I spent 30 years at Lockheed Martin, 20 of which were in site selection, workforce development, and real estate disciplines, followed by the last 11 years consulting in the tech sector. Site selection has come a long way in the last four decades, driven by increased investment requirements, heightened investor scrutiny, and deteriorating workforce demographics.
Forty years ago, touch labor training requirements were relatively rudimentary, most of the population was mechanically adept, and workers were willing to move for a job in the tech sector. In those days, you could locate a new facility at the whims of management with little investor scrutiny.
Today, workforce development and pipelining criteria play the primary role in developing a site selection profile that ensures the ability to hire, train, and perpetuate an affordable workforce.
Until we develop a K-12 system that teaches higher-level math and science in the elementary grades and begin profiling a student’s curriculum to their likely profession early, we will continue to graduate generations of entry-level workers with very few job skills.
Forty years ago, it took 35 man-hours to assemble a television set. Today, that can be done in less than three. Advanced manufacturing facilities using seven to 10 varieties of additive manufacturing systems, composite robotic lay-up and weaving, robotic subtractive manufacturing processes, and robotic blacksmithing (sheet metal forming) are highly complex technologies requiring a few highly skilled workers instead of armies of low-skilled laborers from Henry Ford’s era.
Worse, many of the entry-level K-12 jobs can be blended into skilled operators’ downtime (waiting on machines) or eliminated with a variety of automated, tailorable manufacturing systems.
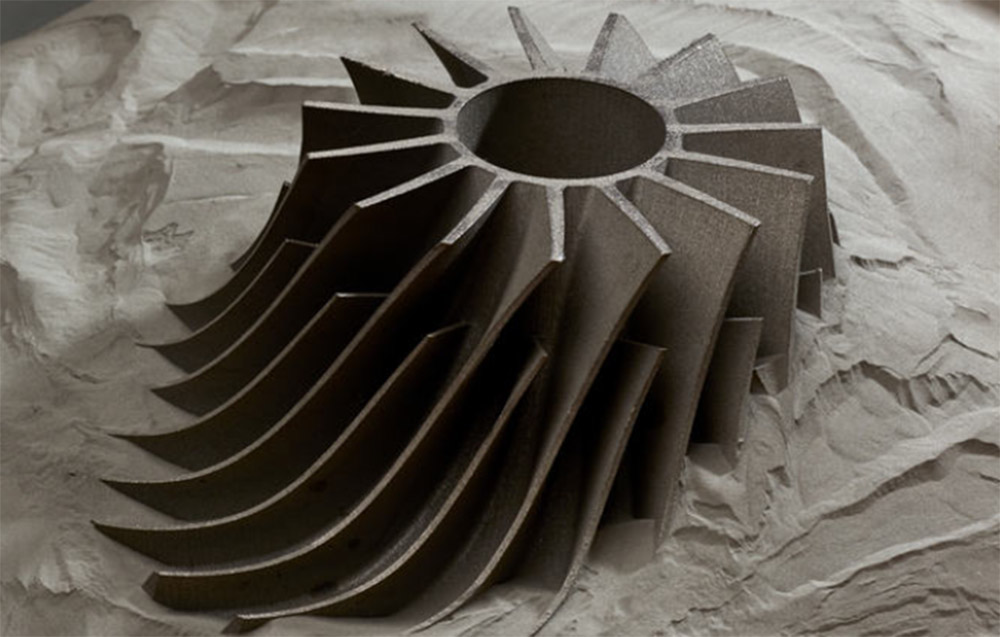
The exponential increase in technology innovation that began in the mid-20th century also plays a factor, creating new professions for which there is no heritage workforce. For example, “aerospace coaters” are people who can apply special ablative and stealth coatings to aerospace hardware. A recent Vista analysis of this market showed that there were 5,000 people in this field in the entire United States, all of them employed by Pratt & Whitney in Connecticut or Lockheed Martin in Texas.
Today, workforce development and pipelining criteria play the primary role in developing a site selection profile that ensures the ability to hire, train, and perpetuate an affordable workforce.
If you need 200 of these people to support your new facility, you quickly conclude that you will have to train them up from an ancillary profession, like robotic automotive painting. You then look for clusters of robotic automotive painters and develop a workforce development program to train them to meet the higher specifications of aerospace coatings work.
Modern, effective site selection starts with an analysis of the proposed new facility’s labor requirements at the Standard Occupational Classification (SOC) code level. This can be aided by looking at both the company’s existing facilities or its primary competitors using cell phone tracking and various financial databases.
With the labor requirements in hand, artificial intelligence and conventional software algorithms are used to scan the country or globe to locate workforce enclaves that match the company’s requirements at a significant cost savings. As shown in the example above, certain disciplines aren’t reasonably available anywhere, so the model has to be adjusted to look for ancillary skills.
The training program for the new facility can no longer be delayed until the new facility is nearing completion. It should be instituted the day after the site selection decision is announced.
35%
Four Phases of Touch Labor Training
For touch labor workers, training can be grouped into four phases:
Phase One – Dedication and Mechanical Aptitude
Phase One is a short-duration pre-employment program to assess the applicant’s dedication (will they show up for work?) and mechanical aptitude (do they know a torque wrench from a set of slip-joint pliers?). Most of the people you will be hiring will already be employed, so the Phase One sessions are held in the evening for three to four hours per night. If the applicant shows up for all the sessions on time, they pass the dedication criteria. Interestingly, a state training director recently told me they lose a third of applicants in this phase. During their classes, applicants are asked to perform simple tasks on rudimentary machinery and identify tools and their use. The company generally defines the tasks they want to see demonstrated. The cost of recruiting applicants for the Phase One program and its execution should be covered by regional government as part of a comprehensive incentives package.
Phase Two – General Job Skills Development
Phase Two training can run from a few weeks to a two-year associate degree or certification. This level of training can generally be carried out by the community college and trade school systems and is aimed at building the general skills necessary for productive employment. In the aerospace coaters example above, this training would consist of a generic robotic automotive painting program. The costs for these programs should be covered by regional government as part of a comprehensive incentives package, and most states have special funds available for this type of program. If possible, this training should also be pre-employment, with the promise of an interview upon successful completion of the curriculum. Many candidates voluntarily enter Phase Two training outside of the Phase One system by simply selecting the major as part of their post-K-12 study.
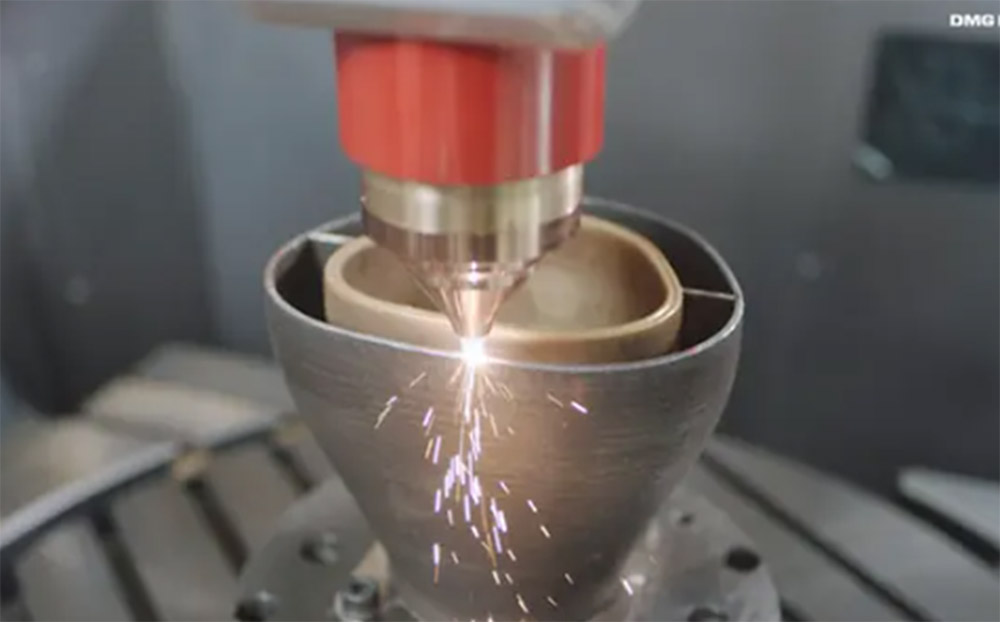
Phase Three – Job-Specific Skills
Having completed generic training for the job skills needed, we now need to train the workforce in specific job skills. In our aerospace coater example, this entails training the successful robotic automotive painter to spray advanced aerospace coatings to much higher specifications than the automotive industry. These processes are either company proprietary or classified for much of the aerospace industry and therefore can’t be taught through the community college and trade school systems. They require a company training center and production equipment and are done post-employment using shop queen, sample, and scrap hardware. Finding public-sector incentives funds to establish the training center and teach the skills is a large hole in the U.S. business incentives infrastructure. If you want this level of training paid for, you need to be cautious about which states you select as prospective sites for the new facility.
Forty years ago, it took 35 man-hours to assemble a television set. Today, that can be done in less than three.
Phase Four – On-the-Job Training
With formal training complete, the new employee is now first exposed to production hardware under the supervision of an experienced operator. The cost of this training is somewhat latent and often materially underestimated by the company. For example, if we assume a new employee enters the system 35 percent efficient and improves along an 86 percent learning curve to reach 100 percent competency over the first six months of employment, the company will incur 580 hours of unproductive time during the on-the-job training process. If we assume a burdened manufacturing rate of $100 per hour, the cost of on-the-job training is $58,000. Once again, public-sector incentives to cover this cost in the form of a wage subsidy are a challenge, and you have to be particular about which states you consider in site selection to maximize this level of workforce development support.
When we implement these strategies with client companies, we generally get pushback from two sources: economic development officials and corporate training professionals. I’ve heard from more than a few economic development professionals, “Why isn’t the company paying for all this? Fifty years ago, companies paid for this.” The answer is clear from the earlier discussion: The manufacturing that’s financially feasible to do in the United States is much more complicated than it used to be, and the candidates the country is delivering are devoid of most of the skill sets necessary. Further, the world has become a very competitive place and other countries do a much better job providing pre-employment skills.
Workforce Development vs. Pipelining
So far, everything I’ve covered would be categorized as workforce development, which gets an initial workforce in place to operate the new facility. Workforce pipelining is a twin discipline, extending workforce development efforts to ensure a perpetual pipeline of new employees to cover growth, attrition, and retirements. There’s no room to discuss those constructs here, so I’ll save them for a follow-up article.
The manufacturing that’s feasible in the United States is more complex than it used to be, and candidates are often devoid of the necessary skill sets.
So, what should your son or daughter study to ensure a financially rewarding career in aerospace and tech? First, don’t opt out of those higher math and science classes in the K-12 system because it is easier. Then augment that education with shop classes in wood, metal, automotive, and robotics from 7th to 12th grades. Don’t spend your retirement on expensive private universities, there are lots of good public university engineering programs that will get you a job without half a million dollars in debt.
Then let the company pay for an expensive master’s degree at a prestigious university. It’s no crime not to be able to make the engineering hurdle, but that’s not a reason to switch to a major that doesn’t offer any reasonable job opportunities.
Go to trade school instead and learn a skillset industry is desperate for. Here are a few: Airframe and Powerplant Mechanic, Robotic Welder (including exotic metals), NC Machinist, Robotic Painter, Additive Manufacturing Technician, Engineering Technician, etc. Thanks for your time, and as they say in the military, “Good Luck and Good Hunting” in all your business endeavors.