Mitigating Site Risks for Industrial Projects
New technologies and improved planning identify and address site issues, saving millions in potential delays and mitigation costs.
Q3 2024
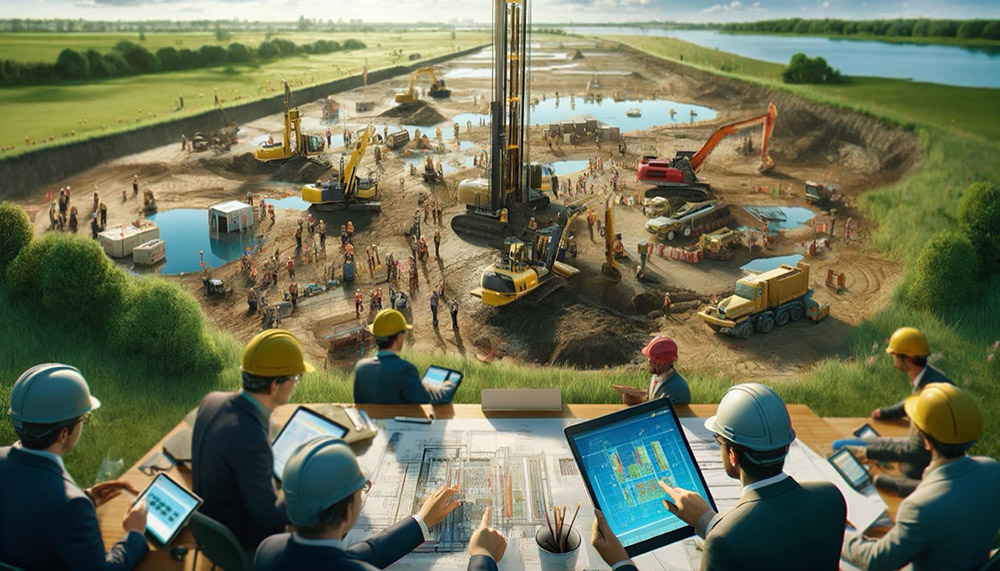
Greenfield space—especially in topographically ideal locations—is becoming rarer. At the same time, industrial construction projects are getting bigger. We are in the age of “megaprojects,” defined by the U.S. Department of Labor as construction projects spanning more than a year and having a value of at least $25 million. Megaprojects involve multiple parties and complicated logistics, and they also require much larger sites and more intensive resources than was common just a few years ago. Another factor placing pressure on the real estate market is the proliferation of new industries that require large initial investments in facilities, such as electric vehicles, semiconductors, data centers, and clean energy.
The news for site selection teams is not as bad as it may seem. By utilizing new technologies, implementing robust preconstruction processes, and involving knowledgeable engineering, environmental and testing firms, general contractors, and other building partners early, most impediments to development can be identified and overcome without a dramatic impact on cost or schedule. While these initial investments will involve some additional effort and cost, that cost is generally limited to $50,000 or less, compared to the millions of dollars that can be lost due to severe delays or excessive mitigation efforts. Additionally, the costs of site analysis may be offset by tax incentives, grants, or low-interest loans. Expenses associated with site remediation may also be rolled into initial land deals.
Site surveys and ecological assessments are nothing new, and many site selection teams may feel they are already performing with due diligence. Experienced contractors can attest, however, that they’re too often coming on board to projects only to find assessments that have been performed in a cursory way, missing important details or outright misrepresenting existing conditions. When putting together the site selection team, owners must commit to collecting and analyzing an adequate amount of data, and what is “adequate” may vary by site.
Addressing All the Risk Categories
Most sitework challenges fall into a few common categories.
Geologic
The most basic consideration for what may be lurking underground is the ground itself. Soil composition and bearing capacity, along with slope stability, will determine the basic structural design of an industrial facility. Soft soils, for example, may necessitate pilings to stabilize the structure. Fault lines or other seismic risks are also a concern.
The amount and type of subsurface rock is another major consideration. Rock close to the surface will significantly increase the amount of excavation, blasting, and fill dirt required.
Beyond identifying the amount of rock, a geotechnical survey should identify the types of rock and their classifications, especially if the site is a known expansive rock area. Identifying rock classification may require additional borings as well as lab testing.
By utilizing new technologies, implementing robust preconstruction processes, and involving knowledgeable engineering, environmental, and testing firms early, most impediments to development can be identified and overcome without a dramatic impact on cost or schedule. Water tables and other sources of groundwater should be identified, as they can cause flooding if pumps or proper drainage are not designed and installed. Surface water and wetlands will be easier to spot, but these types of water also require assessment during preconstruction so that appropriate design responses can be developed.
Buried Infrastructure
With greenfield sites becoming rarer, teams should keep in mind that existing infrastructure such as gas lines or water pipes (including wastewater and stormwater pipes) may be buried onsite. Some industrial project teams have encountered extensive networks of such pipes once excavation began—networks that did not show up on their environmental or geotechnical surveys. Utility easements are an additional factor for teams to research.
Environmental Contaminants
Sites that have been previously occupied may have environmental contaminants. These may include buried tanks or soil that contains lead, oil, asbestos, or other toxins.
Geotechnical reports that gather and process an adequate amount of data will help the building team identify geologic concerns as well as buried infrastructure. This, in turn, will allow them to optimize site layout, minimize excavation, properly design pumps and drainage, develop a grading and/or shoring plan, lay out utilities, design load-bearing components, and more.
Experienced site selection partners may perform environmental research that goes beyond standard tests—which typically include soil borings, monitoring of groundwater, etc.—and examine historical property information or government and regulatory agencies’ information about the site. This can help ensure that all potential sources of contamination are identified, heading off problems at a later stage.
New Infrastructure and Utilities
Beyond physical site conditions, site selection teams should consider the availability of utilities to support plant operation, particularly power and water supply. The same factors that constrain real estate availability, such as the proliferation of megaprojects and an uptick in construction to support new industries, also make it more challenging to successfully compete for resources.
Utility Dive reported that “grid planners expect nationwide electricity demand to grow 4.7% over the next five years—while 2022 estimates called for just 2.6% growth—[yet] the electric grid ‘is not prepared for significant load growth.’” General contractors can help negotiate with power companies, communicating about the planned facility’s average loads, peak loads, power factors (or the efficiency with which equipment utilizes the power supplied), hours of facility operation, and more. The logistics of power provision, along with cost estimates, can then be established. Many industrial project teams are choosing to make additional investments in onsite power supply or storage, especially with an eye toward augmenting peaks in demand and shifts in load.
$50,000 — that's the estimated cost of comprehensive site analysis, a small price compared to the millions that can be lost due to severe delays or excessive mitigation efforts. When planning site utilities, wastewater is another consideration. Just as capital project teams are exploring onsite ways of augmenting power supply, many are now considering the onsite treatment or reuse of wastewater.
Ensuring the necessary water supply will be a major priority during site selection, since unlike power generation or wastewater treatment, water is not a resource that can be augmented by the project owner. Experienced general contractors will be able to accurately estimate a facility’s operational water requirements and will also be able to match project owners with the state and other governmental resources that may have collected data on water capacity by location.
Working with engineering, construction, and testing partners who are knowledgeable about regional conditions is also important. As an example, one manufacturer relied on a geotechnical survey that would, under most circumstances, have been adequate. However, the construction project was located in an area that contained expansive shale, and the report did not test the underlying shale formation for pyritic material, which was common to the region. Pyritic shale, an expansive material, can lead to significant problems years after construction when exposed to air during grading activities. In this case, the situation was discovered and addressed, but it serves as a cautionary tale regarding the ways in which missed opportunities for early data collection and mitigation activities can impact a project.
The focus during site selection and early-stage planning should be on identifying all factors that will influence the scope of work required to develop the site. Working with experienced contractors and other site selection partners will secure the best outcomes.
Project Announcements
MR6 Tech Services Plans Huguley, Alabama, Manufacturing Operations
07/29/2025
Adient Plans Normal, Illinois, Production Operations
07/29/2025
UK-Based WB Alloys Plans Danville, Virginia, Manufacturing Operations
07/29/2025
L3Harris Technologies Expands Camden, Arkansas, Production Operations
07/25/2025
Baltimore Fabrication Expands York County, Pennsylvania, Manufacturing Operations
07/25/2025
Mueller Streamline Expands Wynne, Arkansas, Manufacturing Operations
07/25/2025
Most Read
-
20th Annual Area Development Gold and Silver Shovel Awards
Q2 2025
-
In Focus: AI Is Changing Incentives Math
Q2 2025
-
Optimizing Your Rail-Served Transportation Network: Strategy Before Steel
Q2 2025
-
How to Choose the Right Site for Your Factory in 2025’s Volatile Landscape
Q2 2025
-
From Silicon to Server: Mapping the Data Center Supply Chain
Q2 2025
-
Tariffs, Talent, and U.S. Expansion
Q3 2025
-
First Person: David Robey, Co-CEO of QTS Data Centers
Q2 2025