Made in the USA: Shoring Up Options for U.S. Manufacturing’s Resurgence
With the right planning, investors and occupiers have a unique opportunity to reshape the future of the U.S. and Americas-wide manufacturing sector.
Q4 2023
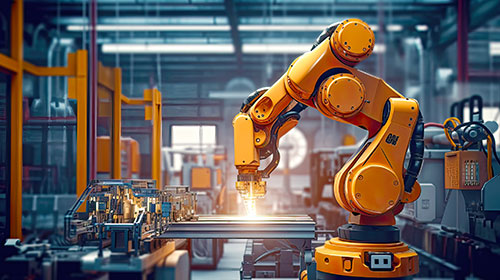
This raises the question, is the U.S. ready for a manufacturing renaissance?
With revived efforts to begin reshoring and nearshoring manufacturing to and toward the U.S., several challenges have surfaced, namely the lack of available manufacturing space, labor and talent shortfalls, as well as significant infrastructure improvements required for much-need supply chain efficiency and, ultimately, success.
According to Cushman & Wakefield Research, U.S. manufacturing vacancy currently sits at a tight 2 percent, and with only 59.9 msf under construction, leasing conditions for occupiers who have yet to secure facilities will prove to be challenging in the near term.
Reshoring and manufacturing job announcements exceeded 360,000 in 2022, a record-breaking 53 percent increase from 2021. Yet despite tight market conditions, in the first quarter of 2023, “reshoring” considerations announced on earnings calls by several S&P 500 companies were up 128 percent year-over-year. Further, reshoring and manufacturing job announcements exceeded 360,000 in 2022, a record-breaking 53 percent increase from 2021; and since 2020, private companies have announced $470 billion in manufacturing investments — in addition to the Biden administration’s $220 billion.
While encouraging, the recent boom in investment has not necessarily translated to an outsized increase in jobs as the composition of U.S. manufacturing has evolved requiring a more diverse group of laborers and skillsets, such as highly skilled scientists and engineers — placing more pressure on an already strained labor market and headwinds for sustained expansion.
Aging infrastructure is another challenge facing the sector, as inventory tends to be older, with nearly two-thirds of it built before 1990, and nearly three-quarters built before 2000. Additionally, the American Society of Civil Engineers gave the nation’s infrastructure a C-minus grade on its 2021 quadrennial Infrastructure Report Card, citing that the nation is spending only half of what it needs to invest in infrastructure improvements to bring systems up to par.
Yet, with revived efforts to begin reshoring and nearshoring manufacturing to and toward the U.S., several challenges have surfaced. This is only counter-challenged by the fact that there are limited land options with sufficient power to support the development of new manufacturing sites, creating additional complexities for site selections, and limiting investment opportunities for investors and space for manufacturing users.
Despite these challenges, corporate interest in expanding manufacturing in the U.S. and in nearby countries will continue to drive new development. With the right planning and strategic analysis of the real estate including location analysis, supply chain optimization, and scenario planning, both investors and occupiers have a unique opportunity to make a transformative investment into reshaping the future of the U.S. and Americas-wide manufacturing sector.
Project Announcements
Kikkoman Foods Plans Jefferson, Wisconsin, Operations
04/26/2024
BWX Technologies Expands Cambridge, Ontario, Nuclear Production Operations
04/26/2024
Greenheck Group Plans Knoxville, Tennessee, Operations
04/26/2024
Local Bounti Plans Pasco, Washington, Indoor Agricultural Operations
04/26/2024
Innovative Construction Group Plans Siler City, North Carolina, Production Operations
04/26/2024
Crystal Window and Door Systems Plans Mansfield, Texas, Headquarters-Production Operations
04/25/2024
Most Read
-
2023's Leading Metro Locations: Hotspots of Economic Growth
Q4 2023
-
2023 Top States for Doing Business Meet the Needs of Site Selectors
Q3 2023
-
38th Annual Corporate Survey: Are Unrealized Predictions of an Economic Slump Leading Small to Mid-Size Companies to Put Off Expansion Plans?
Q1 2024
-
Making Hybrid More Human in 2024
Q1 2024
-
Manufacturing Momentum Is Building
Q1 2024
-
20th Annual Consultants Survey: Clients Prioritize Access to Skilled Labor, Responsive State & Local Government
Q1 2024
-
Public-Private Partnerships Incentivize Industrial Development
Q1 2024