Energy Efficient Facilities Make Good Business Sense
Making your plant more energy-efficient through low- or no-cost measures as well as capital improvements makes good environmental as well as business sense.
Dec/Jan 10
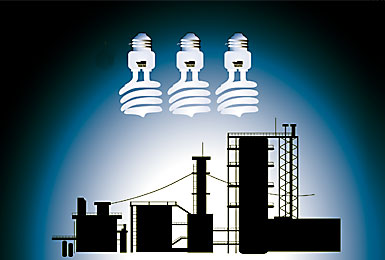
In addition to the "green" benefits of reducing energy consumption, e.g., reducing the site's carbon footprint, the savings that result make this a good business decision. Many energy-reducing retrofits to existing equipment and systems pay for themselves inside of four years, and they provide ongoing cost savings over their useful lives. With an increased emphasis on the environment, the focus on green technology has made it easier than ever to identify and implement efficiency upgrades, beginning with no-cost improvement measures your maintenance staff can implement quickly to those requiring a long-term investment. Here are some key steps to follow:
Get an Accurate Picture: You Can't Change What You Don't Know
The first step in deciding which areas of a plant can be updated is to measure and monitor each facility's energy consumption tied to manufacturing activities. Many plants can do this by pulling together their own metrics, including square footage and hours of operations, and relating this to historical energy cost and consumption information contained on utility bills.
Frequently, manufacturers can avail themselves of real-time energy-usage information by way of a "smart meter." If you aren't sure if your plant has one, contact your local electric utility for more information. For some plants, and for some processes, more detailed information may be warranted. In this case, the plant can install sub-metering to get detailed consumption tracking data on a particular process or system, such as a compressed air plant.
It is important not only to analyze energy consumption, but also to align this information with production metrics. Ask whether or not energy is being put to use efficiently - Is consumption directly necessary to generate production? Many times other information can provide clues on items that might need further investigation; for example, a dramatic increase in maintenance costs for a piece of equipment or system can suggest a problem. It is important to look at the whole picture.
Consider the following scenario: A foundry uses natural gas to heat its boilers; the number of maintenance requests concerning the boilers has increased, while the cost of natural gas has not. This may not set off any energy-efficiency alarms at first, but when coupled with the cost of maintenance and downtime, these boilers are now presenting a big efficiency opportunity that might be realized by replacing them with new equipment.
However you do it, you must have an accurate snapshot of what your plant is consuming, when, and where before you decide where to pursue potential efficiency upgrades. Start with an analysis of at least the last year; you'll want to be able to make an evaluation of the significance of weather and the seasonality of some energy sources such as natural gas.
Decide What's Critical and Set Achievable Goals
By analyzing your energy consumption metrics, some of the most critical areas of concern will reveal themselves immediately. Your snapshot will afford you the ability to effectively identify opportunities for savings from improvements, modernizations, and tweaking some routine plant processes that might easily be improved.
Opportunities generally sort themselves into two kinds of buckets - those that require capital investment and the associated analysis and approval, and those that don't. The latter low- or no-cost upgrades are often a great place to start because they can be accomplished quickly with mostly internal resources, and without major investments.
Retro-commissioning - the process of commissioning an existing building - offers owners and operators a way to improve building efficiency, thereby reducing energy consumption over time and lowering operating costs. Retro-commissioning can occur on any scale, including in a manufacturing environment. It involves the optimization of existing equipment and systems, specifically those that move air, water, and compressed air around your plant. The retro-commissioning field is growing, and it may be a good idea to start your efforts by finding a qualified firm to do this work in conjunction with your plant personnel.
Capital investments can offer significant opportunities to reduce costs while going green. From new high-efficiency lighting systems to variable speed drives, to more efficient chillers and boilers, many technologies can be deployed to reduce consumption and costs. It is important to understand the internal processes and procedures for evaluating capital expenditures at your site before you proceed along these lines. Make sure the people who make these decisions understand the soundness and certainty associated with energy-efficiency investments, and be prepared to have a plan in place to "prove out" the savings over time.
In any case, it is a good idea to dedicate a team or task force to monitor progress, establish goals, and maintain accountability of an efficiency program. Whether it is an outside group or a handful of employees on a task force, establishing an authoritative body to identify weaknesses and maintain the integrity of your investment is a good step when deciding what is critical and how it fits into your company's operational goals.
Project Announcements
Apex Plastics Opens Expanded Production Plant In Brookfield, Missouri
09/22/2014
Japan-Based Bridgestone Rubber-BSA Opens Biorubber Process Research Center In Mesa, Arizona
09/22/2014
SpencerARL Expands Its Plattsburgh, New York, Manufacturing Facility
09/22/2014
Hill International, Inc. Relocates Corporate Headquarters To Philadelphia, Pennsylvania
09/22/2014
Prysmian Group Plans $8.2 Million Expansion At Abbeville County, South Carolina, Manufacturing Center
09/22/2014
Japan-Based Kowa Kentucky Plans $8.3 Million Manufacturing Facility In Corbin, Kentucky
09/22/2014
Most Read
-
20th Annual Area Development Gold and Silver Shovel Awards
Q2 2025
-
First Person: Joe Capes, CEO, LiquidStack
Q2 2025
-
The Legal Limits of DEI in Incentives Agreements, Hiring, and Contracting
Q2 2025
-
From Silicon to Server: Mapping the Data Center Supply Chain
Q2 2025
-
Rethinking Life Sciences Site Selection in a Resilient and Dynamic Market
Q2 2025
-
39th Annual Corporate & 21st Annual Consultants Surveys: What Business Leaders and Consultants Are Saying About Site Selection
Q1 2025
-
First Person: David Robey, Co-CEO of QTS Data Centers
Q2 2025