Many organizations struggle to transition their technology from pilot plant production to full industrial-scale operations. Scaling up is a complex challenge that must be solved both technically and interpersonally.
To succeed, organizations need a holistic understanding of the undertaking and an incremental, phased approach. It’s crucial to understand the process, anticipate challenges, and position the company for growth.
Proactive planning allows companies to transition swiftly and efficiently, keeping costs and schedules in check. Key ingredients for a successful scale-up include a strong grasp of your process, disciplined planning, a high-functioning team, and a flexible program management system.
The scale-up challenge
Scaling up often means increasing production 100 to 1,000 times. Industrial plants are massive and complex, frequently spanning several million square feet. They require large amounts of power, water, natural gas, and other utilities. Construction costs range from $300 to more than $950 per square foot, not including process equipment. If a scale-up fails, the financial and reputational consequences can be severe.
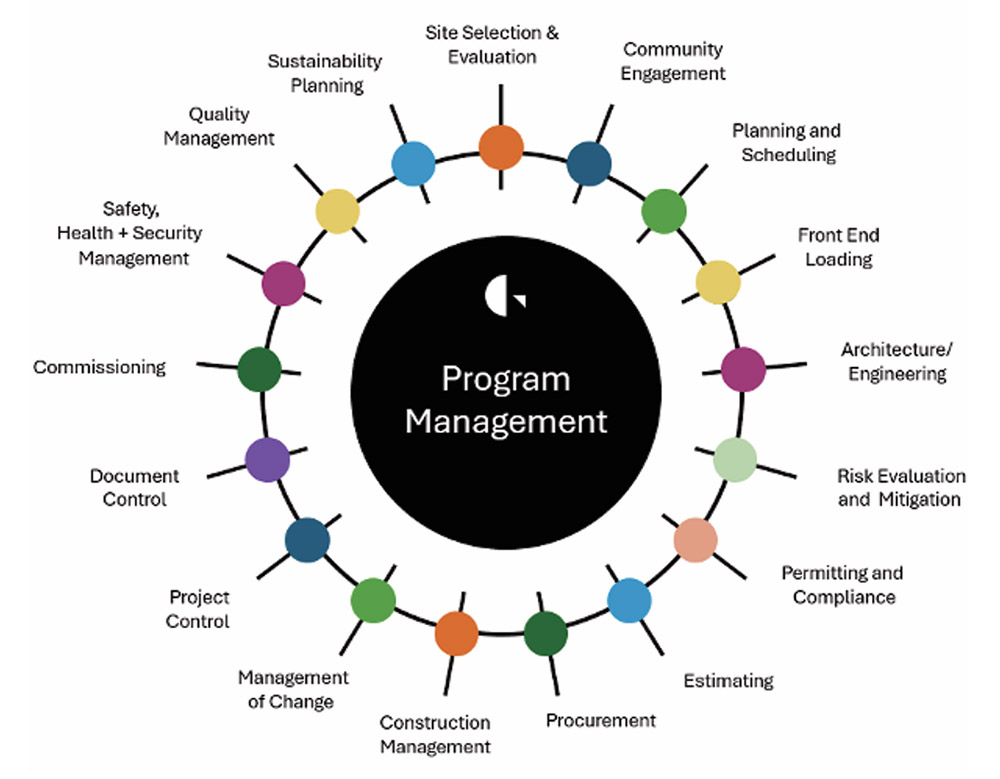
Understanding the process
The first challenge is understanding your production process. Impacts won’t be linear, and early design decisions affect the entire facility lifespan. Planning the pilot plant is as critical as planning the full project. Teams must define what data is needed and what questions must be answered before scaling up.
Engineering concerns that seem minor can have major implications. For instance, a pilot process might require a 1 percent relative humidity (RH) dry room—but the cost difference between maintaining 1 percent versus 5 percent RH is significant. One goal of the pilot plant is to identify the minimum viable manufacturing environment.
Benchmarking is another essential tool. Comparing your facility to similar ones helps challenge assumptions and guide smarter decisions. If your facility requires more acreage or utilities than a comparable site, it’s worth asking why. Good benchmarking supports efficient designs and lower ownership costs.
Disciplined early planning
Effective planning reveals the scale-up challenge in its entirety. It identifies risks, spots opportunities, and sets a roadmap.
The process begins by defining project values—your guiding principles. These lead to clear key performance indicators (KPIs) and a shared definition of success. Discussions should extend beyond budget and schedule to include long-term goals, safety metrics, and sustainability targets.
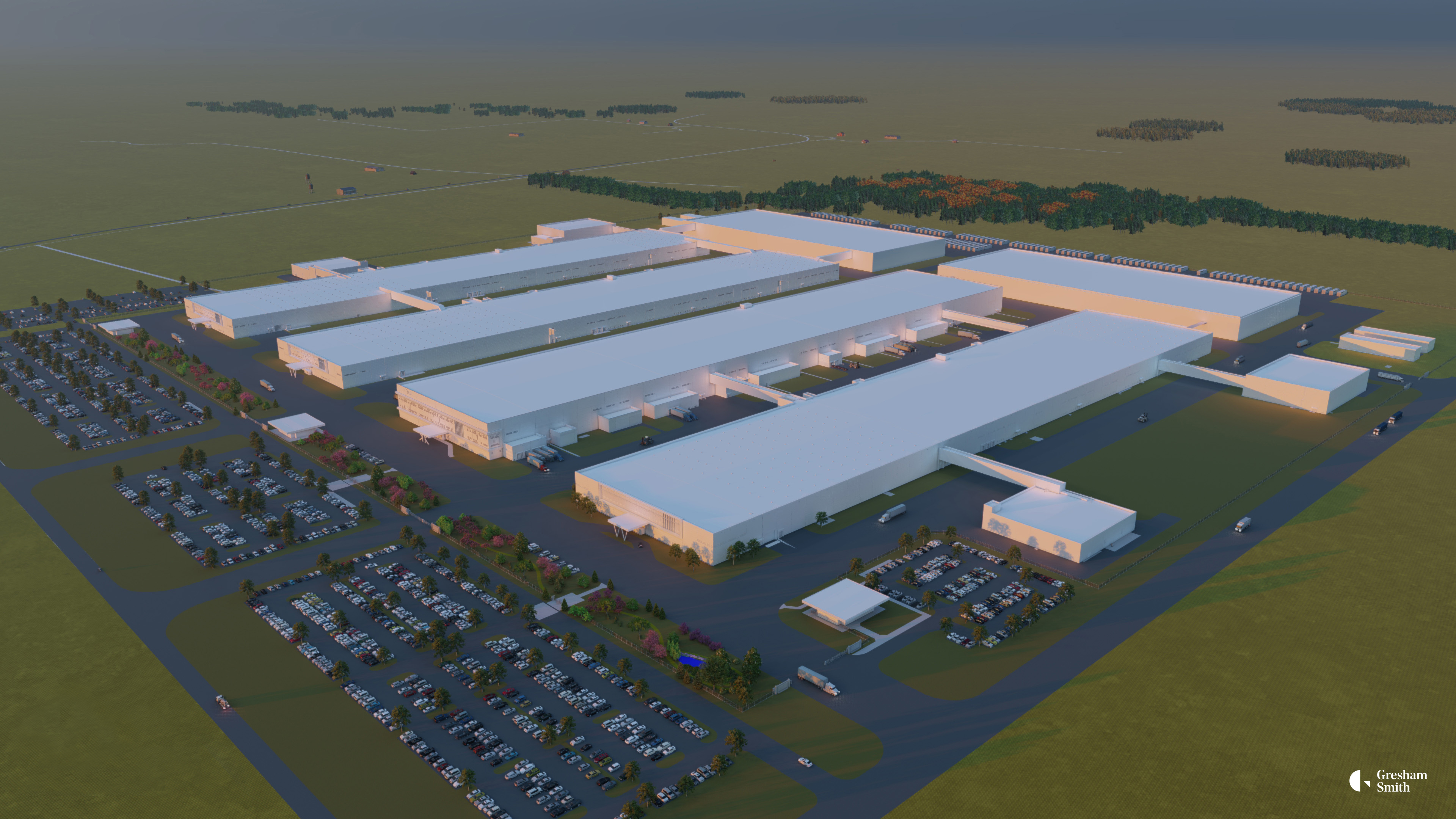
Early strategic thinking informs critical decisions like site selection and long-range facility planning. If your organization has specific goals, this is the time to bring them forward.
Large capital projects evolve through iterations, each decision building on previous ones. Ideally, projects move through “stage gates” that lock in decisions along the way. Gates are defined during planning and tracked by your program manager. As the project advances, plans become more detailed and accurate.
No plan, no matter how well thought out, will survive first contact with the actual project execution.
Most large projects must be fast-tracked—procurement and construction begin before design is complete. This adds risk, which cannot be eliminated but can be mitigated through thoughtful planning.
Budgets are also set during this phase, with contingencies aligned to risk levels. These are reduced over time as uncertainty decreases. Focus on total ownership cost (TOC), not just upfront expenses. Early-stage changes are much cheaper than those made during construction. Return on investment (ROI) analysis should continue throughout, guiding smart financial choices.
Good planning can overcome poor execution. But even the best execution won’t make up for poor planning.
Creating a high-functioning team
One of the most common mistakes is understaffing large, complex projects. You’ll need dedicated internal staff or existing employees freed from their regular duties to focus entirely on the project.
As you bring in external partners, your contracting strategy will shape how teams collaborate. Choose the approach that best fits the services involved, and understand how it influences team dynamics.
15 years
It’s critical to build a collaborative culture. Industrial projects often involve multilingual, multicultural, and remote teams. Trust and collaboration are key. Senior leaders should prioritize relationship-building.
When possible, bring teams together in person. For remote collaboration, encourage video calls and active participation. Trust—within and between organizations—improves quality and saves both time and money.
During planning and team formation, establish how decisions will be made. Many industrial projects involve joint ventures between unfamiliar partners. Rapid, informed decision-making is crucial. Defining authority and escalation paths up front helps avoid delays later.
Implementing a strong program management system
A successful project also requires a capable program management system. Two components are especially vital.
Good planning can overcome poor execution, but poor planning cannot be overcome by the very best execution.
The first is a robust project control system led by an experienced project controller. This person tracks budgets, schedules, and KPIs, comparing targets to actuals. They update projections, flag variances, and work with the team on recovery plans.
The second is a Management of Change (MoC) approach. Change is inevitable. Planning for it from the beginning, and revisiting it regularly, helps teams stay agile. MoC starts with early risk evaluation and focuses on reducing uncertainty that can trigger change.
Even the best-laid plan won’t survive first contact with execution. Your team and your plan must be ready to adapt.
What to remember
Scaling up is both exciting and high-stakes. Done well, it fuels growth. Done poorly, it threatens the business. To stay on track, understand your process, plan early and thoroughly, build a committed team, and implement flexible program management. And don’t go it alone—seek lessons learned from others who’ve already traveled this path.