Mitigating Labor Challenges in Life Sciences Manufacturing
Why executives facing manpower shortages must consider a menu of location planning, automation, and fostering a learning culture to meet current challenges and drive efficiency.
Q2 2024
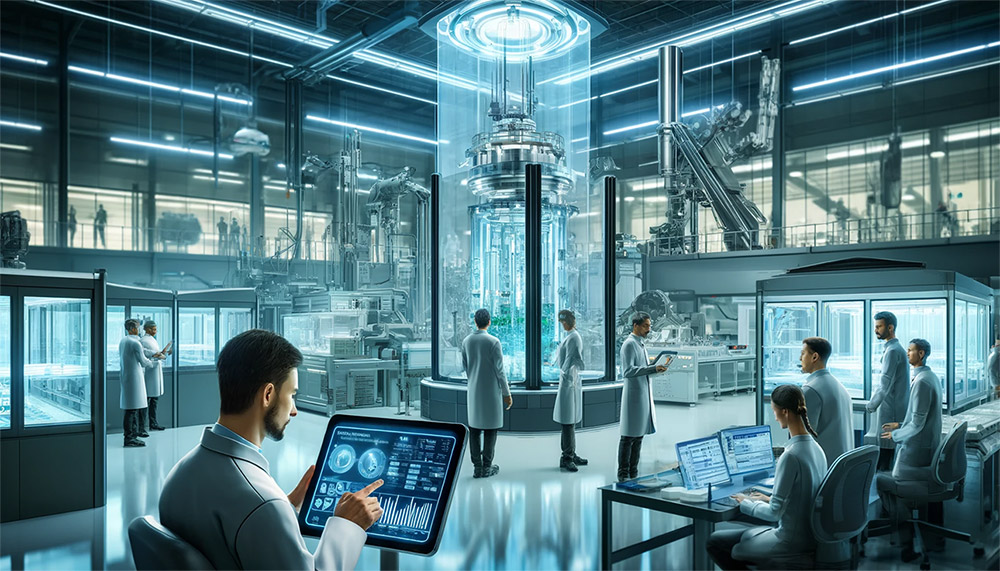
This evolution is not only a testament to our innovation but also a call to action to address the growing challenge of labor shortages—a pivotal issue that could hinder our progress if left unmanaged. As a manufacturing executive, you play a pivotal role in navigating these changes, ensuring our industry not only meets current demands but also gets these wonderful medicines and technologies to patients who need them.
The Current Landscape of Life Sciences Manufacturing
Today’s life sciences manufacturing is light years away from simplistic assembly lines. Modern facilities are high-tech environments where sophisticated biologics are developed under stringent regulatory standards. The workers in these facilities need a unique blend of skills—they must be as adept with bioreactors and chromatography as they are with regulatory compliance and quality control. The demand for such talent is increasing, yet the supply remains worryingly scant.
The root of this labor shortage is deep and tangled. You have the rapid technological advancements that require continual learning and adaptation from your workforce, skills that are not abundantly available in the traditional pool of talent. Then, you must compete with the allure of other high-tech fields, often with more glamorous perceptions or seemingly better working conditions, drawing potential talent away from manufacturing roles in life sciences. The challenges are big, but there are solutions that can bend the curve in the right direction.
Strategic Location Planning
One of the first strategies to mitigate labor shortages is thoughtful location planning for new facilities. The choice of location can significantly influence the ease of attracting skilled labor. Proximity to academic institutions can provide a steady influx of fresh talent, eager to apply cutting-edge scientific knowledge. Additionally, regions with a thriving biotech ecosystem offer a competitive advantage by providing access to a pool of workers experienced in highly regulated environments.
The life sciences sector has been pushing the boundaries of medical science, advancing from small molecule drugs to complex biologics and cell therapies. Conversely, establishing operations in less saturated markets can reduce turnover rates. In areas with fewer competing employers, employees are more likely to have longer tenures, which enhances continuity and reduces the costs associated with training new workers. However, this approach requires a balanced assessment of the potential challenges, such as the initial difficulty in attracting talent to these lesser-known areas.
Leveraging Technology and Automation
Embracing automation is another crucial strategy. While the upfront costs are significant, the long-term benefits of automation in addressing labor shortages cannot be overstated. Automated systems can take on repetitive, labor-intensive tasks, allowing human workers to focus on more complex and value-added activities. This not only makes better use of scarce talent but also improves job satisfaction by reducing monotony.
Moreover, integrating advanced technologies such as artificial intelligence and machine learning can enhance production efficiency and compliance, reducing the burden on human workers and allowing for a leaner workforce that is easier to maintain.
Fostering a Culture of Continuous Learning and Development
Perhaps the most critical strategy is cultivating a workplace culture that values continuous learning and development. In an industry as dynamic as life sciences, the ability to keep pace with technological and regulatory changes is paramount. Employers must invest in ongoing training and development programs to ensure their workforce remains at the cutting edge of scientific and manufacturing advancements.
In an industry as dynamic as life sciences, the ability to keep pace with technological and regulatory changes is paramount. Additionally, life sciences companies must become adept at ‘re-recruiting’ their own employees—continuously engaging them and reinforcing their value to the organization. This approach not only enhances employee retention but also builds a more committed and moti-vated workforce.
Building Partnerships and Collaborative Networks
Collaboration across the industry can also play a vital role in addressing labor challenges. By forming partnerships with educational institutions, life sciences companies can help shape curricula to ensure that the skills taught match the industry’s needs. Internships and co-op programs can provide students with practical experience and a pathway to full-time employment, creating a pipeline of job-ready graduates.
Similarly, companies can collaborate with each other to develop shared training resources, which can be particularly beneficial for smaller firms that may not have the resources to develop comprehensive training programs independently.
The Risks of Outsourcing
Not every mitigation strategy is a good one. Outsourcing manufacturing processes in the life sciences sector is a common way for companies to manage high costs and the complexities of building and maintaining their own facilities. However, this approach comes with significant risks. When you outsource, you relinquish control over critical aspects of production, potentially compromising the quality and consistency of the products. This loss of oversight can lead to delays and variability that may not align with the stringent regulatory standards required in pharmaceutical manufacturing.
The challenges of labor shortages in life sciences manufacturing are formidable, but they are not insurmountable. Outsourcing can also introduce vulnerabilities in your supply chain, making it harder to respond to fluctuations in demand or disruptions in supply. Most critically, dependency on external manufacturers can constrain innovation and responsiveness, delaying the introduction of breakthrough therapies that could significantly benefit patients. These factors make outsourcing a double-edged sword, offering cost savings at the potential expense of product quality and company agility.
What’s Next?
The challenges of labor shortages in life sciences manufacturing are formidable, but they are not insurmountable. Through strategic location planning, the adoption of automation, a strong emphasis on continuous learning, and collaborative industry efforts, we can build a resilient workforce that can support the future of medicine.
Our industry is known for its innovation and resilience, and by applying these qualities not only to our products but also to our manufacturing practices and workforce development, we can ensure that life sciences continue to thrive. As we look to the future, our ability to innovate in how we manage and develop our workforce will be just as important as the innovations we bring to patient care.
Project Announcements
India-Based Garonit Pharmaceutical Plans New Windsor, New York, Manufacturing Operations
08/11/2025
Alltech Expands Jessamine County, Kentucky, Manufacturing Operations
07/30/2025
Catalent Expands Madison, Wisconsin, Production Operations
07/21/2025
Meridian Biotech Plans Franklin County, Kentucky, Aquaculture Product Operations
07/18/2025
ProBio Establishes Hopewell, New Jersey, Gene Therapy Operations
07/02/2025
LifeScience Logistics Plans Memphis, Tennessee, Operations
06/26/2025
Most Read
-
20th Annual Area Development Gold and Silver Shovel Awards
Q2 2025
-
What We’re Getting Wrong About Gen Z’s Future in the Skilled Trades
Q3 2025
-
A New Course for U.S. Shipbuilding
Q3 2025
-
Optimizing Your Rail-Served Transportation Network: Strategy Before Steel
Q2 2025
-
In Focus: AI Is Changing Incentives Math
Q2 2025
-
How to Choose the Right Site for Your Factory in 2025’s Volatile Landscape
Q2 2025
-
Reshoring Reality Check from Construction
Q3 2025