Infrastructure and Logistics Advantages Drive Facility Location Decisions
July 2011
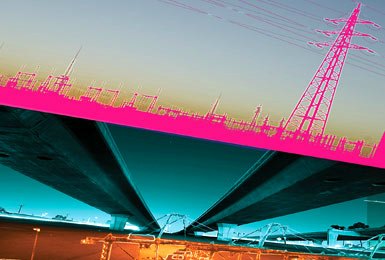
Behind all of this magic is a cloud-colored building in Maiden, N.C., covering half a million square feet and worth about a billion dollars. There's a reason Apple's new data center is where it is - infrastructure. Sure, it helps that the land in the tiny town was reasonably priced, and the generous tax breaks and lightning-fast permitting were pluses. But among the biggest factors that lured the Silicon Valley giant to a sleepy part of North Carolina are the high-tension wires stretching across the back of the property, bringing in lots and lots of reasonably priced electricity.just what a power-hungry data center really needs.
The story was much the same in Lenoir, N.C., not even an hour away. That's where Google planted a $600 million data center. Also not far away in Forest City, N.C., Facebook is building yet another high-profile data center. And word is that Disney Worldwide Services recently lined up land in what is fast becoming known as the "Google-Apple Corridor" for a data center of its own.
It's a striking example of the importance of infrastructure in location decision-making. These sites that are all over the high-tech news lately are not in big population centers, not on interstate highways or major waterways. Their proximity to rail lines and major airports - or lack thereof - is of no consequence. But they have access to the kinds of infrastructure required by data centers: cheap, reliable power and strong data connections.
Those data connections are of ever-increasing importance, observes Lewis Feldman, partner in the business law department of Los Angeles-based Goodwin Procter and a specialist in large real-estate deals. "One of the biggest questions is the cost of information and the amount of information that you can move," he says. "Information is ground zero for economic development." That's certainly true for data centers, but in reality, it's true for just about everything, notes Anthony Figliola, vice president of operations for Empire Government Strategies, a New York lobbying organization. Even a manufacturing operation these days may need solid data links to the supply chain as well as to downstream customers.
Attention to newer types of infrastructure needs is helping communities across the country to increase their economic development relevance. Consider the Indiana community of South Bend, situated right in the middle of the Rust Belt, with a long history of making durable goods from Studebakers to military vehicles. Today, it's emerging as a hot spot for data centers, thanks to strong data links and attention paid to the needs of technology businesses. Earlier this year, Data Realty LLC announced plans to build a data center at Ignition Park, a technology park that happens to sit on the same piece of real estate where Studebakers were once assembled. The city already has six commercial data centers serving customers across the Midwest.
More Traditional Infrastructure
That's not to say that more traditional varieties of infrastructure have lost their importance or influence. One of the world's oldest infrastructure types, water transportation, has been crucial to the success of a $3.8 billion modernization project at BP's refinery in Northwest Indiana. It's a project proceeding on a massive scale, and some of its key components have been shipped in from overseas by way of the St. Lawrence Seaway. Some materials have arrived at the Port of Indiana, others at a special 54-acre barge dock BP built just for this purpose on land leased from a nearby steel mill. According to BP officials, having port facilities nearby is critical because some components are so highly specialized that they can only be sourced internationally - and they are so huge that they have to come by ship or barge.
Kia Motors faced a similar situation working on an expansion at its Kia Motors Manufacturing Georgia Inc. facility in West Point, Ga. The project called for shipments of special machinery from Korea, including pieces weighing up to 170 tons. The equipment was shipped from Pyeongtaek, South Korea, to the Port of Savannah and hauled 300 miles across the state, a feat that required special logistical arrangements including a fleet of trailers and trucks. The components are being assembled into steel-stamping machinery that will turn out various vehicle body panels and support 1,000 new jobs, and state officials say they're glad to have invested in the transportation and logistics infrastructure that made the expansion possible.
Of course, as it always has been, highway access remains a key infrastructure issue driving many development projects, such as the Canon U.S.A. Americas headquarters being built on a former pumpkin farm along the Long Island Expressway in Melville, N.Y. Observes Figliola, the transportation requirements of large groups of people can be just as big a challenge as directing truck traffic at a distribution center: "How do you get more than 2,500 people in and out of the facility?"
In order for the project to move forward, millions of dollars in road improvements have been required, allowing construction access as well as making way for the thousands of Canon employees who'll be based there when it opens.
"Infrastructure is incredibly important to most companies when considering where to develop and expand," Figliola notes, with requirements ranging from roads to more robust sewers. "Manufacturers and distribution businesses need to be close to main thoroughfares to easily transport their products in and out of the region quickly, and most regions require sewage systems to increase the density of the building."
Transportation and logistics infrastructure advantages also are among the factors that persuaded Electrolux to pick Memphis for its new North American Cooking Products manufacturing center, according to Figliola. The company expects to begin transitioning production into the 700,000-square-foot facility in 2012.
Project Announcements
Local Bounti Plans Pasco, Washington, Indoor Agricultural Operations
04/26/2024
Innovative Construction Group Plans Siler City, North Carolina, Production Operations
04/26/2024
Crystal Window and Door Systems Plans Mansfield, Texas, Headquarters-Production Operations
04/25/2024
JDSAT Expands Fairfax County, Virginia, Operations
04/25/2024
Trussworks Mid-America Plans Jackson, Missouri, Manufacturing Operations
04/25/2024
Epic Flight Academy Establishes Hebron, Kentucky, Operations
04/25/2024
Most Read
-
2023's Leading Metro Locations: Hotspots of Economic Growth
Q4 2023
-
2023 Top States for Doing Business Meet the Needs of Site Selectors
Q3 2023
-
38th Annual Corporate Survey: Are Unrealized Predictions of an Economic Slump Leading Small to Mid-Size Companies to Put Off Expansion Plans?
Q1 2024
-
Making Hybrid More Human in 2024
Q1 2024
-
Manufacturing Momentum Is Building
Q1 2024
-
20th Annual Consultants Survey: Clients Prioritize Access to Skilled Labor, Responsive State & Local Government
Q1 2024
-
Public-Private Partnerships Incentivize Industrial Development
Q1 2024