BIM systems provide a virtual platform for real-time collaboration; architects and engineers can share design and construction aspects of the building, allowing them to work in parallel instead of sequentially, thus significantly reducing time spent on a project. By sharing their designs, problems are identified early, dramatically reducing cost of quality. In view of this, BIM systems are not merely producing a model of a building, but also providing a platform for real-time collaboration, logistics, and quality management.
In short, the main value points of BIM (systems and practices) are:
- Providing means for collaboration, shortening the project time span
- Allowing for early detection of quality issues, lowering cost of quality
- Supporting lean logistics for construction
What Is in It For FM?
To answer that question in a practical way, we need to look into typical problems facility managers encounter during the life cycle of buildings and identify new opportunities that FM can leverage when adopting BIM models and systems.
FM professionals are concerned with operating and maintaining buildings for their life cycle, which can span 30 years or even more. During the life cycle, we typically see periods of operations alternated with periods in which reconstructions take place.
Commissioning — Perhaps one of the most significant events is the hand-over from construction to use: commissioning. Many articles and conversations on facility management have been dedicated to this subject, where comments vary from “if they only had involved us in the design, the building would have been so much cheaper and simpler to operate and maintain” to “it is hard to commission a building, chasing after all relevant information we need.”
One of the major problems we see around managing buildings is the loss of building-related information that typically occurs during handovers between the various stages. Using BIM models, this data drop is diminished.
In his book BIM for Facility Managers, Paul Teicholz states: “An inordinate amount of time is spent locating and verifying specific facility and project information from previous activities.” The use of BIM systems and models can add significant value to solve this problem in a number of ways: early-involvement with design, commissioning assessments, and asset data extraction for operations from the model.
Early-involvement — BIM platforms allow for collaboration in real time. Facility managers typically are absent during design stages, when they can add real value to this process and result by adding their experience to the team. Addressing questions like, “Which design elements are particularly expensive to maintain and operate and why?” and “ Is this an affordable price to pay?” are questions where FMs can add unique value by virtue of their experience. And the good thing is access comes for free: the only BIM-related tool an FM needs during design is a model viewer.
Early-engagement does require a proactive attitude from the facility manager him/herself. Now that BIM-connection tools for facility management are entering the market, facility managers can leverage them to earn a seat at the table during design using financial arguments: FMs can take (parts of) the designs of buildings, run their bill-of-materials in the CAFM/IWMS system, and report to the project team on projected cost of operations and maintenance even before the design is completed. The earlier FMs participate, the more influence they can have on the design of the building. (A good representation of this opportunity for facility managers was drawn by CABE — Commission for Architecture and the Built Environment — in the book Creating Excellent Buildings; see accompanying diagram.)
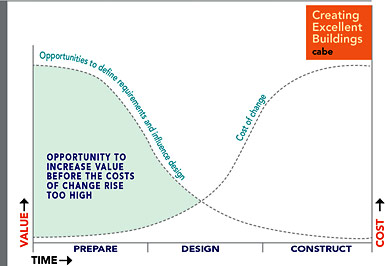
For use in FM- related processes, BIM provides two important characteristics: the bill-of-materials and the geometry of the building and its related assets. It is the geometry that can add specific value to facility management operations. The most tangible advantage is probably the use of the 3D geometrical model in maintaining the building and its assets as installed.
By using BIM viewers, professionals can assess aspects like the impacts and access prior to executing the work using the BIM. Questions like, “What happens when I close this water valve? Where will tabs or systems be cut off?” can easily and safely be assessed when preparing the actual work to be done. Likewise, the need for special tools can be established, and hazardous situations can be anticipated as well. In support of these types of use cases, we see adoption of various BIM model viewers among CAFM/IWMS vendors.
Reconstructions, FM projects — A typical life cycle of a building is made up of a number of rebuilds during its use. In general, we see rebuilds occur to adapt the building to new types of use or to bring it up to modern standards. As in the initial design and construction stages, these reconstruction projects are quite suited to be BIM projects. The same principles, strengths, and benefits of BIM processes apply here: collaboration, early detection, and lean logistics.
With a well maintained BIM at hand, these types of projects can run easier, faster, and cheaper. Using BIM systems and processes for reconstruction represents a significant opportunity for financial return on investment. The key here is to develop the BIM processes needed to execute them and engage the suppliers involved with them.
The consequence of reconstruction projects is that new versions of the BIM model emerge, describing the building in its new quality. Typically, a new BIM model version will show different geometries next to alterations of (part of) the bill-of-materials.
Pitfalls to Avoid
One could argue that BIM models may become the “digital twins” of the physical buildings in future: the models that describe not only geometry and bill-of-materials but also depict the actual condition and state of all its assets. The key prerequisite to effectively use BIM models in the future is that they are well integrated into the information infrastructure as well as connected to the FM operating processes.
In short: BIM adoption for facility management is primarily an information management exercise. So, what challenges lie ahead when considering to include BIM in FM operations?
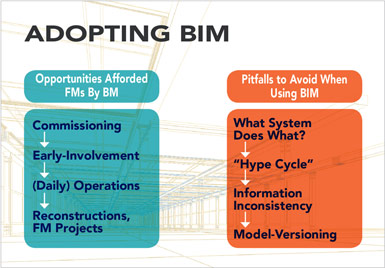
What system does what? — The world-leading IT watcher Gartner often uses its “hype cycle” approach to describe the state of adoption of technologies. Typically, every new technology goes through the stages of the hype cycle, meaning that in its early stages — the “peak of inflated expectations” — we expect too much too soon. Over time, not only do the technologies improve, but also the way in which users deal with them changes.
Facility managers should be aware of this principle in relation to BIM inclusion for FM. This starts with the view of what BIM can do. BIM systems are great for modeling and supporting processes of design and construction. They do not, however, offer the typical capabilities that CAFM/IWMS systems provide in terms of financial support (budget formation and depletion) and demand management (supplier management, work order management, and so on). This implies that BIM adoption calls for a well-designed integration approach between BIM systems and the CAFM/IWMS type of business systems. “I can do all my FM operation from the BIM” is probably a statement that reflects an elevated expectation toward BIM capabilities regarding FM operations.
On the other side, we will not see CAFM/IWMS systems altering the geometry of buildings in BIM models directly. In this domain BIM systems show great strength. Moreover, changing building geometry is a privileged function. Typically (construction) engineers can do that in a reliable and safe way. (Re)designing buildings is not a typical FM job. This is why CAFM/IWMS suppliers generally rely on BIM systems to do that type of work.
BIM systems are not merely producing a model of a building, but also providing a platform for real-time collaboration, logistics, and quality management. Information consistency — BIM models can be seen as databases on their own: data describing the geometry as well as data describing the bill-of-materials of the building in alphanumeric ways. Many FM-related procedures inherently alter data related to the bill-of-materials. Predominantly maintenance activities are involved where sometime replacements of existing assets are performed. When these types of activities take place, and the data is represented in the BIM model as well, then a process of data synchronization has to be in place.
Note that these processes can be initiated in many ways, not necessarily involving BIM. For example, the temperature in a certain space is too low, so the occupant puts in a complaint to the FM department. Typically, these types of complaints are registered in the CAFM/IWMS system to be followed up from there. The incident is dispatched to one of the facility’s maintenance engineers, who analyzes the problem and finds out that the root cause is a failing pump. The existing pump is replaced by a similar one, but of a different make: the Siemens pump is replaced by a Hitachi model with the same specifications. On completion of the job, the data is probably altered in the CAFM/IWMS system but not represented in the BIM model if we do not arrange for that to happen.
If we leave data to diversify over time between the BIM model and the CAFM/IWMS, the inconsistency between them will be quite harmful: “What is the truth? Which system describes the actual situation?” Restoring a source of truth can be quite tedious, difficult, time-consuming, and expensive. It is clear that one should never be found in this situation.
The consequence of this is that one needs two-way data synchronizations. In processes where the initial change takes place in the BIM (during reconstructions, for instance), the altered data has to be shared with the CAFM/IWMS system. In processes where the CAFM/IWMS takes the lead, the altered data has to flow into the BIM. This way we create a single source of truth, which will save time and money. There are numerous ways to implement data exchange, e.g., web services, file transfer, etc. Typically, CAFM/IWMS vendors will provide the means to implement.
Model versioning — As explained earlier, a building will typically go through a number of reconstructions during its life cycle. Every significant reconstruction typically involves remodeling of its geometry and changes to its bill-of-materials. In fact, a new version of the building model emerges. One will need a strategy to manage those versions to effectively use them for FM operations. In fact, over time, we will have multiple models that describe the building: one as it was in the past, another describing the building in its current state, and potentially another model describing the building in its future state.
For facility managers all these models are relevant. For example, in space management new spaces (dis)appear over time as result of reconstruction, impacting space footprint and space types. With that, cost profiles (leases) that the FM department is managing change over time. To effectively analyze future change or to understand cost profiles in the past, FM managers need to be able to connect to past, current, and future models. In fact, one needs to be able to “travel through time,” making sure that the BIM attached to each life cycle phase describes the building as it actually was at that time or how it will be in future.
Opportunity Is There
BIM holds real promise for facility management. The technology is available today and adoption has started. Some governments do require BIM to be used currently or in the near future for construction projects, so the number of BIM models available will grow quickly.
In other words, the opportunity is there. At the same time, facility managers are advised to approach BIM adoption as an information management exercise. Start small whenever possible and prioritize: think about the biggest problem to address first or the most appealing opportunity to materialize. Seek collaboration with the local IT staff and information management. When you do, the chances of success will rise exponentially.