A Skills-Based Jobs Approach to Fulfilling Workforce Needs
Businesses are collaborating with academic and other partners to advocate for modern manufacturing jobs.
Workforce Q4 2017
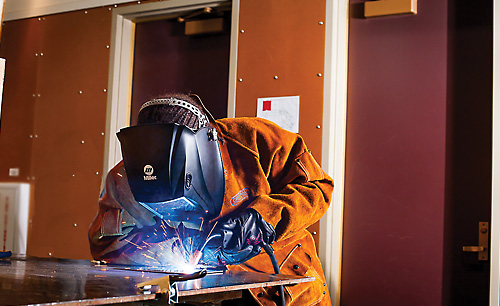
For instance, Schmidt points to the case of one of the company’s standout young employees. Silicon Forest Electronics first learned of the individual through a locally based industry ally, Partners in Careers, which helps provide resources, training, and job placement opportunities to job-seekers. The individual was a recent high school graduate with no designs on attending college.
Partners in Careers volunteered to pay the young man’s wages at Silicon Forest Electronics for 90 days with the aim of giving him industry exposure. Silicon Forest Electronics provided him with a range of work experiences, and he proved to be an unusually quick study, demonstrating — among other skills — that he could excel at military-grade soldering under a microscope. After his 90-day stint, the company offered him a full-time job and he took it. Since that time, the young worker has been trained to be one of the company’s machine technicians and is handling programming on a sophisticated piece of selective soldering equipment.
“He’s one of our selective soldering technicians a year and a half after we hired him,” Schmidt says. “If he wants to go to college, we have tuiti on reimbursement and other ways to help him out. In less than 24 months, he’s gone from not knowing anything in our industry to becoming one of our key manufacturing technicians.”
The story shows the value of manufacturers working closely with industry and education partners to develop a pipeline of young skilled workers. Schmidt explains that aggressive workforce outreach has become a necessity for manufacturers.
“We can’t sit around and wait for people to just apply for jobs anymore, because it’s just not going to happen,” he says. “I went back to Partners in Careers and said, ‘Man, that was great. Give me another one,’” Schmidt continues. “And they said, ‘We don’t have anybody else.’”
The story illustrates the scale of the task that manufacturers face and the scope of the work that is required.
Manufacturers are turning to community colleges and others to recruit and train skilled workers. Spreading the Good News About Manufacturing
With tuition at four-year colleges on a steadily sharp climb, manufacturers are seizing an opportunity to reach out to young people and others to preach the possibilities of a career in manufacturing — with or without a bachelor’s degree. These outreach efforts typically emphasize the rewards of skilled manufacturing work, often involving the use of technology. But many manufacturers are not just talking — they also are working with partners to develop training programs that can prepare workers to smoothly transition into their fields. The ultimate goal is workers prepared to succeed in positions that companies have struggled to fill.
Industry’s partners in these efforts can vary, ranging from workforce groups, such as Partners in Careers, to more education-based entities, such as community colleges and local technical schools. Training is often focused on sophisticated new technology that has changed the nature of manufacturing and created new jobs. Companies covet workers who can excel in these positions.
Mary Kaye Bredeson, executive director of the Washington State Center of Excellence for Aerospace and Advanced Manufacturing, says she believes young people are beginning to recognize the potential of contemporary manufacturing careers. “We’re starting to see that needle move a little bit,” she notes.
“I think people are starting to see manufacturing as more than a second-choice option that you turn to when you can’t do anything else,” Bredeson says. “These are great jobs and great-paying jobs.”
Nonetheless, Dan Belyea, interim director of workforce training for the Maine Quality Centers, which provide customized workforce training grants for Maine employers through the state’s community colleges, says misconceptions about manufacturing work still linger with young people.
“Working in manufacturing today is not what young people think of when they think of manufacturing,” Belyea says. “It’s clean and high tech. It’s a great area to work in — it’s not the old machine shop with oil dripping all over the place. But people don’t know that yet.”
When Industry Talks, Academia Listens
The Center of Excellence for Aerospace and Advanced Manufacturing is one of 10 centers of excellence in Washington. The centers help communicate the pressing workforce needs of the state’s major industrial sectors to the state’s 34 community/technical colleges.
“We don’t have students and we don’t provide any training programs,” Bredeson explains. “What we do is we meet with industry, learn what their emerging needs are, and we disseminate that information to our community/technical colleges.”
The arrangement represents one of the ways that public-private partnerships can work toward addressing shortages of skilled workers for specialized manufacturing work. Bredeson points to her center’s work with Boeing, which was founded in Washington and maintains a large presence there, as a demonstration of the way these collaborations can provide a boost for business.
Boeing informed Bredeson and her team that it was facing an emerging workforce need for industrial machine technicians as well as training in automation and robotics. At that time, Washington’s community colleges were not offering studies in those areas. However, the Center of Excellence for Aerospace and Advanced Manufacturing researched related programs around the country, including a training program developed in Lexington, Kentucky, where Toyota had opened a large production plant.
“We brought in subject matter experts and looked at the curriculum and relied on our industry partners to vet it,” Bredeson says. “Then we applied for a Department of Labor tech hire grant and received just under $4 million to build that capacity.”
With tuition at four-year colleges on a steadily sharp climb, manufacturers are seizing an opportunity to reach out to young people and others to preach the possibilities of a career in manufacturing — with or without a bachelor’s degree. Siblings and more distant relatives of Washington’s program can be found around the country, providing manufacturers with a simple first step to exploring ways to identify suitable partners for training programs tailored to their needs. For instance, Belyea says Maine’s community college system works with employers from a wide range of industries.
According to Belyea, community college system representatives meet with business partners to identify high-demand service areas that would be fruitful for new training efforts. The colleges will provide direct training for the businesses for a fee, including training for both new hires and incumbents who need to expand their skills, or they will partner with the firms to develop training programs to serve industry more broadly.
For example, Southern Maine Community College helped develop a training program for textile manufacturing work in Portland with a number of partners. The program, which focuses on stitching, was built based on input from 26 different Maine manufacturers in that field, with leadership from Old Port Wool & Textile, a woolen goods manufacturer, and American RootsWear, a fleece maker, explains Belyea. The close involvement of the industrial partners helped make the training a success. “No matter what industry is involved, it’s important that the businesses participate,” Belyea says.
Dory Waxman, owner of Old Port Wool & Textile, was closely involved in the development of the textile training program and remains integral to its operation. Waxman says businesses, particularly manufacturers, that do not invest resources in workforce development are taking a major risk. “For any business that wants to be successful, I think education has to be a key component in building that success,” she points out.
The Power of Involvement
Schmidt said manufacturers looking to bolster their workforce through partnerships should be ambitious and persistent in their efforts. “Don’t let perfect get in the way of better,” he says. “Don’t wait for someone to provide things to you. Get out there and get involved.”
Bredeson says manufacturers and others need steady partners to keep up with the rapidly changing workforce climate, altered by the accelerated arrival of new technological solutions.
“The jobs are always changing,” Bredeson explains. “Technology is changing at such a rapid rate that we’ve got high school students starting ninth grade now, and by the time they graduate there will be new jobs out there for them that nobody has even heard of yet.”
Schmidt says the work of proselytizing for manufacturing is difficult but necessary. A great result, such as a young worker discovering talents no one knew were there, makes it all worth it.
“I’m a big fan of Stephen Covey who talked about ‘the law of the harvest’ — you can’t just expect to go out and take the fruit off the vine,” Schmidt says. “You’ve got to put stuff in the soil. Employers need to invest at the root of things for this to really work.”
Project Announcements
Herr Foods Establishes Jackson, Ohio, Operations
05/17/2024
SRC of Lexington Expands Fayette County, Kentucky, Operations
05/17/2024
John Deere Expands Kernersville, North Carolina, Production Operations
05/17/2024
Japan-Based Asahi Kasei Plans Port Colborne, Ontario, EV Battery Operations
05/17/2024
Microsoft Establishes Mount Pleasant, Wisconsin, Data Center Operations
05/16/2024
BlueHalo Establishes Germantown, Maryland, Production Operations
05/16/2024
Most Read
-
2023's Leading Metro Locations: Hotspots of Economic Growth
Q4 2023
-
38th Annual Corporate Survey: Are Unrealized Predictions of an Economic Slump Leading Small to Mid-Size Companies to Put Off Expansion Plans?
Q1 2024
-
2023 Top States for Doing Business Meet the Needs of Site Selectors
Q3 2023
-
Making Hybrid More Human in 2024
Q1 2024
-
20th Annual Consultants Survey: Clients Prioritize Access to Skilled Labor, Responsive State & Local Government
Q1 2024
-
Manufacturing Momentum Is Building
Q1 2024
-
The Bring Your Own Energy (BYOE) Party Is Starting
Q2 2024