The evaluation of a site, phasing, and constructability used to take a project team six to eight weeks…and even then, results were dubious. Because there’s no one-size-fits-all solution to plant design, dissimilar facilities were relied upon to inform ”order of magnitude” estimates, with rough sketches and assumptions being used as the basis for decision-making. Now, however, improved software tools and new workflows, when combined with relevant historical cost data, enable evaluations to be accomplished in a matter of hours, and with greater accuracy. Building information modeling (BIM), in particular, has expanded beyond its original role. Once used primarily within traditional design-phase boundaries, BIM can now be used during front-end planning.
Programs have been developed that allow for quick conceptual model development, or “macro” modeling. These programs focus on construction site requirements and large-scale building massing. They act as a catalyst during early project meetings, allowing the industrial owner and project team to create custom facility models and building elements, addressing such factors as production and process equipment, utility loads, transportation requirements and their impact on site selection, regional construction costs, project schedule, budget, site balancing, and more. Having so much information instantly available allows the team to collaborate, evaluate alternatives, and make informed decisions very quickly.
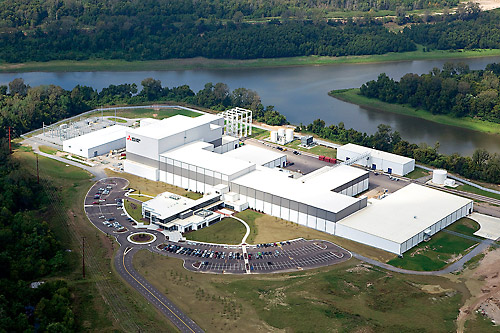
By working with design-build firms or consultants who have leading interactive BIM software — and who have customized its pre-set formulas and data sets (especially historical cost data) with information that is closely tailored to specific project situations — owners can reduce risk and improve on predictability on projects. Parameters can be changed on the fly, and cost estimates on energy, lifecycle, topography/grading, and scheduling/sequencing are then updated in real time. The design-estimate cycle can be reduced significantly. Decision-making is enhanced when owners and team members are engaged in the transformation of a model as its footprint, building material type, massing, siting, and more are adjusted. Each manufacturing project is unique and has specific facility requirements. Various alternatives and “what-if” scenarios can be quickly and accurately compared.
Project Examples
In a recent project planning session, a European client was able to meet with a planning team who helped assess which of six potential sites in the U.S. would likely have the least construction cost based on the specific needs of that factory. During a two-hour interview session, initial costs were established for the facility on the favored site. The site plan was optimized considering cut and fill analysis and the location of major utilities that were known at the time. The macro-BIM model developed for this site, along with its base costs, were then used as a benchmark to factor the likely costs for the five other sites. Exploration of these sites demonstrated that as prospective regions change, the engineering responses to critical factory needs also change. Within a few days, the team was able to adjust the model to provide estimates for varying site-specific construction costs such as tighter humidity control, deeper foundations, higher seismic zones, and labor market costs. The client walked away with an optimized site development plan and cost estimate for their favored site, plus five other scenarios for building the same building in different regions.
If project variables have been controlled and modeled before construction commences, this reduces the number of things that can go wrong once work is under way. During another recent project planning session, designers, estimators, and client were able to consider together the feasibility of a high-bay automated warehouse over a traditional, larger footprint, rack warehouse to store their alcoholic beverages on an existing factory site. After a few hours of work, the options were fleshed out in a model that everyone could see and costs were compiled to help judge feasibility. Analysis of several optional scenarios was part of the model development (e.g., different claddings for the differing building heights, differing foundations, and the impact of finish floor elevation). The analysis showed that the automated warehouse would be able to have a lower finish floor than the traditional warehouse due to the way conveyors retrieve product. Additionally, the costs of imported dirt fill in this particular project were able to be reduced to offset the larger foundations required by the high bay. The high bay was recognized to be more feasible than originally thought and it was eventually adopted as the plan.
Macro-BIM can also be used to determine project feasibility before capital is committed to a project, as part of the capital appropriation process. A 3D visual preliminary design gives form to a project, which is particularly important in light of the fact that studies show most people can’t look at 2D drawings and translate them into 3D visual information. The number of engaged reviewers drops even further when the information being presented takes the form of detailed cost estimates and scope clarification documents. Yet, informed decisions can only be made if all major stakeholders can visualize an end product and understand exactly what is included in the budget.
Overall, the industry is seeking to reduce guesswork and project risk, as well as improve information flow when it comes to major decisions and large monetary commitments. Economic development officers can also derive value from BIM by providing virtual spec industrial spaces for their communities. 3D models provide something to show to site consultants, prospects, management, and community members, at a fraction of the cost of a speculative industrial facility. Macro-BIM software not only provides a virtual spec building but also a preliminary schedule and cost, taking participants’ understanding beyond 3D and into 4D analysis.
Harmonizing with New Project Delivery Methods
Macro-BIM has grown not as a stand-alone technology platform, but as part of the architecture/engineering/construction industry’s larger trend of adopting new project delivery methods. For example, lean project delivery has sought to optimize results and reduce waste, with particular focus on business, design, and production practices. Integrated project delivery has had similar efficiency goals but with an emphasis on collaboration and the early involvement of a project’s key stakeholders. Target value design, a form of value engineering, reverses the traditional procedure of estimating costs based on a finished design, and instead uses estimated costs and constructability considerations to formulate the design. Design-bid-build project delivery has given way to design-build. Even the traditional construction contract environment has been disrupted, as alternative models — ones that distribute risk and promote collaboration — have been created.
Overall, the industry is seeking to reduce guesswork and project risk, as well as improve information flow when it comes to major decisions and large monetary commitments. This has created a demand for more reliable data early in project planning. Technology developments that combine data sets with modeling in order to quickly run sophisticated scenarios bring big benefits to contemporary project delivery.
Downstream Advantages
It’s clear that improving decision-making at project outset is advantageous. But macro-BIM models created during preconstruction can be built upon and utilized as a basis of design during subsequent phases of project development, thus benefiting the design, procurement, and construction processes.
Use of macro-BIM during preconstruction also leads to lower risk and improved predictability during the construction phase. Project risk takes many forms, including the loss of profit due to cost or schedule overruns or excessive changes. If project variables have been controlled and modeled before construction commences, this reduces the number of things that can go wrong once work is under way.
Macro-BIM solutions take a holistic view of a project. Having a preliminary design that is fully represented in 3D form gives shape to a project, improves collaboration and understandings, allows cost and feasibility to be established within hours, and, most importantly, improves project success.