To understand what is driving the recent growth in intermodal activity, it may help to remember that supply chains have fueled economic activity and the affluence of civilizations throughout history. The term “intermodal” may be a product of the 20th century, but the concept of linking multiple transportation modes has been around since Silk Road traders packed Far East goods over land to waiting merchant ships on the Mediterranean. Rail entered the picture in the 19th century, introducing comparatively rapid freight to existing networks of waterborne shipping and horse-drawn wagons.
The last century added trucking to the equation as an expedient method of transporting merchandise in volume to locations inaccessible by rail or water, traversing the distance between ports or railheads to manufacturers, and from warehouses to retail stores. As the growth of American cities outpaced rail expansions, new roads and highways enabled trucking to dominate the freight industry. Then and now, supply chains adjust continually to make efficient use of available resources and transportation methods in moving materials and finished goods.
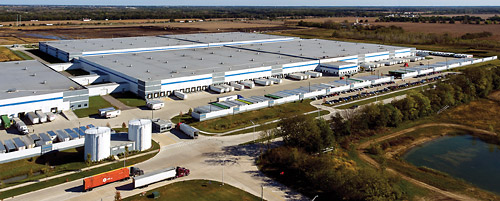
Today, however, intermodal activity refers chiefly to the movement of containers via some combination of ship, rail, or truck. Intermodal yards operated by the major rail providers are designed to transfer containers between railcars and trucks for inland ports, or direct from cargo ships to trains or trucks for seaports. Rail intermodal traffic has mushroomed, from 3.1 million shipping containers and truck trailers transported by train in 1980, to more than 13 million moved in each of the past three years, according to the American Association of Railroads.
This is the model that moves the majority of consumer goods filling American households. The Intermodal Association of North America (IANA) estimates that railcars move 17 million intermodal loads in the United States each year, generating more than $20 billion in revenue for the 10 largest rail carriers. In fact, more than a quarter of U.S. railroad revenue now comes from intermodal freight, the IANA found.
The number of intermodal yards is also growing. Already, 60 North American ports handle shipping containers, as do more than 1,000 inland facilities, and more intermodal yards are in planning and development across the country. What is fueling this resurgence of multimodal freight in the United States, making intermodal capability a priority for so many industrial users?
Drivers of Intermodal Growth
There are many reasons for this rail renaissance and the subsequent upsurge in intermodal activity. Contributing factors range from deregulation of rail service providers and shipping companies beginning in the 1970s, to the rising volume of consumer goods imported from China and other low-cost labor markets. More recently, however, a few factors stand out as the leading impetus for intermodal growth.
Retailers including Amazon are still determining the best formula to meet today’s customer expectations, but most scenarios involve an increased reliance on distribution and fulfillment centers in or near major population centers to process orders close to customers. Transportation costs: More than 60 percent of supply chain costs involve transportation, so it is only natural that companies gravitate to service providers and methods offering the lowest transportation expense. Trains are roughly four times more fuel-efficient than trucks, providing an advantage on the price of fuel, but rail alone seldom offers sufficient access to carry goods from a point of origin to destination. In order to take advantage of rail, supply chain managers must move material to and from the rail segment of a journey. That requires a distribution facility on one or both ends of the rail leg, contributing to the demand for intermodal yards and associated industrial development.
Finite trucking capacity: Federal regulations limit a driver’s hours behind the wheel and require rest periods to reduce the incidence of fatigue-related accidents. An aging workforce and high driver turnover have further compounded the ongoing shortage of trained labor in the sector. And as same-day delivery becomes more common, job opportunities are increasing for short-haul drivers within metropolitan areas; this has increased the difficulty of staffing long-haul companies, luring away potential drivers with the prospect of sleeping in their own beds at the end of each workday.
These limitations on trucking have increased the perceived value of rail, where carrying capacity has been increasing. Practices such as the conversion from boxcars to shipping containers, which can be double-stacked on rail lines up to two miles long, have increased train capacity dramatically over the past 20 years.
The rise of e-commerce: Modern shopping habits and evolving consumer expectations are bringing profound change to distribution practices. Online purchases accounted for 11.7 percent of all retail sales in 2016, according to the U.S. Commerce Department, and many economists expect that volume to double or triple over the next decade. Customers now expect delivery in one or two days, rather than in the five to seven days that were typical a few years ago. As these trends continue to accelerate, it is becoming critical for supply chain managers to establish a reliable and diversified multimodal distribution chain.
By providing access to multiple highways and proximity to an intermodal yard, seaport, or airport with cargo service, supply chain managers can mitigate the impact of unforeseen disruptions in any one transportation component. Retailers including Amazon are still determining the best formula to meet today’s customer expectations, but most scenarios involve an increased reliance on distribution and fulfillment centers in or near major population centers to process orders close to customers. Finished goods generally reach these facilities via a multimodal channel, which often begins at one of the country’s major seaports. In choosing a location for a distribution or fulfillment center, a supply chain manager must balance the savings potential of sites near an intermodal yard, typically on the outskirts of population centers, against last-mile delivery costs that increase with the distance to those customers.
As more transactions move online, many traditional brick-and-mortar retailers have reduced the size of on-premise inventories, using showrooms in physical stores as a place where customers can make purchases or examine merchandise before buying it online in their preferred size and color. But with smaller on-site inventories, retailers must place a greater emphasis on establishing a diversified and reliable supply chain that includes multimodal capabilities.
Mitigating Risk
Just as a prudent investor seeks to reduce exposure in any one asset type within a portfolio, supply chain managers can mitigate risk by diversifying their distribution methods. Rising transportation costs, driver shortages, and port labor disputes are all potential sources of disruption within a supply chain. By providing access to multiple highways and proximity to an intermodal yard, seaport, or airport with cargo service, supply chain managers can mitigate the impact of unforeseen disruptions in any one transportation component.
In our experience, industrial tenants have shown a preference for proximity to rail and intermodal yards, whether or not they plan to access those services in the near term. As supply chains continue to evolve, and regardless of the dominant mode of transit, intermodal facilities and associated industrial developments will remain critical components in serving the nation’s growing population centers.