The Early Days of ADA
When the act was passed in 1990, the focus, for the most part, was on accessibility to public spaces such as schools, stores, churches, civic buildings, and the like. But, because this was now federal legislation, the act applied to ALL types of buildings, including industrial facilities. The first reaction from most industrial building owners and designers was, “So what does this mean for us?” Designers and owners had to quickly get up to speed on how to interpret the guidelines for the types of facilities they worked with, which have vastly different needs and challenges than do more public spaces.
In those early days, the employers that took the most immediate action were those particularly concerned with being seen as considerate employers and community advocates. Those companies wanted to ensure employees, clients, and visitors alike had access and were comfortable in their facilities. But many industrial facility owners were hesitant to invest in upgrades, deciding instead to simply reassign employees with a disability to another role rather than adapt the space for them. As disabled employees and the legal community became savvier about the laws, however, that type of decision began to introduce concerns of parity and discrimination. So, owners began to make some smaller accommodations, primarily geared toward wheelchair users, such as ramps, wheelchair lifts, and wider clearances in places like bathrooms, entries, and common areas.
As time passed, even those accommodations began to draw criticism as they set disabled people apart from the rest of the community. In other words, if a group was moving from one floor to another, the wheelchair-bound employee would need to go to a wheelchair lift rather than toward the stairwell with the group, therefore setting him apart. Instead, the preference began to move toward ramps or elevators directly next to the stairs so that disabled employees maintained a sense of equality with non-disabled staff.
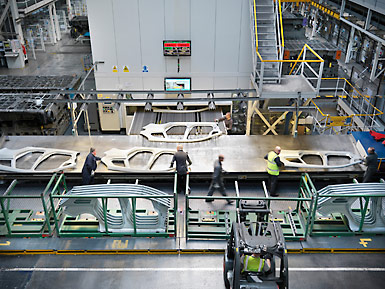
The changes industrial facility owners have implemented to respond to ADA over time have certainly evolved as everyone — from owners and designers to disabled employees and enforcement authorities — became more educated and understanding of the spirit of the act. Owners — who once said “We don’t need to make any changes since we don’t have any disabled employees” — realized the responsibility they had to address the needs of visitors, such as an electrical inspector, as well as future employees.
They also learned that the guidelines provided some practical flexibility. For instance, while the egress stairs in an industrial facility must comply with ADA, the stairwells leading to a maintenance platform may not. For smaller businesses that simply could not afford ADA upgrades, authorities were accepting of changes that provided reasonable accommodations, such as curbside delivery at a dry cleaning business.
With growing attention on ADA compliance, consultants began developing ADA master plans for larger facilities and industrial campuses. These master plans assess the entire building or campus’s accessibility and recommend alterations and improvements that would address any issues. In addition, master plans prove to ADA regulatory authorities that for areas where upgrades have not yet been made, there is a plan and schedule for implementing them over time. Some companies and institutions have gone so far as to hire their own ADA specialists, whose sole job is to ensure all facilities meet ADA requirements. While this type of position is becoming more common now at universities and public entities, it’s not quite the norm for industrial companies yet. Industrial owners more often hire design consultants to manage their ADA compliance as part of the facility design.
Another avenue owners and designers have negotiated since the 1990 passing of the act is the variety of guidelines that fall under ADA. Each jurisdiction can adopt the standards of its choosing, whether those are the federal, state, or municipally mandated guidelines. What’s more, the authority having jurisdiction (AHJ) over a building or site can vary by location. Pennsylvania, for example, has its own department focused on ADA compliance. In other locations, the state may defer to federal authorities, the county, or another local entity. There are currently movements in the direction of unifying the various versions of the accessibility guidelines into one common national or international guideline. This would streamline the process and clarify individual interpretations of the intent.
The changes industrial facility owners have implemented to respond to ADA over time have certainly evolved as everyone — from owners and designers to disabled employees and enforcement authorities — became more educated and understanding of the spirit of the act. 25 Years Later
Today, the education that time and experience have provided has made an enormous impact on accessibility at all types of sites. From those early days of attention on wheelchair-bound employees, companies now have realized that a multitude of disabilities are included within the guidelines, such as hearing and sight impairments. So, for example, while an elevator helps people with wheelchairs or crutches reach another floor, that elevator must also be accessible to those who are hearing or sight impaired, with a braille control system, audio notifications, etc. Similarly, fire alarms and other warning systems must include both an audible horn as well as flashing lights or other visual cues.
Engineers and designers have also learned how to best balance ADA requirements with the rest of the facility’s needs. Because the guidelines are often open to interpretation, designers rely on the commentary in building codes to help clarify the intention of the law’s literal wording. For example, to design an ADA-compliant bathroom stall, there should be adequate clear space adjacent to the toilet and opposite the entry door. This allows the person in a wheelchair to enter straight in through the door, close it, and then dismount onto the toilet. In a literal sense, that means the floor space opposite the door must be large and clear. However, the designer might find that the space is limited when renovating an existing bathroom, maybe only an inch short of the clearance requirements. The solution may be making the door oversized to allow reasonable clearances and providing a good-faith, best effort to meet the intent of the provision.
Advancements in equipment have also made it much easier to comply with ADA requirements. When ADA-compatible bathroom sinks first hit the market, they simply allowed those in wheelchairs to fit their knees under the sink. But when people began burning their legs on the exposed pipes, innovative manufacturers developed kits to place over those pipes to avoid contact with bare skin. Chemical fume hoods have also evolved to be lower and provide unobstructed access below the surface and for reaching research equipment and hardware.
Even if a facility is designed to meet ADA requirements, that doesn’t ensure it will be built exactly to the plans. In one real-life example, a new building had an ornamental staircase with glass panels and a top railing that was open to the floor below. An employee fell over the rail and was injured. The investigation determined that the handrail/guardrail system was one inch shorter than the requirements. The architect’s detail showed the correct measurement but the shop drawings did not, which made the ultimate difference. When these discrepancies come to light after a facility is built, it is much more costly to make the necessary changes for a safe and compliant facility. Facility owners are best served by making ADA compliance a priority for the entire project team, from design through construction.
Into the Next 25 Years
Ultimately, ADA compliance is largely acknowledged and accepted now as any owner or developer plans upgrades to existing facilities or to build brand new ones. Just as a building must accommodate lighting and heating systems, it must incorporate ADA needs. And as the entire building community has become more educated, it’s become much easier to comply. Designers now see their role as continuing to educate clients on what accommodations need to be made, but with that understanding, pushback is rare — a significant change from 25 years ago.
Undoubtedly ADA requirements and their scope will continue to evolve over the next 25 years. In fact, the latest edition of the guidelines has now been expanded to include more types of facilities, such as boat ramps and other outdoor recreation sites. As we all become more sensitive and accommodating to the needs of all others, the trend is to expend the additional effort and cost to do what is right and in the best interest of the community as a whole.