Controlling Conditions in Aerospace Manufacturing Facilities
Modern aerospace facilities have special interior environmental requirements in order to support the manufacture of cutting-edge technology and products.
2019 Auto/Aero Site Guide
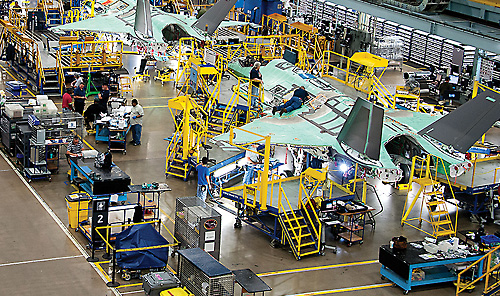
Historical Aerospace Working Environments
With the onset of World War II, the United States needed manufacturing capacity — and needed it quickly. Large aircraft and aerospace manufacturing facilities were quickly erected and enclosed: some framed in wood, others in steel. Most used trusses to provide large open spans and were clad in siding that varied from brick to steel to wood to asbestos. The choice of building materials was often driven by what was available due to the materials shortages related to the war effort.
The interiors of these aircraft manufacturing facilities were spartan at best, featuring concrete floors and exposed structure with only the necessary lighting and heating. Few were cooled or conditioned for worker comfort: doors, windows, clerestories and an occasional fan were used to manually control the “breeze” to moderate the temperature. Humidity control was seldom provided. Creature comfort for the employees was not a major concern.
The aircraft and other vehicles manufactured in these spaces were largely made of metals, often hand-made by drilling, screwing, welding, and riveting components together without a great deal of precision or automation. While quality was important, functionality and quantity or production rates were the primary manufacturing requirements of the day, and out-of-spec product tolerances and gaps were not uncommon.
Despite the environmental and quality limitations these buildings possessed, many are still used today to manufacture state-of-the-art aerospace products. The Lockheed Martin Fort Worth plant in Texas is one such example. Originally built during World War II for Consolidated Aircraft Company to build B-24 Liberators, it currently assembles the state-of-the-art F-35 Joint Strike Fighter. The building has been used to support at least nine different manufacturing programs since it was originally built.
Current Aerospace Working Environments
Today’s aircraft and aerospace products perform to a much higher level than World War II aircraft. Materials of construction include a wide range of metals, composites, plastics, coatings, and electronics. Manufacturing with these materials and components requires a wide variety of special environmental conditions, and modern assembly facilities now rely on high degrees of automation and precision. For the parts and the products to meet these higher standards of performance, the facilities and systems must perform at a much higher level, as well.
Temperature control is often required to minimize thermal expansion of the components to support closer tolerances and greater accuracy required in today’s aerospace products.
Skilled aerospace workers are in high demand throughout the industry. The quality of their working environment is often critical to retaining “the best of the best.” Humidity control can be critical in composites to prevent cut edges from absorbing excess moisture, which would cause issues when baked or autoclaved. Too little humidity supports static electricity, which can build up and damage electronic components.
Near “cleanroom” cleanliness can be required for laminating and tape-laying processes, as any dust or lint inclusions would become a potential structural flaw.
Modern bonding, sealing, and adhesive agents can have specific temperature or humidity requirements to cure and develop their engineered strengths.
All these factors need to be well-controlled within program manufacturing and assembly requirement specifications. Failure to maintain these environmental conditions can often be a cause to reject an expensive part or component. Furthermore, beyond products and components, skilled aerospace workers are in high demand throughout the industry. The quality of their working environment is often critical to retaining “the best of the best.” Well-controlled work environments are important to maintaining worker comfort and overall satisfaction. Many of the automated processes, robots, or other “non-human” workers can also require specific environmental conditions to perform with optimal accuracy.
Environments in today’s aerospace manufacturing facilities often have temperature ranges around 70-720 F. Humidity ranges can vary with the specific manufacturing processes: they can be as wide as 20–80 percent Rh or down to 40–60 percent Rh range, or less. Cleanliness also varies with the specific processes but can easily be at a Class 100K (ISO 5) cleanroom level for particulates in a facility involved with composites.
Many aerospace facilities are tall or have a large volume of space. Maintaining the required environmental conditions within an individual workspace or the entire volume is a critical consideration and requires the proper design and necessary control systems.
As the requirements and tolerances of the aerospace manufacturing environment grow more specific and restrictive, these types of facilities must be designed and constructed to support those requirements. Compared to historic aerospace and aircraft buildings, today’s facilities must be much more robustly insulated and sealed. Construction needs to be more thermal and vapor tight.
In the southeastern U.S., for example, with hot and humid summers, moisture will enter the building through every door, crack, or penetration if not well-sealed. Special attention is necessary for all exterior wall assemblies, roofs, windows, skylights, personnel doors, material transfer doors, and even large aircraft and hangar doors. Increased insulation is generally an inexpensive option to improve thermal performance compared to larger HVAC systems, increased energy usage, or failure to maintain requirements. High-quality insulation usually has a relatively short payback or return on investment.
Technical Challenges and Critical Considerations
Temperature-controlled aerospace facilities often have large doors to move components or entire aircraft in or out. Because of the size of the product, vestibules or airlocks to control and isolate airflow may not be feasible. Once these types of large doors are opened, the controlled environment within the facility is compromised and the exterior temperature and humidity conditions infiltrate the facility. After the doors are closed, the building systems can begin attempting to restore the required temperature or humidity control.
The time it takes to restore the required environmental conditions is the “recovery” time. During design of the building and related HVAC systems, the recovery time and exterior conditions should be defined. Temperature-critical manufacturing processes may need to be postponed or deferred until after the recovery period, when environmental conditions return to within required specifications and the affected components also return to temperature.
As aerospace manufacturing facilities often have tall, open volumes of space, the air in these taller spaces tends to stratify or divide into different temperature layers. If the program requires a consistent temperature throughout the entire range of the working height, then destratification is necessary. If destratification is necessary, one method is fully flooding the space by using a combination of air distribution devices to create an upper and lower blanket of conditioned air. An alternate method would be to use air displacement equipment to circulate the conditioned air vertically. Air displacement equipment typically — unfortunately — takes up valuable manufacturing floor space. In some cases, only the lower 20–30 feet of the volume need its temperature strictly maintained.
The aerospace industry is renowned for its cost-consciousness. Whether government program oversight or private industry, the costs associated with manufacturing are formidable. The heat generation of any manufacturing equipment or processes needs to be considered when designing aerospace HVAC systems. Certain aerospace components or processes, such as composites, may require ovens or autoclaves. Care must be taken to plan for the heat potential from the equipment, as well as the product once it is removed in a heated state. Test equipment such as pumps or actuators can also give off considerable heat into the interior space.
Manufacturing processes such as bonding, sealing, or the use of adhesives can generate undesirable odors. Specialized exhaust systems are used to remove these odors. Exhaust systems take conditioned air out of the interior spaces and dump it outside the building, which in turn requires additional replacement air from the outside that needs to be conditioned. This can impact the overall HVAC design, as well as result in additional energy consumption. Designing exhaust systems to their specific tasks can optimize the capture of odors while minimizing the total volume of air exhausted, thus providing significant energy savings. The same approach can be used for smoke removal from processes such as welding.
Local weather conditions should also be carefully considered to design the appropriate HVAC systems for maintaining required interior environmental conditions. While standardized local weather data can be utilized as a basis for the HVAC design, special consideration needs to be given if the facility must strictly maintain interior environmental conditions 24 hours a day, 365 days a year. For example, while California’s Mojave Desert is famous for being hot and dry, there are times when monsoonal conditions can create excessively humid conditions.
Opportunities For Savings
The aerospace industry is renowned for its cost-consciousness. Whether government program oversight or private industry, the costs associated with manufacturing are formidable. While materials and labor are the major aerospace cost factors, the embodied energy in some of these products can be substantial. Although the ability to reduce energy consumption within the product manufacturing process may be limited, the building and support systems provide numerous opportunities; the HVAC and lighting systems represent significant opportunities for energy efficiency.
With both industry and government programs looking for greater sustainability, manufacturing facilities provide unique opportunities. The use of standardized sustainability scoring systems such as LEED® have become more commonplace. Aerospace-specific processes are typically not covered by these scoring systems, but the building and its systems impacts can be measured and compared. These standards include increased levels of energy monitoring to provide early detection of potential excessive energy usage. Usually a building that does well on these sustainability standards will be energy, water, and materials usage efficient, and potentially less expensive to operate.
Modern aerospace facilities represent a unique building type with special interior environmental requirements to support the manufacture of cutting-edge technology and products. As aerospace products and components require greater precision and more specialized processes, these buildings and systems must continue to evolve to meet the ever-changing requirements.
Project Announcements
Collins Aerospace Expands Richardson, Texas, Manufacturing-Research Operations
08/12/2025
L3Harris Technologies Expands Huntsville, Alabama, Manufacturing Operations
08/12/2025
Premium Aerospace Center Expands Burns Flat, Oklahoma, Operations
08/11/2025
L3Harris Technologies Expands Camden, Arkansas, Production Operations
07/25/2025
Germany-Based MTU Maintenance Expands Fort Worth, Texas, MRO Operations
06/30/2025
Otto Aviation Plans Jacksonville, Florida, Manufacturing Operations
06/20/2025
Most Read
-
What We’re Getting Wrong About Gen Z’s Future in the Skilled Trades
Q3 2025
-
A New Course for U.S. Shipbuilding
Q3 2025
-
Optimizing Your Rail-Served Transportation Network: Strategy Before Steel
Q2 2025
-
In Focus: AI Is Changing Incentives Math
Q2 2025
-
How to Choose the Right Site for Your Factory in 2025’s Volatile Landscape
Q2 2025
-
Reshoring Reality Check from Construction
Q3 2025
-
The New Math Behind Mexico and U.S. Manufacturing Decisions
Q2 2025