Growth in International Aerospace Markets Spurs Increased Production in New Hampshire
SAFRAN Aerospace Composites and Albany International have co-located in a 343,000-square-foot facility in Rochester, New Hampshire, which will provide the lightweight composite components required by the aerospace industry.
2018 Auto/Aero Site Guide
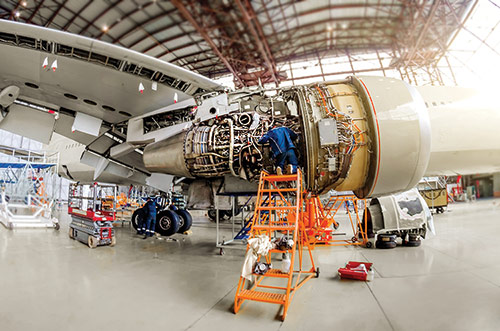
CFM has just delivered the 1,000th LEAP engine with composite material fan blades and casings, and demand continues to climb as the company logs another $15.7 billion in orders from the Farnborough Airshow outside of London. The LEAP engine features composite engine components available since 2014, with the opening of a new SAFRAN Aerospace Composites and Albany International co-locating in a 343,000-square-foot facility located in Rochester, New Hampshire. The composite components have quickly become the preferred lightweight material as demonstrated by orders at the Farnborough Airshow, where 15 of the 16 orders were for the LEAP engines. This composite engine increases safety as well as provides significant energy savings over traditional engines.
The LEAP engine is going through a massive ramp-up, “the fastest in the history of aviation,” says Brandon Wagner, executive plant leader at GE’s Hooksett Plant. “The LEAP-1B, which goes to Boeing…we’re making 20 engines a week — that’s going to be 36 engines a week by the end of next year.”
CFM International announced orders and commitments for just over 858 LEAP and CFM56 engines at the 2018 Farnborough Airshow, in addition to long-term services agreements, at a total value of $15.7 billion U.S. list price.1 Orders from the airshow were across all engine lines, servicing widebody, narrow-body, and regional jets. New Hampshire makes products for all of these engine platforms, so these orders go back directly to the Rochester and Hooksett, N.H., plants. In preparation for increased production, hiring is a priority, with more than 1,200 employed at the two plants. Rochester has 50 open positions and can provide customized training at the Advanced Technology and Academic Center (ATAC). The ATAC is a satellite campus of Great Bay Community College, with a lab replicating the exact manufacturing experience as the actual plant floor at SAFRAN Aerospace Composites. Recruits are OSHA-certified and get a complete training in composites and nondestructive testing in six months.
1 www.safran-group.com/media/cfm-logs-157-billion-orders-2018-farnborough-airshow-20180719
Project Announcements
Busch Vacuum Solutions Plans Tempe, Arizona, Operations
08/18/2025
Made Scientific Establishes Princeton, New Jersey, Manufacturing-Headquarters Operations
08/18/2025
Comcast Establishes West Palm Beach, Florida, Operations
08/17/2025
Buttonwood Farm Expands Fortuna, Missouri, Egg Production Operations
08/15/2025
MerryGoRound Plans Pittsylvania County, Virginia, Fulfillment Operations
08/14/2025
Hartman Cabinetry Plans Jonesburg, Missouri, Operations
08/14/2025
Most Read
-
What We’re Getting Wrong About Gen Z’s Future in the Skilled Trades
Q3 2025
-
A New Course for U.S. Shipbuilding
Q3 2025
-
Optimizing Your Rail-Served Transportation Network: Strategy Before Steel
Q2 2025
-
In Focus: AI Is Changing Incentives Math
Q2 2025
-
How to Choose the Right Site for Your Factory in 2025’s Volatile Landscape
Q2 2025
-
Reshoring Reality Check from Construction
Q3 2025
-
The New Math Behind Mexico and U.S. Manufacturing Decisions
Q2 2025