GLOBALFOUNDRIES - 2010 Gold Shovel Project of The Year
What does it take to win the largest economic development project in New York's history? Two things-clear strategic vision for the future and a simple cold call.
June/July 10
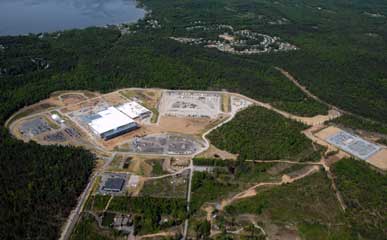
To be clear, AMD had no plans at that time to build a new fab in New York or anywhere else. But with that one cold call, and four years later, New York had the deal on the largest private economic development project in its history. The GLOBALFOUNDRIES* project will result in the construction of a $4.2 billion semiconductor manufacturing facility, called Fab 8, at the Luther Forest Technology Campus and the creation of 1,465 new high-tech jobs in New York. It will also solidify the state's position as a global high-tech center. The lessons learned from this project can add value to any site selection process.
New York's Approach - Make Them an Offer They Can't Refuse
In the late 1990s, New York adopted a new economic development strategy with an impressive goal: to attract a major semiconductor manufacturer to the state - not just any manufacturer, but an industry leader whose presence would spur the development of an entire semiconductor industry cluster. The new strategy was designed to help replace New York's declining manufacturing industries with the high-tech, high-value jobs of the future. According to Dennis Brobston, President of SEDC, "Our state and regional leaders chose to focus on a semiconductor industry strategy for the transformative effect it could have on the economy and for the opportunities it would afford us in the future. We knew there were hard work and investment and risk ahead of us, but firmly believed we had the partners and assets needed to be successful."
New York's team did its homework. A strong development team with representatives from the public, private, and academic sectors worked together. Industry experts were consulted so the team would better understand the semiconductor industry and could identify the companies that would most benefit from New York's assets. The team visited the Dresden semiconductor cluster and learned about the type of incentives the State of Saxony and German governments gave to semiconductor manufacturers. SEDC identified an ideal site for semiconductor manufacturing and worked to make it shovel-ready with financing from local partners such as the Adirondack Trust Company. State and local governments began needed infrastructure improvements, and state leaders committed to negotiating a competitive incentive package when the time came.
New York believed that AMD was a perfect candidate for its pitch, and AMD agreed to New York's request for a meeting. By all measures, New York's cold call was a success. When describing the initial meeting, Terry Caudell, who led AMD's site selection process and is currently Project Manager for the GLOBALFOUNDRIES Fab 8 project says, "They [the New York team] felt that AMD was a primary candidate for the semiconductor assets and resources that New York had put in place. They presented an opportunity to us that we felt was unique, and we made the decision then to further explore whether New York fit into AMD's long-term capacity strategy."
Initial interest led to a site visit so AMD could learn more about the region. A full spectrum of community partners participated in the site visit to give AMD a complete picture of the assets in place to support a new fab. Team members included state and local elected leaders; local public agencies like the Saratoga County Water and Sewer authorities; private partners such as SEDC, the Center for Economic Growth (CEG), and National Grid; and academic partners including the College for Nanoscale Science and Engineering (CNSE) and Hudson Valley Community College (HVCC). The visit convinced AMD it should move to the next step. Says Caudell, "Our first exposure to all of the pre-development work done at the Luther Forest Technology Campus was impressive. We looked at this site in context of the work we had already done in Dresden and went away feeling that this team had done its homework."
Site Selection Begins in Earnest
After visiting New York, AMD initiated its formal site selection process. AMD did not settle on New York immediately, but approached its potential capacity expansion from a global perspective. Every region with a 300-mm factory was evaluated against several criteria including economics, labor, education, utilities, political stability, cost of manufacturing, and availability of capital. The resulting short list included three regions: Dresden, Germany; Singapore; and New York.
In parallel with its global search, AMD also evaluated 10 New York sites with the potential to support a high-tech industry cluster. The Luther Forest Technology Campus stood out as the clear winner. The campus, located 20 minutes north of the Albany, is a 1,014-acre greenfield site with few wetlands. The region is home to a highly skilled work force and has nearby R&D assets like IBM's research park in Fishkill, the College of Nanoscale Science and Engineering at the University at Albany, and the International Sematech Consortium. It's close to major transportation routes, and utility companies had already developed plans to build the advanced utility infrastructure at the campus.
The final piece of the puzzle was the development of a comprehensive cost model to predict the true cost of manufacturing in each region around the world. The model factored in construction costs, utility costs, local labor rates, and potential benefit packages, and provided a realistic cost per wafer estimate in each location. The cost model turned out to be a critical tool that helped both AMD and New York understand what type of incentive package would make New York globally competitive. New York simply had to commit to an incentive that brought the cost of manufacturing in the state in line with the cost of manufacturing in Singapore or Germany. Would New York be prepared to offer AMD such a deal?
Project Announcements
GE Appliances Expands Jefferson County, Kentucky, Operations
06/30/2025
ValorFlex Packaging Plans Bowling Green, Kentucky, Production Operations
06/30/2025
Neuro.io Plans Terrebonne Parish, Louisiana, Operations
06/30/2025
Germany-Based MTU Maintenance Expands Fort Worth, Texas, MRO Operations
06/30/2025
Cascade Die Casting Group Expands High Point, North Carolina, Manufacturing Operations
06/30/2025
BuildOps Plans Raleigh, North Carolina, Operations
06/30/2025
Most Read
-
20th Annual Area Development Gold and Silver Shovel Awards
Q2 2025
-
First Person: Joe Capes, CEO, LiquidStack
Q2 2025
-
The Legal Limits of DEI in Incentives Agreements, Hiring, and Contracting
Q2 2025
-
From Silicon to Server: Mapping the Data Center Supply Chain
Q2 2025
-
39th Annual Corporate & 21st Annual Consultants Surveys: What Business Leaders and Consultants Are Saying About Site Selection
Q1 2025
-
Rethinking Life Sciences Site Selection in a Resilient and Dynamic Market
Q2 2025
-
Top States for Doing Business in 2024: A Continued Legacy of Excellence
Q3 2024