over time in numerous and unexpected ways,” he notes. “For example, specialized footwear manufacturer Keen cited the changing dynamics of overseas labor costs as key in its decision to expand its U.S. manufacturing operation.”
Most companies, adds Larry Gigerich, managing director for Indianapolis-based site selection firm Ginovus, are not strictly chasing the lowest labor costs they can find in a given location. “There is a balance between affordable labor costs and quality of the employee’s work,” he says. “Companies can certainly pay lower wages, but they are then typically faced with higher turnover, quality challenges, and significant internal training costs. Labor costs are an important factor, but they should be analyzed as a part of other operating costs such as tax rates, utility costs, transportation costs, and real estate costs.”