Logistics/Distribution Projects on the Rise
In the coming decades, businesses and communities seeking to remain competitive in the logistics arena will need to continuously innovate in order to adapt to the changing environment.
Winter 2012
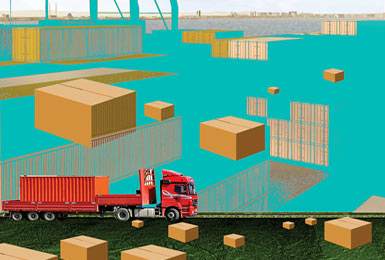
Logistics, as a business concept, evolved in the 1950s due to the increasing complexity of supplying businesses with materials and shipping out products in an increasingly globalized supply chain. This led to a call for experts referred to as supply chain logisticians, people who focus on "having the right items, in the right quantity, at the right time, at the right place, in the right condition to the right customer."
There are three primary types of logistics that comprise the industry: inbound, outbound, and reverse. Inbound logistics concentrates on purchasing and arranging inbound movement of materials, parts, and/or finished goods from suppliers to manufacturing or assembly plants, warehouses, or retail stores. Outbound logistics is the process related to the storage or movement of the final products, and the related information flows from the end of the production line to the end user. And, as one might expect, a portion of what goes out typically comes back creating the need for reverse logistics, which is the process of handling products that are returned.
In the United States alone, according to recent reports, logistics is a $250 billion per year industry. The growth and progress of this industry can be attributed to many things, most notably, improved road systems, the rise of the Western economy, and what seems to be an insatiable appetite of the American people for the consumption of goods.
Logistics is estimated to account for 8.7 percent of the total U.S. GDP and is continuing to grow, not just in services provided and outsourced, but also in terms of volume. The industry's third-party logistics (3PL) provider element accounts for more than $78 billion and is estimated to be growing at a rate of 15 percent to 20 percent per year principally because of the intrinsic benefits, such as the reduced need for personnel, reduced transportation/distribution costs, potential for improved customer service, improved cycle time, and the ability to free up needed capital to deploy in other more strategic core business areas.
Change as a Constant
With all of this growth and progress, there is change. Change is a given in the world of business; the only variable is the rate at which change will occur. Of the top 50 Fortune 500 companies listed in 1991, only 15 remain as of 2011. Changes in the U.S. economy have heightened the importance of goods distribution as an economic engine. With the decline in manufacturing jobs, the result has been a raised profile of the goods distribution industry as a resource of well-paying industrial jobs that may not require postsecondary degrees.
The Bureau of Labor Statistics projects a 4.2 percent increase in wholesale trade employment, and 9.8 percent in transportation and warehousing employment by 2018. These projections - along with expanding geographical boundaries and the rate at which 3PLs are anticipated to grow - all point to a favorable future in logistics/distribution projects. The strongest growth is anticipated within the mixed freight, pharmaceutical products, commodities, electronics, and other electrical equipment categories.
The value of U.S. imports and exports have more than doubled since 1989 and are now more than $3 trillion. In addition to the changing economy, recent studies indicate that 95 percent of the U.S. CEOs believe they should have some form of logistics strategy, and nearly 50 percent of the nation's CEOs are incorporating supply chain planning into their overall business strategies.
Newer, More Modern Facilities
During the 1990s construction of logistics buildings increased. In fact, demand for warehouse and distribution space has steadily increased during the past three decades, and commodity shipment trends indicate that space demand is likely to continue to grow.
A recent report produced for the National Association of Industrial and Office Properties (NAIOP) projects the need for some 700 million square feet of new space to be built between now and 2018. In addition to new facility needs, there is also a significant need to replace older obsolete facilities, which averaged 300 million square feet between the years 1990 and 2003. If this trend continues, we might anticipate that 3.5 billion to 4 billion square feet of warehouse and logistics space will be built by 2020. The end of the recession has allowed companies to focus on expansion and deployment of new, more sophisticated technologies, which correlate to a rise in logistics and distribution projects.
Real estate inventory and employment related to logistics buildings have also shifted in design, with the result being more square footage per worker today than in the past. Today's centers are modern and efficient and are the heart of logistics in providing control, efficiency, and velocity for goods moving through the system. Elements of warehouse and distribution centers continue to evolve and to accelerate through several trends, such as the general trend toward outsourcing to 3PLs, the unprecedented growth of e-commerce, and the importance of the partnership aspect of the manufacturer/marketer and logistics provider relationship.
4PLs and Other Trends
Outsourcing provides the ability to leverage another's strengths, which may free-up internal distribution infrastructure and resources. Outsourcing may be directed to 3PL providers; however, there is an emerging trend in 4PLs; whereas the 3PL provider targets a specific function, the 4PL provider targets the management of an entire process to include transportation, customer relations, billing, and human resources.
Because of the forces shaping supply chains, changes in warehousing and distribution will continue. Competition will continue to pressure operations to be more efficient while catering to more demanding customers. The key is that the industry is always changing, and an outside provider may be more nimble, allowing a company that has traditionally handled distribution to better control expenses and utilize internal resources.
Other trends impacting growth in the industry and decisions of where to locate warehouse/distribution/logistics facilities include reductions in transportation costs. These reductions have enhanced productivity, opened new markets, and altered trading patterns. This, in turn, has led to just-in-time logistics planning that seeks to minimize inventories and storage, create incentives for more horizontal integration of supply and distribution networks, and spur development of new distribution hubs.
The distinction between distribution and production has become increasingly blurred with value-added services such as parts, production, assembly, and customer service all integrated under the same distribution center roof. Other considerations include centralization vs. regionalization, government regulations, security, technology, business management, and further business drivers such as energy and work force quality/availability, real estate, land and building, price/availability, business tax structure, and opportunities for economic development incentives.
Project Announcements
Little Leaf Farms Plans Coffee County, Tennessee, Production Operations
07/02/2025
White Rock Truss & Components Expands Lee County, Virginia, Operations
07/02/2025
Fox Tank Company Plans Coshocton, Ohio, Operations
07/02/2025
Ascentek Expands Shreveport, Louisiana, Operations
07/02/2025
ProBio Establishes Hopewell, New Jersey, Gene Therapy Operations
07/02/2025
22nd Century Technologies Expands Fairfax County, Virginia, Headquarters Operations
07/02/2025
Most Read
-
20th Annual Area Development Gold and Silver Shovel Awards
Q2 2025
-
First Person: Joe Capes, CEO, LiquidStack
Q2 2025
-
The Legal Limits of DEI in Incentives Agreements, Hiring, and Contracting
Q2 2025
-
From Silicon to Server: Mapping the Data Center Supply Chain
Q2 2025
-
39th Annual Corporate & 21st Annual Consultants Surveys: What Business Leaders and Consultants Are Saying About Site Selection
Q1 2025
-
Rethinking Life Sciences Site Selection in a Resilient and Dynamic Market
Q2 2025
-
Top States for Doing Business in 2024: A Continued Legacy of Excellence
Q3 2024