Reducing Energy Consumption of Manufactured Goods
By obtaining technology and scientific grants, government performance contracts, and economic development support, innovative companies can quickly flourish.
Q2 2016
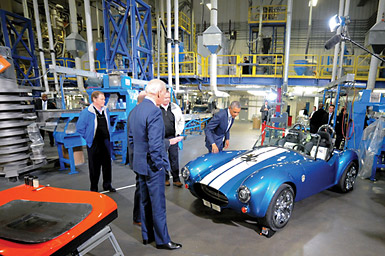
AD: Can you briefly describe the goals of the Advanced Manufacturing Office?
Johnson: Our mission is to enhance the competitiveness of U.S. manufacturing, and create high-quality domestic manufacturing jobs by reducing the life-cycle energy consumption of manufactured goods by 50 percent over 10 years. We are doing this by teaming up with industry, universities, companies, regional groups, and other stakeholders to identify and support the development of promising new clean-energy technologies. AMO also has a leadership role in the national interagency Advanced Manufacturing Partnership.
AMO staff work with our partners on several levels to identify technology platforms that have the potential to improve energy efficiency in manufacturing processes, or provide benefits for clean-energy products. AMO also helps fund early-stage R&D, typically through public-private partnerships, to identify and solve the research challenges that inhibit the development of these technologies. We also advise small businesses about adopting new technologies and improving their manufacturing practices, especially with regard to more efficient use of heat and power.
AD: How does AMO partner with the nation’s research labs to advance its mission?
Johnson: The Department of Energy manages 17 labs in its national laboratory system. Part of our job is to transfer innovative discoveries from our labs into the private sector for further development and commercialization. Federal partners include the National Institute of Standards and Technology, Department of Defense, Department of Commerce, National Science Foundation, and NASA, through the Advanced Manufacturing Partnership 2.0.
For example, we have funded research projects at Oak Ridge National Laboratory’s Carbon Fiber Technology Facility, a state-of-the-art, semi-production-scale carbon-fiber conversion plant. Researchers there have developed a production method that can reduce the cost of carbon-fiber as much as 50 percent, as well as reduce the amount of energy used in its production by more than 50 percent. These results will likely accelerate the use of carbon-fiber composites in high-volume industrial applications including automobiles, wind turbines, compressed gas storage, and building infrastructure.
AMO also supports the efforts of the National Network for Manufacturing Innovation (NNMI) through its Manufacturing Innovation institutes to identify and develop emerging technological advances for specific industries. For example, through our partnerships with the Department of Defense, the national labs are involved with several research projects in upstate New York at the American Institute for Manufacturing Integrated Photonics, an industry-driven public-private partnership that targets the photonic integrated circuit (PIC) sector.
AD: How are disruptive technologies like the Internet of Things and additive manufacturing/3D printing impacting U.S. manufacturing?
Johnson: The Internet of Things (IoT) is crucial for improving energy efficiency in manufacturing sectors. Advanced sensors and controls embedded in equipment provide real-time data that give operators a better understanding of how equipment operates, including identifying areas where energy efficiency can be improved. IoT is also driving positive change in information management — the huge amounts of data being generated can be analyzed using new algorithms that improve the efficiency of manufacturing processes.
Additive manufacturing (AM) and 3-D printing are revolutionizing the manufacturing space. An increasing number of materials can be printed, including metal. Sophisticated 3D printers can print parts and products that cannot be manufactured in any other way. 3D printing can also be used to improve the supply chain and operations. Tooling for manufacturing, for example, can be expensive and time-consuming — it can take up to 12 weeks to make a tool. However, a 3D printer can turn out that tool in a single day. Printing parts on site is another way to shorten the supply chain and deliver the end product faster. Wind turbine blades, for example, are normally too big and expensive to ship. With 3D printing, they can potentially be made on site, saving time and money and speeding up construction.
Perhaps the most impressive 3D printing accomplishment is a new additive manufacturing tool created through a partnership between Oak Ridge National Laboratory and Cincinnati Incorporated. Called the Big Area Additive Manufacturing machine (BAAM), this system is 500 to 1,000 times faster, and capable of printing polymer components up to 10 times larger, than today’s industrial additive machines. This equipment was used to 3D print a fully functional replica of a Shelby Cobra automobile in six weeks. The machine printed the car from the bottom up using thermoplastic resin and carbon fiber, which are lighter weight than metal or aluminum. Because the BAAM technology is also scalable, we will be able to make even larger components in the future.
AD: HPC4Mfg (High Performance Computing for Manufacturing), one of your newer programs, involves the use of Department of Energy supercomputers. How does this program work?
Johnson: Five of the top 12 supercomputers in the world are owned by the Department of Energy. The HPC4Mfg initiative, which we started in March 2015, is part of the department’s Clean Energy Manufacturing Initiative. Research partners can use these high-performance computing systems to work on modeling, simulating, and analyzing cutting-edge industrial products and processes, giving them a resource that no international competitor can match. The program is directed by Lawrence Livermore National Laboratory, with strong support from Lawrence Berkeley National Laboratory and Oak Ridge National Laboratory.
Funding is provided to companies that are inventing potentially disruptive clean-energy technologies, with the hope of dramatically reducing production costs and shortening time to market for these innovations. HPC4Mfg is currently supporting 15 projects that range from improved turbine blades for aircraft engines and reduced heat loss in electronics to improved fiberglass production. Each project has received up to $300,000 for a total of nearly $4.5 million.
AD: What is on the horizon for AMO over the next few years?
Johnson: We will continue to focus our efforts on solving technical problems relative to the energy space, and transferring these R&D successes as quickly as possible into the marketplace. Collaboration with engaged and active partners is critical for our success. With HPC4Mfg, for example, partners include the Edison Welding Institute, General Electric, GlobalFoundries, the National Network for Manufacturing Innovation’s Lightweight Innovations for Tomorrow consortium, the Ohio Supercomputer Center, Procter & Gamble, PPG Industries, United Technologies Research Center, and ZoomEssence. We will also look forward to partnering with more NNMI institutes as they come online in the near future.
AD: What accomplishment so far best represents the partnership between AMO and U.S. manufacturing?
Johnson: The Shelby Cobra — The first version of a 3D printed, all-electric vehicle using Big Area Additive Manufacturing (BAAM) technology looked like a typical prototype, with a rough surface. To achieve a high-quality surface finish, the engineering team worked with a local auto body shop, Tru-Design, LLC, to develop a new process for bonding and painting, based on the car’s chemistry. This process will now likely be a model for future large-scale 3D-printed vehicles and products. By sharing his expertise with the Oak Ridge team, the owner of this small business is now hiring scientists and growing the company in a way he had not previously envisioned. This just shows that, with shared vision, we can do great things when we work together.
Project Announcements
Germany-Based Becker Robotic Equipment Plans Canton, Georgia, Manufacturing Complex
12/07/2022
LEGO Group Plans Chesterfield County, Virginia, Manufacturing Plant
06/17/2022
Scotland-Based PowerPhotonic Plans Sahuarita, Arizona, U.S. Headquarters-Production Campus
04/04/2022
A. Duie Pyle Plans Manassas-Richmond-Roanoke, Virginia, Cross Dock Service Centers
03/15/2022
Black Buffalo 3D Corporation Relocates-Plans Smithfield Township, Pennsylvania, Manufacturing Complex
02/07/2022
Cooperative Response Establishes Kirksville, Missouri, Operations Center
02/03/2022
Most Read
-
2023's Leading Metro Locations: Hotspots of Economic Growth
Q4 2023
-
2023 Top States for Doing Business Meet the Needs of Site Selectors
Q3 2023
-
38th Annual Corporate Survey: Are Unrealized Predictions of an Economic Slump Leading Small to Mid-Size Companies to Put Off Expansion Plans?
Q1 2024
-
Making Hybrid More Human in 2024
Q1 2024
-
Manufacturing Momentum Is Building
Q1 2024
-
20th Annual Consultants Survey: Clients Prioritize Access to Skilled Labor, Responsive State & Local Government
Q1 2024
-
Public-Private Partnerships Incentivize Industrial Development
Q1 2024