How U.S. Manufacturers Can Navigate the Route to the New Trade Policy
Manufacturers need to prepare now for prospective trade policy changes so that they may recalibrate their supply chains if need be.
Q3 2017
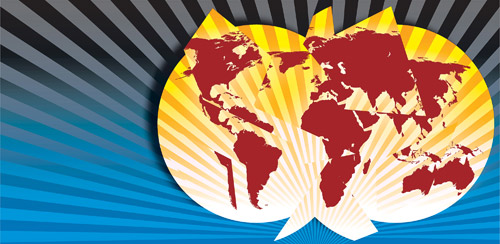
To navigate impending changes, manufacturers need to begin preparing now for the most practical scenarios, including the potential recalibration of their supply chains, reconsideration of where they produce and sell and, in some cases, consideration of whether the current business model even remains viable.
Regardless of the outcome around hot-button issues like the North American Free Trade Agreement (NAFTA) and the Trans-Pacific Partnership (TPP), there are three practical considerations that business leaders can focus on now to begin to adapt to, and even capitalize on, the global trade policies in flux.
Consideration #1:
What’s the imported content of my products?
A major focal point of the 2016 U.S. presidential election was the need to reprioritize domestic jobs. This is sure to be a major priority for policymakers as they look to reshape trade agreements. As such, it is important for manufacturers to understand exactly what components of their finished products contain imported elements. But this is easier said than done, thanks to the complexity of global supply chains. Take the auto industry, for example. With vehicles containing hundreds of parts, many of which are imported from global suppliers, it can be an onerous task to track down the origins of each nut and bolt. But as NAFTA’s rules of origin currently stand, tariffs are lifted for the auto industry as long as at least 62.5 percent of the value of autos, light trucks, engines, and transmissions originates in one or more of the three NAFTA countries. If the rules of origin levels are increased to encourage more domestic business (and discourage the importation of parts from non-NAFTA countries), it could be difficult for automakers to quickly adjust to the new requirements.
A major focal point of the 2016 U.S. presidential election was the need to reprioritize domestic jobs. The good news: manufacturers have time to implement changes now that will greatly help if and when we see an increase in these rules-of-origin levels. First, it will be critical for U.S. end-customers who import components to perform a deep and transparent accounting of where their parts are sourced. This will make the handling of any additional reporting requirements a much smoother process than having to start from scratch. This also allows time if more stringent requirements need to be imposed on suppliers to get accurate origin information from their supply chain.
It will also be critical to establish a more rigorous process of cataloguing the origin of all imported content and accurately assign the value for the parts. This becomes more difficult when accounting for components that have been shipped back and forth across borders, such as a raw material that is sent from the U.S. to Mexico, included in a component, and then exported back to the U.S. Spending the time now to fully understand these nuanced conditions will surely pay off in the long run.
Consideration #2:
Preparing for supply chain disruption
Once manufacturers have a clearer picture of the origination point of the components in their end products, and are able to accurately attach values to them, it is now time to consider if a reconfiguration of the supply chain is in order. Changes to NAFTA could cause complex shifts of cross-border supply chains and may result in an accelerated search for new suppliers in different jurisdictions and, in some cases, the need to look toward supplier networks that have the capability to implement a “build where you sell” model.
A shift away from NAFTA could also result in large multinational manufacturers significantly re-organizing their supply chains, which could have major effects on small and mid-sized suppliers. To meet these new demands, M&A targets and divestitures may also be a key strategy.
To prepare for the potential of having to rapidly deploy a new supply chain, manufacturers should consider forming a task force around operational supply chains to model how various trade policy scenarios would specifically affect their companies. Models and scenarios should be run around all countries with which the U.S. has existing trade agreements and where there might be new ones. While time-consuming, this in-depth planning will allow for manufacturers to build a range of possible supply-chain change scenarios that could occur in this current uncertain environment.
While the specifics of trade reform remain hazy, there have been signals in general directions that could help business leaders discern their vulnerabilities. Conducting stress tests on their supply chains is a critical component of the scenario planning. While the exact timing of the changes are not yet clear, it is likely that they will come swiftly. Therefore, it is key to make sure that supply chains can withstand sudden trade policy shifts.
M&A may be one of the most efficient ways to rapidly adjust to new supply chain requirements. As the landscape may quickly become competitive and crowded, developing plans for M&A or strategic partnerships now is also important.
Besides the supply chain, it is important to understand how changes in trade policy could affect cross-border data flows and potentially force the localization of data. Preparing infrastructure and technology now to be nimble and adjustable will likely pay off in the future.
Consideration #3:
Preparing your plan B and C
While the specifics of trade reform remain hazy, there have been signals in general directions that could help business leaders discern their vulnerabilities. In order to get ahead, companies should identify potential red flags that affect their businesses and prioritize accordingly. It’s important to note that manufacturers of low-margin products may become particularly vulnerable if higher tariffs affect their imports from countries like Mexico and China. These companies could be in a Catch-22: it may be too expensive to source from both inside and outside the U.S., threatening the viability of their business model.
Building trade policy and government affairs teams that focus on prospective trade policy changes and anticipate the range of outcomes will provide a significant advantage for manufacturers. It is also important for companies to identify their biggest “country exposures” — those areas to and from which a company imports or exports a significant amount of product. Assessing and understanding geopolitical risks and how strained national relationships could affect their business are also key.
While U.S. industrial manufacturers remain in the dark about trade reform, their hands are hardly tied. By taking a proactive approach to not only understanding their organization from top to bottom, but also researching and planning their next moves carefully and strategically, they will be well prepared for the changes to come.
Project Announcements
Kikkoman Foods Plans Jefferson, Wisconsin, Operations
04/26/2024
BWX Technologies Expands Cambridge, Ontario, Nuclear Production Operations
04/26/2024
Greenheck Group Plans Knoxville, Tennessee, Operations
04/26/2024
Local Bounti Plans Pasco, Washington, Indoor Agricultural Operations
04/26/2024
Innovative Construction Group Plans Siler City, North Carolina, Production Operations
04/26/2024
Crystal Window and Door Systems Plans Mansfield, Texas, Headquarters-Production Operations
04/25/2024
Most Read
-
2023's Leading Metro Locations: Hotspots of Economic Growth
Q4 2023
-
2023 Top States for Doing Business Meet the Needs of Site Selectors
Q3 2023
-
38th Annual Corporate Survey: Are Unrealized Predictions of an Economic Slump Leading Small to Mid-Size Companies to Put Off Expansion Plans?
Q1 2024
-
Making Hybrid More Human in 2024
Q1 2024
-
Manufacturing Momentum Is Building
Q1 2024
-
20th Annual Consultants Survey: Clients Prioritize Access to Skilled Labor, Responsive State & Local Government
Q1 2024
-
Public-Private Partnerships Incentivize Industrial Development
Q1 2024