In my decades of experience providing supply chain network design and operations design, I've repeatedly encountered one major challenge that businesses struggle to overcome: balancing the high cost of automation with the pressure to improve productivity, capacity, accuracy, safety and speed, particularly in distribution operations.
Automation's appeal is clear — companies seek lower cost, faster fulfillment, lower error rates, improved worker safety, and reduced reliance on increasingly scarce labor pools. Yet, implementing automation has historically been prohibitively expensive, causing even sophisticated operations to scale back ambitious plans due to financial constraints. In many cases, companies face sticker shock when presented with a comprehensive automation solution costing tens of millions of dollars, leading them to settle for less-than-ideal compromises.
However, an emerging approach offers businesses a financially savvy way to overcome these hurdles: integrating automation investments into real estate leases. While this model has been around for years in other property types, it is not widely adopted in industrial real estate. It's gaining traction due to its logical alignment with long-term operational and financial goals.
The Traditional Approach to Automation Investment
Typically, companies approach automation investment separately from real estate considerations. A common scenario might involve a manufacturer or distributor first selecting a site and leasing a building. Concurrently, they would contract with consultants or integrators to design and implement automation solutions. Often, these automation systems are financed through short-term equipment loans or funded directly from company capital.
This segmented strategy leads to substantial upfront costs and relatively high short-term financial burdens, as traditional equipment financing terms are usually limited to five years at elevated interest rates. Consequently, the overall cost per unit handled remains high, and the flexibility to scale or adapt can be significantly constrained.
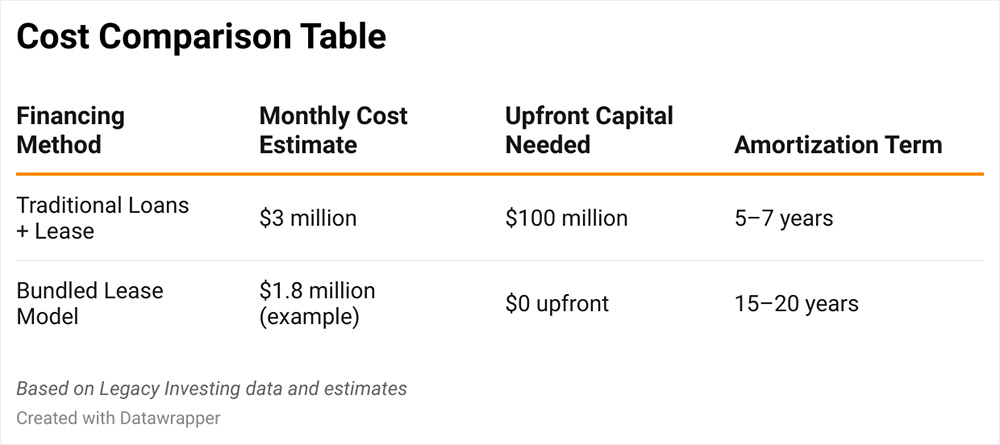
Integrating Automation into Real Estate
The alternative — and increasingly attractive — model treats automation infrastructure similarly to real estate fixtures like HVAC or lighting systems. This approach bundles the cost of substantial automation systems into the long-term lease of the facility itself, allowing tenants to spread the financial impact over a longer period, typically aligned with real estate amortization schedules of 10, 12, 15, 20 years or more. This lowers the monthly cost compared with other options and creates a long-term, predictable cost forecast with less variability or surprises.
Automation doesn't just reduce costs — it reshapes your labor strategy.
This method offers notable advantages. First, companies can avoid hefty initial investments or expensive equipment loans, making automation more accessible even to smaller operations. Second, because automation infrastructure can be amortized over an extended period at lower real estate rates, the total monthly expense is significantly lower than traditional financing options. Third, companies can align their financial strategy with their operational reality. Automation infrastructure embedded into the building lease naturally encourages tenants to plan for long-term use and benefit from operational stability.
Real-World Benefits and Scenarios
Consider a 500,000-square-foot distribution facility scenario with a comprehensive automation investment of $100 million. Traditional financing through equipment loans and real estate leases could result in combined monthly expenses of around $3 million. By bundling these costs into a long-term facility lease, however, companies could reduce monthly expenses dramatically, often achieving a significant internal rate of return (IRR) and substantial net present value (NPV) savings.
$100M
From an operational perspective, automated facilities dramatically reduce reliance on large, low-skilled labor pools. For instance, a typical manual fulfillment center might require 800 material handlers and forklift operators across three shifts, while an automated equivalent could achieve the same output with just 80 skilled mechanics, technicians, and programmers. This shift benefits regions facing labor shortages, particularly smaller counties or rural areas that struggle to attract large numbers of manual laborers but can support skilled technical roles.
Addressing Key Concerns
Naturally, businesses considering this integrated approach must weigh certain risks and practical considerations that come with automation and change. One frequent concern is the adaptability of automation infrastructure to future tenant requirements or changes in product mix. However, because most automated fulfillment solutions for picking and packing operations handle relatively uniform cube for sellable eaches — small to medium-sized items — the likelihood of reuse remains high.
Additionally, companies need to plan for technology evolution. Core automation systems like multi-shuttle storage and retrieval solutions have decades-long life cycles, while some peripheral technologies like robotic arms or vision-guided picking systems might need periodic upgrades. A flexible lease agreement that accommodates planned technology refreshes ensures operations remain competitive without incurring massive financial shocks.
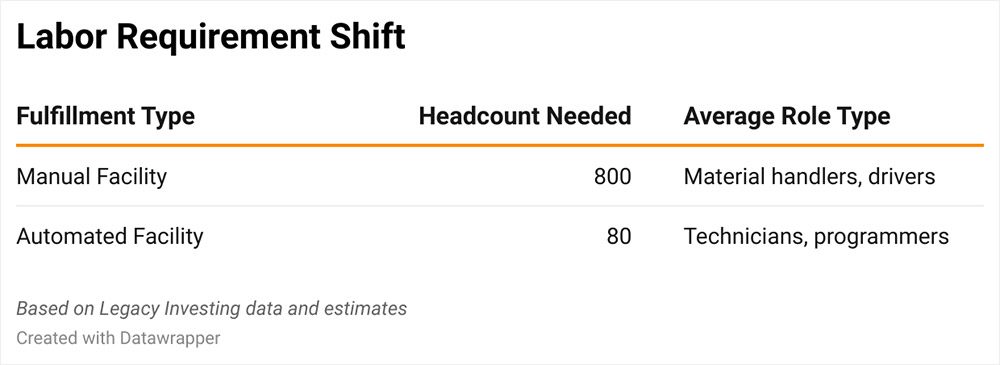
Jobs and Economic Development Implications
While automation is sometimes viewed skeptically as a job eliminator, a nuanced view reveals more complex realities. Automated facilities shift labor from numerous lower-paying, manual tasks toward fewer but higher-paying skilled positions such as mechanics, technicians, programmers, and integration specialists. For companies, this labor shift presents a strategic opportunity to reduce churn, elevate workforce productivity, and capture more value from each hire — especially in smaller communities challenged by labor scarcity.
Bundling automation into leases transforms how companies finance and deploy next-gen facilities.
Indeed, far from merely eliminating jobs, automation reshapes them — often leading to increased job quality, improved workplace safety, higher retention, and greater worker satisfaction.
Looking Forward
Ultimately, the integration of automation into real estate leases represents a strategic shift rather than just a financial tactic. It aligns business operations closely with long-term financial planning, facilitating smarter capital allocation decisions. For companies, economic developers, and landlords alike, understanding and embracing this model can provide substantial competitive advantages.
As automation continues its inexorable advancement, reshaping industries and redefining economic landscapes, integrating it seamlessly with real estate strategies offers both financial efficiency and operational excellence. It’s not just about managing today's operational challenges — it's about strategically positioning businesses and communities for tomorrow’s successes.