The historic level of private investment has been catalyzed in part by multiple pieces of federal legislation — the Infrastructure Investment and Jobs Act, Inflation Reduction Act (IRA), and now CHIPS and Science Act — aimed at strengthening the ecosystem for all things EV and, more broadly, green energy. Rather than spurring new ventures, these federal programs appear to be adding fuel to accelerate the pace of activity.
Even with historic tailwinds, as new factories are constructed and commissioned, EV and battery producers face challenges on several fronts that threaten to complicate or delay full ramp-up, including significant supply chain constraints. Furthermore, these projects are creating impacts that reach far beyond auto manufacturing and are accelerating a generational shift under way in the U.S. manufacturing landscape.
Here’s what EV executives are watching for 2024 and beyond:
Mining
Generally speaking, the highest value EV components are the materials comprising the battery’s cathode, which typically contain some combination of nickel-manganese-cobalt (NMC), lithium-iron-phosphate (LFP), or occasionally lithium-cobalt-oxide (LCO), lithium-nickel-cobalt-aluminum-oxide (NCA), or other formulations. This component, a relatively small part of the vehicle by total weight, dictates the battery’s range, temperature control, and other performance qualities. While NMC is generally understood to have a higher storage capacity and affords a better mileage range, lithium is more widely and cheaply available, leading some automakers to shift to lithium-based batteries.
As new factories are constructed and commissioned, EV and battery producers face challenges on several fronts that threaten to complicate or delay full ramp-up. Regardless of the exact battery formula adopted by a particular OEM, the critical mineral supply chain has been brought to the forefront of the EV world, in part by the IRA’s requirement that in order to qualify for the generous EV subsidies, automakers must procure significant percentages (80 percent by 2027) of EV components by value from U.S. suppliers or under a free trade agreement. This has spurred a flurry of activity in the mining and chemicals sector as automakers and battery producers jostle for long-term supply contracts for key battery material components.
This dynamic has forged some interesting partnerships with unlikely bedfellows: mining companies and automakers. GM inked a deal in January 2023 with Canadian company Lithium Americas for exclusive rights to lithium mined from the remote Thacker Pass in Nevada; Ford has announced plans to purchase a stake in an Indonesian nickel mine; and Stellantis is investing in an Argentinian copper mine. Mining is still a notoriously risky, boom-and-bust industry, hardly known for the stability or price controls that are hallmarks of the automotive industry, and it remains to be seen how these partnerships and joint ventures will play out.
Trade
Exacerbating supply issues are new trade restrictions imposed on exports of key minerals. Developing nations, rich in natural resources but historically challenged by development and governance issues, are moving to protect their resources and demanding a larger share of EV investment in materials processing in return.
In 2020, Indonesia banned the export of unprocessed lithium, leading to billions of dollars of investment in processing capacity, even while the ban has been declared a violation of trade norms by the WTO. In February, Mexico nationalized lithium reserves and awarded control of their processing to the nation’s energy ministry. Several African and Central/South American countries are signaling tightened state control over exports of lithium and other critical mineral reserves are ahead. Producers of battery materials in search of long-term supply relationships must successfully navigate these challenges or find new resources in other countries.
As the consumer shift to EVs continues, a key area of continued growth will be in recycling capacity for end-of-life batteries. Utility Constraints
Most of the EV-related projects announced in the past several years have significant electric utility requirements amounting to thousands of megawatts in added new load. This comes at a time when both investor-owned and public utilities are managing their own decarbonization plans, shifting away from coal-fired generation, and integrating new renewable or natural gas assets. In many cases, this has stretched the capacity of existing electric generation and transmission resources.
This tremendous growth has caught up to the limits of our current infrastructure: transformers for new substations have an average 18–24+ month lead time from the manufacturer, limiting delivery of existing capacity to new parks and buildings. Grid interconnections are backlogged — several years in many areas — restricting the ability to bring new generation assets online.
For example, in Texas, the abundance of new wind and solar assets has threatened to overwhelm the existing transmission lines and actually exceeded demand during certain times, leading ERCOT to curtail generation from these assets — by 9 percent for solar and 5 percent for wind in 2022. This is also happening during a time when the U.S. population is shifting south — a slow trend accelerated by COVID in the past three years — further exacerbating the strain on electric capacity.
Consumer Adoption
Much of the investment by OEMs over the past several years has been predicated on the assumption that the transition to EVs is inevitable — still a big gamble, given the skepticism of many consumers. The EV adoption rate has grown exponentially, but — due to factors such as spotty charging infrastructure, vehicle and battery cost and range, and other factors — the total market share is still low at 5.7 percent in 2022. While that share of the overall market is projected to continue to grow in 2023 and beyond, automakers must prove to consumers that these new models not only function equally and reliably as internal combustion engines (ICE) did, but also provide an improvement over the current models.
Some automakers are betting instead on a hybrid path forward: EV and ICE models. Several new southeastern OEM facilities are being designed to accommodate modular assembly, in which EV and ICE models will be side-by-side on the same assembly line and can be more responsive to customer demand without requiring an expensive retooling process.
Most of the EV-related projects announced in the past several years have significant electric utility requirements amounting to thousands of megawatts in added new load. Synthetic Fuels
While batteries are well suited as a solution for light passenger vehicles, they are insufficient or untenable for many other transportation sectors such as trucking and aviation. These customers require different solutions to lessen their carbon footprint, and significant funding and innovation expertise is being dedicated to delivering new alternatives. Many heavy trucking companies are exploring hydrogen as a potential solution, and hydrogen generation, transportation, and service projects are taking off across the country.
Airlines are also investing in innovation to source new fuels: in February, United Airlines announced a $100 million fund dedicated to new sustainable aviation fuel (SAF) projects to increase the quality and amount of fuels; however, at this stage, it remains to be seen whether these fuels can be scaled on a cost-effective basis to supplement or replace current fuel sources.
In Sum
While the recent spate of EV projects has generated plenty of headlines and fanfare, the long-term impacts of this industrial boom are far-reaching, creating new challenges and opportunities in sectors such as mining and energy, and catalyzing commercialization of alternative fuel products. The current dynamic environment is a result of the intersection of long-simmering industrial trends, mixed with a shift to EVs, set alight by billions of dollars of federal investment. Understanding how the EV transformation progresses in the next five years requires an understanding of all of these factors, and others, that are shaping the future of this industry. Hold on tight — it’s going to be a wild ride!
Recycling
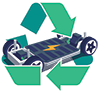
As the consumer shift to EVs continues, a key area of continued growth will be in recycling capacity for end-of-life batteries, particularly for the critical mineral components. Most current recycling producers are processing batteries from electronics, or production scrap material rather than end-of-life EV units, but as larger segments of drivers purchase EVs and more batteries exceed their service life — currently, most batteries have a useful life of 8–20 years, depending on factors such as mileage and weather and use conditions — and become available as feedstock for the circular economy, research suggests that this supply will grow by 25 percent annually through 2040.
Companies such as Redwood Materials, with facilities in Nevada and recently announced in South Carolina, Cirba Solutions in Ohio, as well as Li-Cycle in New York, Arizona, and Alabama are building out capacity to handle the growing battery volume, but much more will be needed. Like mining, recycling as an industry has historically had a poor reputation among regulators and communities, but today’s recycling technologies are highly sophisticated, sustainable, and much cleaner than previous iterations. In order to ensure that we have a resilient and cost-effective supply chain for both battery and EV manufacturing, recycling must be part of the equation.