Logistics Industry Continues to Evolve
Expansion of the Panama Canal, increasing use of intermodal facilities, and siting of new mega distribution facilities are among the latest logistics trends.
Directory 2016
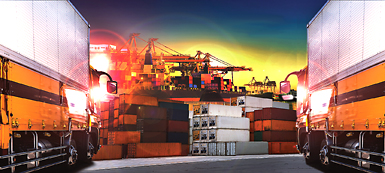
Logistics modeling, alternative delivery systems, and new methods of order picking are driving changes in the size, ceiling heights, and types of employees needed for the modern warehouse. These new trends will continue to influence the transportation and logistics of how consumers receive goods. The widening of the Panama Canal, investment into rail intermodals, and the development of industrial distribution centers for solely e-commerce purposes are additional developments the industrial real estate landscape is experiencing.
In April 2016, the much anticipated expansion of the Panama Canal is scheduled for completion. This is a serious game-changer, particularly for the ports located on the East Coast. According to the America Association of Port Authorities, $46 billion will be spent through 2016 in deepening harbors and constructing larger terminals in order to accommodate the new, more massive freight ships that will now be able to move through the canal. These ships will be able to accommodate up to 14,000 containers and have historically called upon the ports of the West Coast. With the recent labor strife the West Coast has experienced, this access and utilization of the East Coast ports will definitely be a hedge should other disputes or disagreements arise in the future. Those ports that are unable to deepen their harbors or do not upgrade their facilities will have an increasingly difficult time competing for container traffic.
Intermodal Trends
As port traffic increases due to the expansion of the Panama Canal, there are new and expanding rail intermodal facilities being constructed throughout the United States. The Association of American Railroads defines rail intermodal as the long-haul movement of shipping containers and truck trailers by rail, combined with a truck movement at one or both ends.
Intermodal allows railroads, ocean carriers, trucking companies, and intermodal customers to take advantage of the best attributes of various transportation modes to yield an efficient and cost-effective overall freight movement. A report completed by the Association of American Railroads in May of 2015 states that in 2014 rail intermodal volume was 13.5 million containers, and trailers and intermodal accounted for 22 percent of revenue for major U.S. railroads, more than any other single commodity.
According to a recent report by Colliers International titled “From First Mile to Last Mile – Global Industrial & Logistics Trends,” intermodal freight has been the fastest-growing transportation mode for the U.S. for the past decade, with U.S. rail volumes growing over 400 percent since 1980. With railroads investing in new intermodal terminals, track upgrades, and other infrastructure, the intermodal service has become more reliable and cost-effective.
The growth in intermodal is attributed to several key changes taking place. Those include truck-driver shortages, new tighter restrictions and regulations being placed on the trucking industry, increased congestion, and the condition of the interstate highway system. The shortage of qualified truck drivers is an issue for trucking companies and it appears that this problem will persist in the foreseeable future. In addition to finding qualified drivers, recent restrictions mandate shortening the hours a truck driver may spend behind the wheel, which will definitely reshape the supply chain.
The critical infrastructure (highways, bridges, etc.) needed to deliver goods by trucks has been deteriorating and is in vast need of repair throughout the U.S. These conditions lead to increased costs, which include repair to damaged vehicles from the poor road conditions and additional miles traveled or time spent to avoid unusable roadways or congested areas. The critical infrastructure (highways, bridges, etc.) needed to deliver goods by trucks has been deteriorating and is in vast need of repair throughout the U.S. These conditions lead to increased costs, which include repair to damaged vehicles from the poor road conditions and additional miles traveled or time spent to avoid unusable roadways or congested areas. The increased congested areas, in turn, creature an issue in making sure freight is delivered on time.
A few key examples of successful intermodal hubs include BNSF Alliance Global Logistics Hub – Dallas/Fort Worth, BNSF Logistics Park – Chicago, and South Carolina Inland Port – Greer, S.C.
Distribution Center Requirements
Retailers are determining what best suits their needs. Should they operate a multi-channel distribution center (combination of store orders and individual orders) or a dedicated e-commerce facility? Therefore, the design of the modern distribution center or e-commerce facility is another evolving change taking place. This evolving change relates to the process and delivery of goods in which e-commerce is playing a major role. E-commerce-centric distribution centers have come to be known as mega distribution centers.
Mega distribution centers are loosely defined as greater than one million square feet. In the United States, Amazon appears to be leading the way in constructing these so-called mega distribution centers. Close to a third of Amazon’s distribution centers are one million square feet or larger. This recent trend in larger and larger building size has been taking place just over the past 10 years. Previously, a mega distribution center was considered to be a facility measuring around 500,000 square feet.
Taller ceiling heights are also a new design feature taken into consideration for modern distribution centers. A 40-foot clear ceiling height is not uncommon for buildings currently under construction or that have been completed for e-commerce purposes. The increase in ceiling height is required as the building will feature a combination of some type of automation, racking, robotics, and pick-and-pack services situated on one or multiple mezzanines within the structure.
Even though less than 5 percent of operating costs are attributed to real estate, careful planning and consideration is being given to where a distribution center is located and what functions it will serve. The location of a dedicated e-commerce facility is pertinent as it pertains to the occupant’s ability to deliver on service commitments (i.e., same-day, next-day delivery). It truly is a consumer-driven location decision. Access to major population centers is critical for its success.
With the larger distribution centers comes a need for a larger site or acreage requirement on which to site the facility. Critical to the siting requirement is close proximity to interstate highways, intermodal facilities, and ports. Multiple means of transporting products to the facility is an advantage. The ability for the local road system to handle both truck and automobile traffic is also taken into consideration, as these facilities will need to continue to move trucks while shift changes are taking place. Existing public infrastructure with immediate access to utilities is also very critical. Projects are becoming extremely time-sensitive and there’s little or no time to wait for infrastructure to be brought to the site.
Communities that are successful in recruiting modern distribution facilities are working with employment offices and community and technical colleges to identify and pre-train prospective employees with basic skill sets. Today’s highly automated distribution centers require a semi-skilled workforce. Many of these operations need to draw from a seasonal employment pool. Qualified temporary employees are often needed during seasonal peaks such as Christmas and the holidays.
While we have just covered a few of the many changes taking place within the industry, these appear to have the greatest impact right now. But, as Ben Franklin said, “When you are finished changing, you are finished.” The industry and communities need to continue to evolve to be successful.
Project Announcements
Geartek Expands Corinth, Mississippi, Production Operations
05/03/2024
Bekaert Expands Van Buren, Arkansas, Production Operations
05/03/2024
ESS Technologies Expands Montgomery County, Virginia, Operations
05/02/2024
Martin’s Famous Potato Rolls and Bread Expands Franklin County, Pennsylvania, Operations
05/02/2024
StandardAero Expands Augusta, Georgia, Operations
05/02/2024
Nextracker-JM Steel Expand Leetsdale, Pennsylvania, Operations
05/01/2024
Most Read
-
2023's Leading Metro Locations: Hotspots of Economic Growth
Q4 2023
-
38th Annual Corporate Survey: Are Unrealized Predictions of an Economic Slump Leading Small to Mid-Size Companies to Put Off Expansion Plans?
Q1 2024
-
2023 Top States for Doing Business Meet the Needs of Site Selectors
Q3 2023
-
Making Hybrid More Human in 2024
Q1 2024
-
20th Annual Consultants Survey: Clients Prioritize Access to Skilled Labor, Responsive State & Local Government
Q1 2024
-
Manufacturing Momentum Is Building
Q1 2024
-
Last Word: Striking a Balance - Prioritizing Electric Infrastructure While Preparing for the Next Wave of Industrial Expansion
Q1 2024