At first glance one might assume this makes selecting a new location for a manufacturing plant or a distribution center easier — the closer you can get to a hub or a corridor the better. However, if companies invest without understanding the entire, complex set of cost and conditions issues, they risk making hub or corridor decisions that could have negative consequences with regard to profitability, flexibility, and competitiveness. Although logistics efficiencies and costs may be lower, these areas typically have higher labor costs, higher real estate costs, tougher permitting and regulatory approval processes, security concerns, and higher taxes as well as increased congestion — all items that can negate the logistics advantages. The key is to be aware of the trade-offs against the other investment criteria and other less expensive locations, and see how they all compare at the bottom line. To do this requires conducting a thorough, detailed, logistics-based site selection.
Site selectors notice that port-centric commercial real estate has been the hottest sector of any type over the past five years in the United States - all due to logistics.
Location’s Role in Supply Chain Optimization
One of the most important goals of conducting a manufacturing or distribution-related site selection should be to enhance one’s supply chain, with the project-specific purpose of enhancing the overall facility portfolio footprint of the company. The site selection process is closely linked to supply chain optimization via logistics.
While labor access and costs are still considered to be the number-one criteria in most surveys, for manufacturing and distribution location projects logistics is a very close second and, in many cases, actually the most important criterion, having surpassed real estate as the historical second-largest cost item.
Logistics-focused site selections should begin with a detailed logistics analysis to determine the search area. Pricing, timing, capacities, and quality of service drive the decision of what modes and routes shippers use. Regardless of the mode used, lane rates (costs), capacity, and associated efficiencies (time and service levels) are a real-time reflection of a specific lane’s competiveness. Closest lanes do not always mean cheapest lanes, especially considering issues like congestion and backhauling.
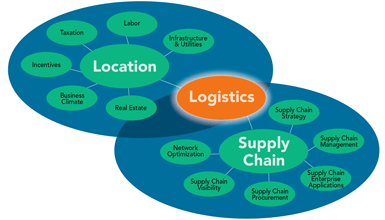
Having completed the centroid and lane analysis, a search area needs to be determined. With the logistics analysis completed and search area defined, then a screening of the other main criteria should commence, with the ultimate goal of finding the optimum location within the search area that further minimizes costs and maximizes efficiencies.
Hubs
Logistics hubs are typically Metropolitan Statistical Areas (MSAs) that are strategically connected by various popular freight corridors. These hubs have several positive attributes that attract both manufacturing and warehouse distribution projects. Typically logistics hubs are either in, close to, or have advantageous freight corridor access to major consumer markets. Some are ports and some are cities that simply became home to land-based rail and interstate interchanges. Others are strategically located between markets. All of these logistics hubs have infrastructures that accommodate large, diverse volumes of freight traffic.
There are risks common to most freight corridors. The most prevalent is congestion, as heavy usage of infrastructures leads to capacity limitations.
These hubs have also attracted significant amounts of transportation companies (carriers) and logistics firms, and have provided the skilled workforce these entities need. Support activities have also grown including real estate firms, construction firms, financial institutions, insurance companies, and government. Success breeds success as logistics clusters attract more direct investment.
Locations of some top logistics hubs in the U.S. include California’s Inland Empire, Chicago, the Dallas/Ft. Worth metroplex, Kansas City, Indianapolis, Memphis, New York City, and northern New Jersey. Other logistics hub locations include the northern Virginia area, eastern Pennsylvania, Columbus, St. Louis, Denver, Salt Lake City, Phoenix, Oklahoma City, Nashville, Birmingham, Little Rock, Louisville, and Detroit.
Port cities have naturally become logistics hubs. While their domestic distribution capabilities are hampered by not being able to distribute in all directions, they are the gateways to international trade, which brings greater volumes to and through the port hubs. Currently 95 percent of the world’s consumer market is outside North America. Site selectors notice that port-centric commercial real estate has been the hottest sector of any type over the past five years in the United States — all due to logistics. The main port logistics hubs include Los Angeles/Long Beach, Oakland, Seattle, Houston, New Orleans, Mobile, Tampa Bay, Miami, Jacksonville, Savannah, Charleston, Norfolk, Baltimore, Philadelphia, and the port of New York/New Jersey.
Some hubs already mentioned are also known as “inland ports.” As seaports continue to grow in size and capacity, they are faced with being squeezed for space. Inbound cargo from overseas will increasingly be transferred directly from ocean vessels to truck, rail, or barge and then transported to a “hinterland” location for further processing and distribution. The inland logistics hub provides the means for ocean cargo to pass through port terminals more quickly and more cost effectively, literally “clearing the decks” for the arrival of the next vessel. These inland ports can also be used as processing points for outbound freight being shipped to ports for export. Some examples of inland ports include Dallas/Ft. Worth, Chicago, Kansas City, St. Louis, Atlanta, Memphis, California’s Inland Empire, Stockton, Columbus, Charlotte, and Florida’s Inland Port.
If a product is moving more than 700 miles and is equal to or more than a container load, rail transport can be the best economical option if a location has rail access.
Air cargo also has established hubs. While commercial air passenger hubs are well known, air cargo hubs are less known. The top-10 air cargo hubs are Los Angeles (LAX), New York’s JFK, O’Hare in Chicago, Miami, Newark, Memphis, Dallas/Ft.Worth (DFW), Atlanta, Louisville, and Indianapolis.
All logistics hubs give shippers multiple choices regarding the movement, storage, and transfer of their freight. Multimodal opportunities and warehousing are located here and companies experience greater utilization rates and less backhauling headaches. In the United States there are 30 cities that produce more than 70 percent of U.S. GDP, and most of these are included here as logistics hubs.
Freight Corridors
The economic reasons freight corridors are sought after in site selection searches involve capacity, reliability, and efficiency. Greater capacity means there is an economy of scale in supporting larger volumes of freight. Reliability is the result of a coordinated effort to provide the needed corridor infrastructure to move higher volumes of freight. Greater efficiency cuts costs.
There are risks common to most freight corridors. The most prevalent is congestion, as heavy usage of infrastructures leads to capacity limitations.
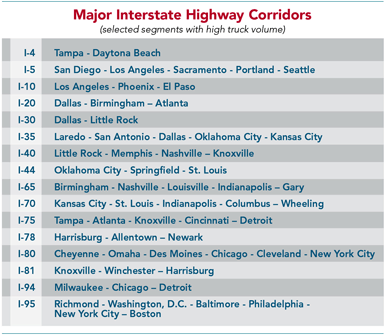
Infrastructure upkeep is another big problem. While railroads fund their own infrastructure, funding for highway repairs and expansion is provided by federal, state, and local governments. Although the U.S. highway system is world-class and very extensive, it is typically more than 30 years old and in desperate need of significant repair/upgrade. The federal fuel tax that has historically been used to fund highway infrastructure does not produce enough needed revenue. Revenues are declining as more vehicles are becoming more fuel-efficient. As the United States grows by an additional 30 million people by 2050, keeping this vital transportation infrastructure in top condition to meet future sustainable growth and safety needs will require much better long-term planning.
Another concern is higher costs of real estate along these freight corridors, which is increasing due to their perceived commercial potential. Trucking
America’s highway system is the most important nationwide infrastructure the nation has. More than 70 percent of the freight tonnage and two thirds of product value transported in the U.S. move by truck. U.S. trucking accounts for 5 percent of U.S. GDP. For more than 80 percent of the communities in the U.S., trucks are the only mode of delivering goods. Trucks are certainly flexible as they enable shippers to have quick response and flexibility in routing and scheduling.
Rail Corridors
Rail networks move the remainder of non-commodity products. Currently, if a product is moving more than 700 miles and is equal to or more than a container load, rail transport can be the best economical option if a location has rail access.
Rail also has some red flags for manufacturing and distribution location investors. In recent times, railroads encouraged trackside investment. Even as rail transport is becoming more attractive, most Class I railroads prefer to not increase their spur activity due to the disruptions on their mainline traffic. Before pursuing trackside sites, check with the railroad to be sure that the site is and will continue to be actively rail served.
The Future
Several scenarios exist that could change the makeup or location of logistics hubs or freight corridors in the future. These include:
- Demographic shifts from the Northeast to the Southeast of the U.S.
- Impact of the Panama Canal completion
- Increased shipping to U.S. via Mexican/Canadian Pacific ports
- Greater Intermodal penetration
- Significant increase or decrease in international trade and/or investment
- Growing online retailing
- Low/high fuel cost
- Advancement in big data technologies
- Additive manufacturing (3D printing)
- Drone delivery systems
- Driverless vehicles
Selecting the optimum site location is now possible and will eventually become easier with advancements in data and technology. Those that truly optimize their location footprint and overall supply chain and embrace forward planning will be the winners.