The goal of NNMI is to maintain U.S. leadership in advanced manufacturing by bringing industry and academia together to solve industry-relevant challenges. Each institute is a public-private partnership, owned and operated by an industry-led consortium. Today there are seven operating institutes with a goal of a mature network of 45 institutes. Each institute has a specific industry focus (for example, photonics) with the goal of advancing innovation in that sector and workforce development. Area Development checked in with Molnar to see how the program is doing so far.
AD: It seems like NNMI is rolling along — seven institutes were established between 2012 and 2015. With the many partners involved, it must require a tremendous amount of collaboration and focus to make these institutes work. How do you manage that?
Molnar: NNMI is designed to be a collaborative effort that involves extensive input from industry and academia. In 2012, five public workshops were held and more than 1,200 voices heard. Each institute is a private-public partnership, meaning the institute is managed by an industry-led consortium. The public investment is intended to establish the institute, and is a cooperative agreement awarded through an open competition. The competitions require proposing teams to co-invest in the institute, with at least a 100 percent match to federal funds. To date, every institute solicitation has been highly competitive with co-investment levels significantly above expectations.
Stakeholders realize how critical it is to the U.S. economy to have a robust, competitive manufacturing industry.
There are currently two active competitions: a Department of Defense-sponsored competition for an institute on revolutionary fibers and textiles, and a Department of Energy-sponsored competition for an institute on smart manufacturing. This year up to six additional institute competitions are planned. The NIST-sponsored competitions are open to any topic proposed by the private sector.
AD: The NNMI was established by the Obama Administration. What will happen if a Republican is voted into the White House?
Molnar: The NNMI program was authorized by Congress under the Revitalize American Manufacturing and Innovation Act of 2014. RAMI was strongly bi-partisan, with 118 co-sponsors evenly split from both sides of the aisle.
AD: You’ve had a 30-year, private-sector career in advanced manufacturing, yet left for a new career in the public sector. What do you like best about your job? What is most challenging?
There are currently two active competitions: a Department of Defense-sponsored competition for an institute on revolutionary fibers and textiles, and a Department of Energy-sponsored competition for an institute on smart manufacturing.
Molnar: Much of my industry career involved technology development using collaboration — with other companies, academia, and national labs/federal agencies. This experience has been invaluable in forming an inter-agency team to build stronger partnerships with industry and academia. I really enjoy the collaboration and teamwork with our agency partners, and with all of our stakeholders in U.S. manufacturing.
The biggest challenge is often the best opportunity — understanding the various viewpoints, constraints, and objectives of each participant. A surprise for many of us is that so many of the best practices in industry are present in the public sector, but often described with different terminology. Rephrased then, the opportunity with collaboration is to find the common terms and approaches that every stakeholder can understand and support.
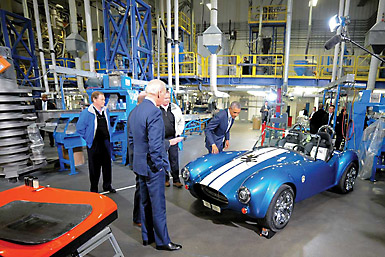
Molnar: I would offer several recommendations. First, show your community why you are important by being involved in Manufacturing Day, a national celebration held on the first Friday in October. The 2015 celebration (our fourth) included more than 2,600 events across the country. The website provides toolkits for hosting an open house or other event to celebrate U.S. manufacturing. Consider sharing your story in 2016 and the exciting things your business is doing.
A key recommendation from the President’s Council of Advisors on Science and Technology (PCAST) is upgrading the image of manufacturing. Surveys continue to show that one of the biggest issues limiting growth in U.S. manufacturing is the shortage of skilled workers. There is a misperception that a career in manufacturing today is unwise, based on the “4 Ds” — that U.S. manufacturing is dirty, dark, dangerous, and declining. As a result, many people never consider manufacturing. Manufacturing today, however, is an exciting, high-tech sector that offers significantly higher wages and benefits.
Manufacturers should also understand their local, regional, and federal resources — especially their local Manufacturing Extension Partnership (MEP) centers. MEP is a public-private partnership that helps small- and medium-sized manufacturers become more efficient and profitable. The MEP network has centers in every state, which offer information about local, regional, and federal programs, as well as providing access to experienced subject matter experts — yet many manufacturers do not take advantage of this resource. The NIST MEP program is also valuable to large companies because many of their tier-one and tier-two suppliers are small manufacturers.
Manufacturers should also understand their local, regional, and federal resources — especially their local Manufacturing Extension Partnership (MEP) centers. MEP is a public-private partnership that helps small- and medium-sized manufacturers become more efficient and profitable.
AD: Should all manufacturers become involved with NNMI and its institutes?
Molnar: The choice to join NNMI depends on how a company values collaborative research. The charter for each institute is unique and bold, involving a challenge that is transformational and beyond the means for an individual company, university, or laboratory to achieve. The composites institute, for example, aims to reduce the cost of composites by 50 percent, reduce energy use by 75 percent, and increase recyclability to over 95 percent. Those who are involved and develop a technology at an institute own the technology. Become aware of what each NNMI institute offers and then decide if this is beneficial to your technology and future product plans.
AD: NNMI is less than five years old, but what impresses you the most so far?
Molnar: The dedication by all stakeholders to make this work — they all realize what is at stake, and how critical it is to the U.S. economy to have a robust, competitive manufacturing industry. The response from the private sector to pilot institutes has been extraordinary in validating the concept, and the need for the institutes.
Establishing something new is always difficult, and there were concerns expressed that the requirement for at least 100 percent-matching funds was impossible. Every one of the solicitations had multiple proposals with not only matching funds, but at considerable multipliers — two or three times. The recent competition for integrated photonics, with a federal investment of $110 million, garnered over $500 million of co-investment. It was noted that without the public investment — and the creation of a neutral convening ground — this partnership would not have been possible. This is just one of many achievements.
The status of the program and its progress toward achieving its goals will be made public very shortly in the first annual report on NNMI. All reports and information on NNMI are available at www.manufacturing.gov. With the FY16 budget approved by Congress, the NNMI program should comprise 15 institutes by 2017.