Streamlining Best Practices Across Facility Management
Every business can realize significant cost savings by implementing streamlined, automated processes in its daily operations.
Spring 2011
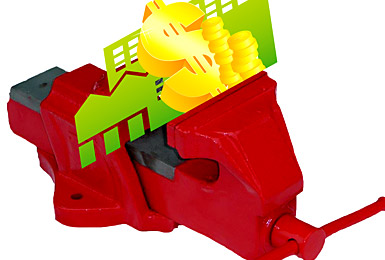
Second-Highest Costs
Real estate typically represents the second-highest costs after human resources (HR) for a company, so streamlining even a small percentage of those expenditures can significantly improve the bottom line. Streamlining a practice lets management organize in order to be more strategic, and allows automation to enhance efficiencies by eliminating tedious, mundane activities.
In other words, once a company's real estate organization establishes streamlined and appropriately automated business processes, it will:
• Speed service delivery,
• Get more accurate performance metrics in real time,
• Be able to more quickly respond to customers, and
• Execute more efficiently overall.
The most appealing part of streamlining and automating is that start-up and follow-through are common-sense. For example, an organization should first examine which services it offers within the entire RE/FM spectrum, from early strategic planning to project management, and operations maintenance to building management. Then, after evaluating the performance of each service component, management should address each discrete process to define a best-practice approach. One caveat: the RE/FM industry does not currently have a governing body defining or setting best practices as fields such as accounting have. Although organizations such as Open Standard for Corporate Real Estate (OSCRE) are beginning to address this deficiency, the phrase "best practice" is essentially up to individual organizations or informed industry consultants to decide.
Working More Consistently, Anywhere
The industry is ripe for this kind of optimization, with many opportunities available to perform tasks consistently among most RE/FM organizations. When examining each service area, determine:
• The requirement of that specific process,
• Who the ultimate customer is,
• The motivation for the customer's plans to use the space,
• How to make the space support the customer's business model, and
• How to make the process support the requirement.
Project Announcements
Little Leaf Farms Plans Coffee County, Tennessee, Production Operations
07/02/2025
White Rock Truss & Components Expands Lee County, Virginia, Operations
07/02/2025
Fox Tank Company Plans Coshocton, Ohio, Operations
07/02/2025
Ascentek Expands Shreveport, Louisiana, Operations
07/02/2025
ProBio Establishes Hopewell, New Jersey, Gene Therapy Operations
07/02/2025
22nd Century Technologies Expands Fairfax County, Virginia, Headquarters Operations
07/02/2025
Most Read
-
20th Annual Area Development Gold and Silver Shovel Awards
Q2 2025
-
First Person: Joe Capes, CEO, LiquidStack
Q2 2025
-
The Legal Limits of DEI in Incentives Agreements, Hiring, and Contracting
Q2 2025
-
From Silicon to Server: Mapping the Data Center Supply Chain
Q2 2025
-
39th Annual Corporate & 21st Annual Consultants Surveys: What Business Leaders and Consultants Are Saying About Site Selection
Q1 2025
-
Rethinking Life Sciences Site Selection in a Resilient and Dynamic Market
Q2 2025
-
Top States for Doing Business in 2024: A Continued Legacy of Excellence
Q3 2024