Many top U.S. manufacturers already recognize this reality, of course, and have pushed the nation far down the road toward that goal. The federal government also has recently hopped on board with some initiatives to give various types of digital and other advanced manufacturing very real boosts. And with the ever-intensifying interstate derby to land capital investments and jobs in advanced manufacturing, new regions are coming to the fore to join traditional industrial capitals to nurture this unique American advantage.
“Digital is how the United States wins in manufacturing,” says William King, chief technology officer of the Digital Manufacturing and Design Innovation Institute, a new research center on Goose Island in the Chicago River. It was launched in 2014 with $70 million in funding from the federal government and $250 million in commitments from many of the icons of U.S. manufacturing, including General Electric, John Deere, Procter & Gamble, Caterpillar, Lockheed Martin, and Boeing.
There has been a groundswell of support for advanced-manufacturing initiatives...there’s a lot of activity in the Midwest, but there are things going on from coast to coast with different applications. Geographic clustering will emerge more over time. Larry Gigerich, managing director of Ginovus, a site-selection consulting firm based in Indianapolis
“The whole world looks to the U.S. for digital innovation, [and] digital is a really good fit for the American way of doing things, for our business and culture and education system,” King says. “And as manufacturing becomes much more of an information industry, we’re really poised to win because of the things that have helped America to win at digital in other industries.”
Midwest Rides the Digital Wave
Already, for example, the Chicago institute is attracting interest not just from its supporting behemoths but also from small and medium-sized manufacturers that also must ride the digital wave for American manufacturing overall to dominate the era. One of them is AskPower, an Aurora, Ill.-based maker of terminal lugs, electrical splices, and other fasteners and connectors for the telecom, automotive, and other sectors. CEO Steve Kase wants the institute’s guidance in bolstering AskPower’s digital chops in both product development and in process improvement for designing, costing, manufacturing, and replicating its components — and in making sure that at every step along the way, the company is completely integrated as possible with customers’ digital environments.
“Buttressing suppliers like us is totally critical” to the success of digital manufacturing overall, Kase explains, “because it’s one thing to have the front end of the supply chain — the major manufacturers like General Electric — ‘geeked up’ for digital manufacturing, but what if there are no suppliers to play with them?”
Besides the digital-manufacturing institute in Chicago, under its four-year-old effort the federal government also has set up manufacturing innovation hubs in Youngstown, Ohio, to advance 3-D or “adaptive” printing; in metro Detroit, to develop lightweight materials and technology; and at North Carolina State University in Centennial, N.C., to devise smaller, faster, and more efficient power electronics. Others are planned as well.
Interestingly, the Obama administration’s push to seed various outposts across the country with responsibility and funding to develop specific aspects of advanced manufacturing has coincided with the flourishing of existing and new hot spots that are being created and nurtured by state and local governments, industries, and specific big companies.
“There has been a groundswell of support for advanced-manufacturing initiatives,” says Larry Gigerich, managing director of Ginovus, a site-selection consulting firm based in Indianapolis. “There’s a lot of activity in the Midwest, but there are things going on from coast to coast with different applications. Geographic clustering will emerge more over time.”
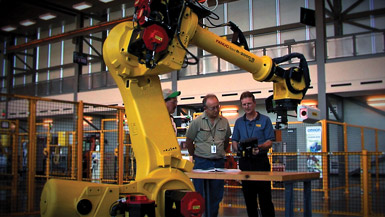
The Southeast: A Formidable Hub
Already, however, in addition to the industrial Midwest with its depth and diversity of manufacturing from steel to farm equipment to autos to machine tools, the Southeast is emerging as a formidable regional complement in various aspects of advanced manufacturing. Much of this is based on the growth of automotive and aerospace fabrication there, and it has been accelerated by the savvy of state and local governments and universities.
For instance, Airbus in September opened its first civilian aircraft factory in the United States, in Mobile, Ala., a $600 million facility situated on 116 acres on an old Air Force base where the Europe-based manufacturing consortium — Boeing’s biggest global competitor — has begun assembling its latest, most fuel-efficient airplanes. The city and state dangled generous tax breaks and other financial incentives to attract Airbus — and the prospect of up to 4,000 jobs with the company and suppliers over the next several years — to the city of about 200,000 people, where unemployment has continued to hover at about 8 percent.
Meanwhile, about 200 miles to the north of Mobile, in Tuscaloosa, Ala., Mercedes-Benz recently announced a $1.3 billion, 300-job expansion of it auto-assembly plant, representing one of the single largest investments for the German automaker at the site. Mercedes-Benz will install new robots and other advanced equipment by the middle of 2017 in order to support assembly of the brand’s next generation of sport-utility vehicles for the U.S. and worldwide markets.
Expansion in Alabama by both auto and jet assemblers and their many suppliers has been given a big boost over the last few years by the Alabama Robotics Technology Park in Tanner, Ala. It hosts about 75 employees each month sent for training by companies with manufacturing investments in the state, which also include Honda, Toyota, and Navistar. The trainees attend classes on safety, maintenance, welding, or operating robots and programmable controllers. The park has been open for nearly five years and doesn’t charge for the training. Once the third phase of the facility, where ground was broken in late 2014, is complete, Alabama will have invested more than $73 million overall.
“It’s such a huge success,” Gigerich notes. “Companies can use this facility to train their senior employees, who can then go back to train other people on the front line. And of course robotics manufacturers like it because they can showcase their equipment there. It’s become a real center of excellence.”
The New Era of Advanced Manufacturing: Coast-to-Coast Examples
All over the country, venerable industrial companies also are coming up with new techniques and products that assure a brighter future for them as the new era of manufacturing progresses.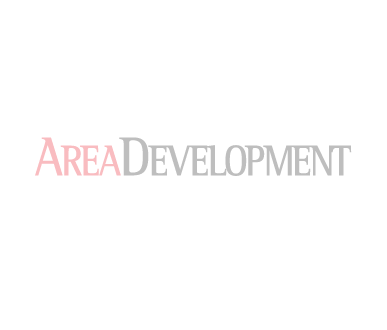
-
Digital Manufacturing and Design Innovation Institute
The Digital Manufacturing and Design Innovation Institute, a new research center on Goose Island in the Chicago River, was launched in 2014 with $70 million in funding from the federal government and $250 million in commitments from many of the icons of U.S. manufacturing, including GE, John Deere, Procter & Gamble, Caterpillar, Lockheed Martin, and Boeing.
-
Alabama Robotics Technology Park
Expansion in Alabama by both auto and jet assemblers and their many suppliers has been given a big boost over the last few years by the Alabama Robotics Technology Park in Tanner, Ala. It hosts about 75 employees each month sent for training by companies with manufacturing investments in the state, which also include Honda, Toyota, and Navistar.
-
Macomb Community College
Macomb Community College, in suburban Detroit, is leveraging financial support from Goldman Sachs and JPMorgan Chase to forge a new role for institutions like itself: boosting the local manufacturing base in a much more tightly integrated way. Macomb is fostering development of software and big-data applications for a range of industrial IT needs, including automotive “infotainment” and connectivity, as well as coming up with innovations for big area defense contractors such as tank manufacturer General Dynamics.
-
Rush Manufacturing
In Detroit, Rush Manufacturing, a major supplier of parts and logistics to the auto industry, is using highly advanced ultrasonic welding in the manufacture of plastic components that go into instrument modules for cars that it makes with global partner Faurecia, employing about 500 people in inner-city Detroit in the process.
-
United Parcel Service
In Louisville, Ky., United Parcel Service recently rolled out 100 industrial-grade 3-D printers at its logistics hub there, in an experiment to make everything from iPhone components to airplane parts.
-
Standby Screw
A 76-year-old family-owned fastener manufacturer, Standby Screw, can keep up with making about 1,100 different parts for cars, appliances, and other products only by operating a pair of dual-armed collaborative robots that are so versatile they can do everything from pack boxes to run milling machines with only occasional supervision. With their help, the company ships out about two million pieces every week.
-
Hostess Brands
Hostess Brands has come back from bankruptcy in part by streamlining production by upgrading the equipment at its pared-down number of bakeries with robots that pack Twinkies into boxes.
-
John Deere Electronic Solutions
John Deere Electronic Solutions recently opened a $22 million addition to its plant that will use advanced techniques perfected by its parent company to manufacture power electronics components and systems designed to perform in rugged and extreme environments in agriculture, construction, and forestry.
Micromill is a new casting technology that allows for alloys to be digitally shaped more easily than traditional aluminum, making it a prime candidate for complex parts such as fenders and door-panel interiors in cars. Micromill technology, announced in 2014, produces an alloy that is 40 percent more formable than today’s automotive aluminum, allowing for the use of a thinner, lighter aluminum sheet without compromising dent resistance. And Micromill can turn molten metal into aluminum coil in just 20 minutes versus 20 days using traditional methods.
In Louisville, Ky., United Parcel Service recently rolled out 100 industrial-grade 3-D printers at its logistics hub there, in an experiment to make everything from iPhone components to airplane parts. The company’s 3-D project is run by an Atlanta startup in which UPS has invested, wanting to find out if 3-D printing centers could shorten supply chains and cut into its $58 billion annual transportation business — or give it a leg up in a potentially emerging market for local production and delivery.
In Detroit, Rush Manufacturing, a major supplier of parts and logistics to the auto industry, is using highly advanced ultrasonic welding in the manufacture of plastic components that go into instrument modules for cars that it makes with global partner Faurecia, employing about 500 people in inner-city Detroit in the process.
In Macomb County, Mich., in suburban Detroit, Macomb Community College is leveraging financial support from Goldman Sachs and JPMorgan Chase to forge a new role for institutions like itself: boosting the local manufacturing base in a much more tightly integrated way. Macomb is fostering development of software and big-data applications for a range of industrial IT needs, including automotive “infotainment” and connectivity, as well as coming up with innovations for big area defense contractors such as tank manufacturer General Dynamics.
In Berea, Ohio, a 76-year-old family-owned fastener manufacturer, Standby Screw, can keep up with making about 1,100 different parts for cars, appliances, and other products only by operating a pair of dual-armed collaborative robots that are so versatile they can do everything from pack boxes to run milling machines with only occasional supervision. With their help, the company ships out about two million pieces every week.
In Kansas City, Mo., Hostess Brands has come back from bankruptcy in part by streamlining production by upgrading the equipment at its pared-down number of bakeries with robots that pack Twinkies into boxes.
In Fargo, N.D., John Deere Electronic Solutions recently opened a $22 million addition to its plant that will use advanced techniques perfected by its parent company to manufacture power electronics components and systems designed to perform in rugged and extreme environments in agriculture, construction, and forestry.
And there are hundreds of other examples of how states and localities are working with manufacturers to create and grow outposts for advanced manufacturing. In letting a thousand such ideas and applications attempt to take on vitality, America is placing lots of bets on grabbing hold of the digital future of manufacturing.