Due Diligence: Thoroughly Investigating the Technical Aspects of a Site
By carefully examining site conditions/logistics, environmental regulations/risk, as well as the area surrounding the chosen site, companies can avoid delays and cost overruns.
Q2 2018
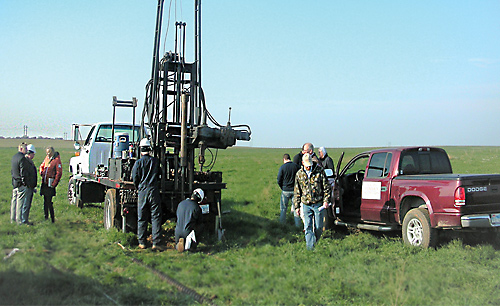
What To Evaluate
Many details come into play in determining the suitability of a site. Here is a sampling of things to consider:
Site conditions — It’s important to take into account geological and topographical conditions in the area to determine its suitability for an industrial facility. An ideal site will have well-graded, compacted soil with high soil-bearing pressure. For a greenfield manufacturing plant, the type of operation and equipment installed will affect the soil requirements. For example, a heavy load production plant constructed on a site with low soil-bearing capacity will require a deep foundation, increasing construction costs.
The evaluation should assess the level of the water table. A high water table creates drainage issues and makes construction more difficult, especially if the production requires pits. Other site characteristics that affect construction and operations include the size and shape of the parcel of land. The purchase of too much land will tie up capital, while a site that is too small can hinder growth of the company at that location. Will adjacent land be available for future expansion? Also take into account the shape of the land parcel, which can allow or prohibit the construction of additional buildings in the event of future expansion.
Environmental risk factors — An environmental assessment report is critical in order to check for factors that can complicate and delay construction or operations. It’s also wise to undertake an archaeological study as well as an endangered species analysis. Risk factors can be measured by assessing the site’s seismic zone, wind zone, rainfall intensity, and the presence of wetlands, streams, and flood areas. What is the likelihood of an earthquake, hurricane, tornado, and/or hailstorm? Are shelters required?
Nearby operations can also affect the site’s suitability. Check for contamination or pollution on or near the site. Is there fracking activity in the area? Are there heavy industries (e.g., chemical operations) close by? Is your production prone to salinity or radon?
Site logistics — For most companies, executing key business strategies and ensuring convenient travel require easy access to infrastructure. The location and its accessibility by air, rail (rail line, intermodal facility), sea (ocean port, barge), and/or major highway will affect the ease and cost of the way raw materials are brought in and finished products/materials distributed.
For ground transportation, check roads to determine if they can accommodate the required truck traffic and loads. If construction will require the transportation of large equipment pieces, logistics and accessibility are particularly important to review during the site selection process rather than at a later stage. Additional elements such as the height of bridges, width of roads, and necessity of coordinating with the Department of Transportation may come into play.
Utilities — Take into account the demand, cost, quality, and reliability of basic utilities. Their impact can be lasting, as these costs can represent a significant portion of annual operating expenses. Factor electric power, natural gas, fiber optics, water, and sewer services into the decision-making process. Look at the cost of starting up these services as well as recurring costs. Consider the potential need for expanded capacity with future growth of the company at the site.
The location and its accessibility by air, rail (rail line, intermodal facility), sea (ocean port, barge), and/or major highway will affect the ease and cost of the way raw materials are brought in and finished products/materials distributed. Permitting and regulatory environment — Regulations vary by city/county/state. Take into account zoning regulations, as well as the ease/difficulty of and lead time needed for various permitting processes.
Check regulations applying to design and land use. Are there building height restrictions or covenants in place? Federal Aviation Administration (FAA) restrictions? What planning and operating permits are required? What operating licenses are necessary? Are there any limitations on the plant’s hours of operation?
Other challenges — How many current owners does the site have? When there are a large number of private owners, immediate availability is unlikely and protracted delays can derail the process. Are there any existing liens on the site? Do easements and/or underground utility lines cross the site?
Where Things Can Go Wrong
When the due diligence process falls short, costly headaches are likely to result. Here are two examples of inadequate research and planning:
Example 1 — An international automaker opening a U.S. plant secured a site and developed a plan and project timeline. Its first site glitch occurred during construction — the discovery of a blue-line stream that had to be relocated and rerouted. The next obstruction — bulldozers encountered a rock bed that had to be blasted out of the way. The final blow was the discovery that the site was home to an endangered species — a turtle family that also had to be relocated.
Example 2 — A company selected a site that was “certified” through a program that provided detailed information about factors such as utilities, access, environmental concerns, and potential development costs. Though the program assessed the risks associated with development generally, project-specific information was not gathered. In addition, only 300 of the 450 acres the company selected had been certified, and the remaining 150 acres were not assessed.
An efficient due diligence process and successful site selection often require the input of a qualified site selection expert with deep knowledge of engineering principles, building codes, permitting requirements, and regional characteristics that affect operations. During the design phase it became apparent that the site’s close proximity to an airport would present a major problem. While the flight path had been checked during site selection, the certification did not apply to or provide information about the approach and proximity to the airport’s systems and controls. The FAA took action due to concern about the heights of buildings and structures as well as the risk that a highly automated production would interfere with the airport’s technical system. It ultimately requested a review of every building and structure, including stacks and the substation. This type of review can cause extensive delays, as it can take up to nine months if questions and clarifications are requested.
Certifications are often misunderstood. While they may be useful in the gathering of general reports, studies, and utility information, they frequently fail to uncover project-specific risks such as those presented by the nearby airport in this example.
Consult An Expert
To avoid the types of difficulties outlined herein, make sure to conduct the appropriate studies of the site and its environment. Following are among the things on an engineer’s checklist: identifying wetlands, streams, and flood areas; testing soil composition; investigating the presence of endangered species and archaeological findings; evaluating weather conditions; and studying the site’s access by road, sea, air, and rail.
An efficient due diligence process and successful site selection often require the input of a qualified site selection expert with deep knowledge of engineering principles, building codes, permitting requirements, and regional characteristics that affect operations. There is no shortage of businesses claiming to offer these services. But note that it’s best to hire someone with the client’s best interests at heart, rather than someone chasing a sales commission. An experienced consulting engineer will ensure no issue is overlooked and efficiently manage the process. This will help the company minimize headaches, delays, and cost overruns.
Project Announcements
MerryGoRound Plans Pittsylvania County, Virginia, Fulfillment Operations
08/14/2025
Hartman Cabinetry Plans Jonesburg, Missouri, Operations
08/14/2025
eBliss Global Plans Utica, New York, Manufacturing Operations
08/14/2025
QTS Data Centers Plans Cedar Rapids, Iowa, Operations
08/14/2025
AbbVie Expands North Chicago, Illinois, Production Operations
08/13/2025
Land ‘N’ Sea Distributing Expands Norfolk, Virginia, Operations
08/13/2025
Most Read
-
20th Annual Area Development Gold and Silver Shovel Awards
Q2 2025
-
What We’re Getting Wrong About Gen Z’s Future in the Skilled Trades
Q3 2025
-
A New Course for U.S. Shipbuilding
Q3 2025
-
Optimizing Your Rail-Served Transportation Network: Strategy Before Steel
Q2 2025
-
In Focus: AI Is Changing Incentives Math
Q2 2025
-
How to Choose the Right Site for Your Factory in 2025’s Volatile Landscape
Q2 2025
-
Reshoring Reality Check from Construction
Q3 2025