Advanced Technology and the Changing Face of U.S. Manufacturing
U.S. manufacturers are investing in advanced equipment, automation, and robotics in order to drive down the cost of production and compete in the global economy. The net result has the potential to transform our industrial base.
Q4 2014
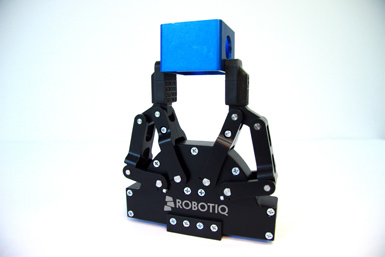
One of the strongest technology trends in manufacturing today is the installation of robotic equipment. Technological advances have made robots more “aware” of their surroundings, using 360-degree sensors that allow them to operate safely, and with more dexterity, near human workers on the production line. Another design improvement is intuitive, easy-to-use software interfaces that improve production and efficiency. Robotic equipment has also dropped dramatically in cost and can be easily scaled to any size of operation, making it more accessible and affordable to smaller companies.
Manufacturing is undergoing a change that is every bit as significant as the introduction of interchangeable parts or the production line, maybe even more so Michael Idelchik, Vice President of Advanced Technology Programs, GE Global Research
According to the Robotics Industries Association, global robotics companies established record sales in the first half of 2013. A total of 10,854 robots valued at $679.3 million were ordered from North American robotics companies during that six-month period — an increase of about 2 percent over the same period the previous year. This increase is, in part, driven by a wider use of robots across multiple industries, including semiconductors, life sciences, food processing, injection molding, metalworking, medical equipment logistics/distribution, and even small, complex devices like cellphones. For example, Google and Taiwanese manufacturer Foxconn plan to use 10,000 assembly-line robots to manufacture the iPhone 6.
The automotive industry continues to use industrial robots in creative ways. Robots have been developed for automotive assembly lines whose highly sophisticated vision systems allow them to “see” their surroundings and take on more intricate tasks, such as painting. An especially innovative robotic application is an exoskeleton “hand” that assembly line workers can wear, which reduces repetitive stress injuries and improves performance.
“Although the automotive industry uses a large number of industrial robots in a production line, human workers still contribute to the final completion of the cars,” says Mathieu Bélanger-Barrette, an engineer with Robotiq, a Canadian robotics manufacturer based in St-Nicolas, Quebec. “Operations such as wiring installation and wheel installation remain human tasks. To reduce the weight applied on the human hand, Equipois has developed a bionic hand. This exoskeleton device reduces the stress produced by repetitive movement. It also adds 10 pounds of gripping force to the worker. The ‘gripper’ comes with sensors, actuators, and simulated nerves, muscles, and tendons that not only reduce fatigue, but also increase manual dexterity.”
Auto manufacturer Tesla is also using cutting-edge robotics to manufacture its Model S. Tesla employees work alongside flexible robots to install the battery, motor, interior components, and miles of cabling. In fact, the company recently announced plans to install additional flexible robots made by KUKA, a leading robotics firm in Germany, to expand production and keep up with consumer demand for the Model S and Model X crossover SUV.
When manufacturers utilize automation, robotics, and vision systems in their production lines, it has been estimated that throughput can be increased by nearly 25 percent, with improved quality and less down time.
“For our customers, automation is the decisive key to higher productivity and greater cost-effectiveness,” says Wolfgang Meisen, director of corporate communications at KUKA Robotics. “It improves product quality, reduces cost-intensive use of materials, and minimizes the consumption of dwindling energy resources.”
Automated Technologies
New manufacturing equipment, such as computer numeric control (CNC) machining centers, rely increasingly on automation. These sophisticated machines enable the micro-machining of complex, mission-critical parts with dimensional tolerances as tight as +/- 0.0001 inches. Complex profiles and shapes that once required multiple machining operations can now be completed on a single machine, reducing operational costs and shortening lead times.
One of the biggest advantages of the new machines is being able to change parts quickly, with fewer set-ups. Because of these advancements in tooling and automation, secondary operations that were commonly performed on lathes and other machining centers are now done on a single machine, saving considerable time and money. Perhaps the most exciting part of automation and advanced machining equipment is that designers and engineers now have more options for creating innovative parts and products, often from materials that were once considered too challenging to machine.
“The machine operator is now an integral part of the layout, machine programming, and statistical control process,” says Dave Simak, marketing manager for Banner Service Corporation, an Illinois-based provider of medical-grade metal materials. “Automation allows for lights-out operation and extends capacity for companies looking to continue production after the standard work day has ended.”
An essential part of any advanced manufacturing operation is the use of sophisticated, automated vision inspection systems to inspect and pass/fail final products. System requirements vary according to the product’s specifications and requirements. For example, systems can be designed to take an image of each final product that is then compared to the actual dimensions in the imported CAD file with high precision. Optical visual-coordinate-measuring machines can inspect complex contours in a matter of seconds. When manufacturers utilize automation, robotics, and vision systems in their production lines, it has been estimated that throughput can be increased by nearly 25 percent, with improved quality and less down time.
Perhaps the most exciting part of automation and advanced machining equipment is that designers and engineers now have more options for creating innovative parts and products, often from materials that were once considered too challenging to machine. Manufacturing Intelligence Ties It All Together
“Manufacturing intelligence” is a process by which manufacturing-related data is captured in real time, using sophisticated sensors and software, which is then analyzed to manage overall operations and maximize efficiency. These metrics are monitored on a regular (or continuous) basis and bring together a number of different cost centers to streamline the manufacturing process, improve quality, reduce downtime, and save energy.
“Manufacturing intelligence strategies leverage a suite of reporting and analysis tools, interfaces, and dashboards designed to deliver contextual, localized, role-based information to help improve the system or process,” Rockwell Automation states on its website. “Reliable data collection and accurate, streamlined reporting is needed to put data into context and improve production performance. Displaying metrics in graphical representations and easy-to-read reports provides powerful insight into performance history that can be used throughout operations to support continuous improvement.”
Automation and robotics are critical tools for achieving continuous improvement and overall equipment effectiveness in the manufacturing setting. A good example of the impact of automation and manufacturing intelligence is GE’s $170 million battery plant in Schenectady, New York, which manufactures industrial batteries for power plants, cellphone towers, wind turbines, and other large installations. GE’s operations management team has designed an intricate manufacturing intelligence system that analyzes a vast array of data that plant engineers can monitor 24/7. This can identify areas where improvements can be made, often through the implementation of automation or other advanced technologies.
As reported in The Wall Street Journal, “GE can trace a product’s entire genealogy, from containers of dirt, sand, and salt to a bank of high-tech batteries supporting a nation’s electric grid. The data not only improve quality control — if a defect shows up at any point, GE can trace it back to its original source — but in the end give GE a powerful competitive weapon that’s virtually impossible to duplicate.”
The various operations within the Schenectady plant are so automated, networked, and monitored that, despite its vast size (a footprint of about four football fields), the company won’t need more than 450 people to run at full production in 2020.
“Manufacturing is undergoing a change that is every bit as significant as the introduction of interchangeable parts or the production line, maybe even more so,” says Michael Idelchik, vice president of advanced technology programs for GE Global Research, only a few minutes from the battery plant. “The future is not going to be about stretched-out global supply chains connected to a web of distant giant factories. It’s about small, nimble manufacturing operations using highly sophisticated new tools and new materials.”
Project Announcements
AMfg Labs Expands Belmont County, Ohio, Production Operations
11/25/2024
Shapeways Holdings Expands Livonia, Michigan, Operations Complex
07/07/2023
Germany-Based Becker Robotic Equipment Plans Canton, Georgia, Manufacturing Complex
12/07/2022
LEGO Group Plans Chesterfield County, Virginia, Manufacturing Plant
06/17/2022
Scotland-Based PowerPhotonic Plans Sahuarita, Arizona, U.S. Headquarters-Production Campus
04/04/2022
A. Duie Pyle Plans Manassas-Richmond-Roanoke, Virginia, Cross Dock Service Centers
03/15/2022
Most Read
-
First Person: Joe Capes, CEO, LiquidStack
Q2 2025
-
The Legal Limits of DEI in Incentives Agreements, Hiring, and Contracting
Q2 2025
-
39th Annual Corporate & 21st Annual Consultants Surveys: What Business Leaders and Consultants Are Saying About Site Selection
Q1 2025
-
Top States for Doing Business in 2024: A Continued Legacy of Excellence
Q3 2024
-
Get Your Mega Site ‘Project Ready’
Q2 2025
-
Why Cold Storage May Defy the Tariff Crunch
Q2 2025
-
Navigating the new era of SCIF construction
Q1 2025