Liebherr: Arming the Workforce With New Skills
Liebherr manufactures large trucks for the mining industry, including the world’s largest diesel-electric mining truck. These gigantic machines are partly assembled, tested, and certified at the plant in Newport News with complete assembly carried out at the mine. One hundred percent of the vehicles produced in Newport News are exported. Liebherr USA, Co. headquarters and three of its eight divisions are also based in Newport News.
Q4 2019
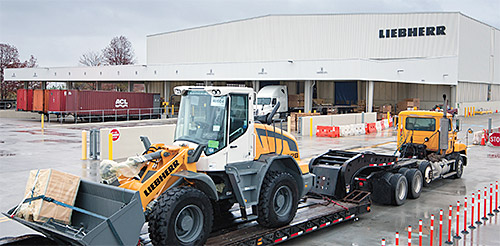
Virginia Economic Review: What trends do you see emerging from a manufacturing perspective? What’s changing and how will the landscape look in the next five to 10 years?
Cort Reiser: As we’ve entered into the fourth generation of the Industrial Revolution, our workforce needs to be more skilled. We invest a lot to train our workforce, and we work with the local educational institutions to find and develop talent from K-12, to high schools, community colleges, and local universities.
VER: How is this fourth generation, or Industry 4.0, changing the way your sector manufactures?
Reiser: Things are changing rapidly. As machines begin to talk to us and each other, we have to understand what that means for manufacturing and find new applications for such technology. Automation means we don’t have to stand and watch the work be completed; instead we are notified when it is done.
Even better, automation can provide preventative maintenance information, predicting an issue before it occurs. These shifts in the process allow more time for quality-checking and employee growth so that we are able to develop a more highly functioning team.
Now we can adapt our focus to more upper-level tasks. Somebody has to program the automated machines, and who better than a person who’s done the job by hand? So, we’re taking our existing workforce and arming them with new knowledge and skills, training them to train the next wave of manufacturing technology. Nobody is obsolete, nobody is laid off. Instead, our people stay on to help improve the process and final product, by teaching the machine the best possible way to do the work.
We will never replace our human workforce with robots. We’re a long way from that, as a company and as a society. We still need that human touch, the attention to detail, the experience, knowledge, and foresight, which only a human can contribute.
VER: What do you think states and regions can do to better position themselves to retain and attract manufacturing investments in the future? Reiser: Newport News and the area here is very attractive due to The Port. Importing and exporting from all around the world is happening just a few miles from our manufacturing facility, which puts us in a unique position. Liebherr — and other states and regions — looking to achieve these goals should invest in the smaller tiers of their supply chains, as well as acquiring a skilled workforce.
VER: So, you recommend recruiting smaller supply chain tiers, and hiring skilled employees?
Reiser: Not only recruiting them, but developing them, too. Some may not have the resources needed to achieve the best results. When a bigger company assists with training, the smaller companies benefit — and so do we. We all work from a supply chain, and it works better when we all collaborate.
Project Announcements
AVAIO Digital Plans Brandon, Mississippi, Data Centers Operations
08/21/2025
Schütz Container Systems Establishes Kenosha, Wisconsin, Production Operations
08/21/2025
GE Vernova Expands Charleroi, Pennsylvania, Operations
08/18/2025
Busch Vacuum Solutions Plans Tempe, Arizona, Operations
08/18/2025
Made Scientific Establishes Princeton, New Jersey, Manufacturing-Headquarters Operations
08/18/2025
Comcast Establishes West Palm Beach, Florida, Operations
08/17/2025
Most Read
-
Tariffs, Talent, and U.S. Expansion
Q3 2025
-
What We’re Getting Wrong About Gen Z’s Future in the Skilled Trades
Q3 2025
-
A New Course for U.S. Shipbuilding
Q3 2025
-
Optimizing Your Rail-Served Transportation Network: Strategy Before Steel
Q2 2025
-
In Focus: AI Is Changing Incentives Math
Q2 2025
-
Rewriting the Rules of Warehouse ROI
Q3 2025
-
How to Choose the Right Site for Your Factory in 2025’s Volatile Landscape
Q2 2025