The U.S. has become the cheapest place in the world to make plastics, as one of the benefits of the fracking technology that has created a surplus of natural gas, the primary ingredient for making most plastics. To build on this competitive advantage, chemical producers have invested a record $185 billion to build new capacity in the U.S., according to the American Chemistry Council (ACC), an industry group.
Expansion/New Investment
“Many plastics companies are betting on the continued, future growth in the industry, which has generated a great deal of expansion and new investment,” Perc Pineda, chief economist of the Plastics Industry Association told Area Development.
Much of the expansion is taking place along the Texas Gulf Coast, which continues to be a mecca for plastics manufacturers and those who supply the industry. Dow, Exxon Mobil Corp., and Chevron Phillips Chemical Co. are building multibillion-dollar factories along the Texas coast. The plants are part of $185 billion in proposed and recently completed investments, according to the ACC.
One of the biggest Gulf Coast projects is a joint venture between ExxonMobil and Saudi Basic Industries Corp. (SABIC), a company owned by the government of Saudi Arabia. The partners are investing $10 billion in what will be the world’s largest steam cracker plant at a massive petrochemical complex just north of Corpus Christi. Access to natural gas from the Eagle Ford Shale was the key factor in locating the plant, which will become operational in 2021, making ethylene and other chemicals used to make polyester, anti-freeze, plastic bottles, and food packaging products.
The plant will be capable of producing 1.8 million metric tons per year of ethylene that would feed a monoethylene glycol plant and two polyethylene plants. Manipulation of these molecules currently is used in a number of practical applications, including the manufacture of hybrid plastics and ceramics that are scratch-resistant, lighter, and much stronger than steel.
In Baton Rouge, La., Lotte Chemical USA is investing in a $1.9 billion joint venture with Westlake Chemical to build an monoethylene plant on a 250-acre site that will also serve as a future headquarters. More than $3 billion in new capital investment is expected to translate into 265 new direct jobs, and more than 2,300 new indirect jobs in Lake Charles and surrounding areas.
Almost 20 factories are being built or expanded to convert gas to liquids such as ethane and propane into ethylene, the most used petrochemical and the main ingredient in polyethylene plastic. However, South Africa’s Sasol Ltd. has abandoned plans for a gas-to-liquids plant in the Lake Charles, La., area that would have cost as much as $15 billion and employed 750, saying the low price of oil and a volatile marketplace make the project “uneconomic,” according to the Lake Charles Advocate. Meanwhile, Sasol is going ahead with an $11 billion ethane cracker complex being built near Lake Charles, La., which is scheduled to begin producing polyethylene next year.
Formosa Plastics Corp. USA is making a massive investment in the coastal town of Point Comfort, Texas, building two polyethylene plants and a polypropylene plant. ICIS, a market information service, has reported that the polyethylene plants, each with a 400,000 ton per year capacity, should start up in the second half of this year. Formosa is also building a 1.2m ton/year ethylene cracker at Point Comfort, as well as a 600,000 ton/year propane dehydrogenation (PDH) unit. The PDH unit could start production in 2020 or 2021, ICIS says.
Plastics Industry on Track to Grow
Fracking technology that has created a surplus of natural gas, the primary ingredient for making most plastics, has resulted in a great deal of investment in new and expanded facilities, with chemical producers investing a record $185 billion.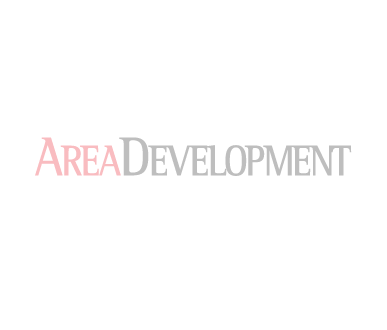
-
Dow
Freeport, TXDow Chemical started up its ethylene and plastics complex in Freeport, Texas, at the end of 2017; the company’s Gulf Coast Investment Program began more than five years ago with a series of comprehensive investments in projects designed to take advantage of low-cost shale gas feedstock.
-
Chevron Phillips Chemical Co.
Woodlands, TXWoodlands, Texas-based Chevron Phillips Chemical Co. has put its ethane cracker, which is located at its Cedar Bayou facility in Baytown, to work; it represents the final phase of its $6 billion Gulf Coast petrochemicals project that was announced in 2011.
-
ExxonMobil and Saudi Basic Industries Corp. (SABIC)
Corpus Christi, TXExxonMobil and Saudi Basic Industries Corp. (SABIC) are investing $10 billion in what will be the world’s largest steam cracker plant at a massive petrochemical complex just north of Corpus Christi, which will make ethylene and other chemicals used to make polyester, anti-freeze, plastic bottles, and food packaging products.
-
Lotte Chemical USA and Westlake Chemical
Lake Charles, LAIn Baton Rouge, La., Lotte Chemical USA is investing in a $1.9 billion joint venture with Westlake Chemical to build an monoethylene plant on a 250-acre site that will also serve as a future headquarters.
-
Sasol Ltd.
Lake Charles, LASasol is going ahead with an $11 billion ethane cracker complex being built near Lake Charles, La., which is scheduled to begin producing polyethylene next year.
-
Formosa Plastics Corp. USA
Point Comfort, TXFormosa Plastics Corp. USA is making a massive investment in the coastal town of Port Comfort, Texas, building two polyethylene plants and a polypropylene plant. Formosa is also building a 1.2m ton/year ethylene cracker at Point Comfort, as well as a 600,000 ton/year propane dehydrogenation (PDH) unit.
-
Royal Dutch Shell Plc
Pittsburgh, PARoyal Dutch Shell Plc, the U.K. oil and chemicals conglomerate, has started building an ethylene complex outside Pittsburgh that will begin production in the early 2020s. It will produce plastic pellets, which end-users will turn into products such as packaging, trash bags, and bottles.
-
Shell Chemical Appalachia
Marshall Township, PAIn Monaca, 25 miles northwest of Pittsburgh, Shell Chemical Appalachia is building a petrochemical plant that will produce ethylene and polyethylene, employing 600 workers.
-
Central Plastics
McPherson County, KSCentral Plastics has expanded to 210,000 square feet at its in McPherson County, Kansas, location there and employs more than 200 people, with another expansion planned.
-
Wright Plastic Products Co. LLC
St Clair, MIIn St. Clair, Mich., a $3.3 million expansion project is in the works for Wright Plastic Products Co. LLC, a major supplier to the automotive, recreational, and marine vehicle markets.
-
Plastic Trim International
East Tawas, MIPlastic Trim International is investing $16.1 million in a 42,000-square-foot expansion and technology upgrade at its Baldwin Township manufacturing plant and its logistics center in Tawas City, on the shore of Lake Huron.
-
20/20 Custom Molded Plastics
Bluffton, IN20/20 Custom Molded Plastics, a custom structural form-molding manufacturer, plans to locate a new facility in Bluffton, Ind. The company will invest more than $27 million to purchase and equip Buckhorn Inc.’s former 170,000-square-foot facility and plans to hire many of its workers, ultimately creating up to 155 jobs by 2020.
-
Berry Plastics Group, Inc.
Phillipsburg, NJEvansville, Ind.-based Berry Plastics Group, Inc. has added 150,000 square feet and an on-site quality lab to its Phillipsburg, N.J., facility. The expansion will help serve its growing healthcare and personal care packaging market.
-
Oji Intertech, Inc.
North Manchester, INProximity to automakers has been profitable for Oji Intertech, Inc., a Japanese-owned automotive and industrial packaging company, which plans to expand its operations in North Manchester, Ind. The company will invest $4.5 million to double its 80,000-square-foot facility.
Pennsylvania is the second-largest U.S. producer of natural gas, expected to produce 40 percent of U.S. natural gas by 2030. And, Central Pennsylvania is home to one of the largest coal-to-natural gas power plant conversion projects in the U.S. — a $1 billion, 1,124-megawatt plant along the Susquehanna River in Snyder County, on the site of a shuttered, coal-burning power plant. Beginning this year, it is expected to power one million homes in the Northeast and Mid-Atlantic.
Royal Dutch Shell Plc, the U.K. oil and chemicals conglomerate, has started building an ethylene complex outside Pittsburgh that will begin production in the early 2020s. It will produce plastic pellets, which end-users will turn into products such as packaging, trash bags, and bottles.
In Monaca, 25 miles northwest of Pittsburgh, Shell Chemical Appalachia is building a petrochemical plant that will produce ethylene and polyethylene, employing 600 workers. It should be noted that more than 70 percent of North American polyethylene customers are within a 700-mile radius of Pittsburgh.
The Midwest has also attracted plastics manufacturers, albeit on a smaller scale than the Gulf Coast. Like the Pennsylvania-Ohio area, the Midwest also has a strong manufacturing legacy. “In a way, the Midwest cluster is expanding eastward to Pennsylvania,” says Pineda.
One Midwestern concentration is in McPherson County, Kansas, which has nine plastics manufacturers and eight plastic industry support facilities. Central Plastics has expanded to 210,000 square feet at its original location there and employs more than 200 people, with another expansion planned.
Imposing higher import duties on U.S. plastics companies changes the industry’s supply chain dynamics in a way that impacts both businesses in plastics and businesses that depend on or serve plastics. Perc Pineda, chief economist, Plastics Industry Association told Area Development In St. Clair, Mich., a $3.3 million expansion project is in the works for Wright Plastic Products Co. LLC, a major supplier to the automotive, recreational, and marine vehicle markets. And in Iosco County, Mich., Plastic Trim International is investing $16.1 million in a 42,000-square-foot expansion and technology upgrade at its Baldwin Township manufacturing plant and its logistics center in Tawas City, on the shore of Lake Huron.
Plastics manufacturers are also expanding in Indiana. 20/20 Custom Molded Plastics, a custom structural form-molding manufacturer, plans to locate a new facility in Bluffton, Ind. The company will move into the former home of Buckhorn Inc. and plans to hire many of its workers, ultimately creating up to 155 jobs by 2020. The Holiday City, Ohio-based company will invest more than $27 million to purchase and equip Buckhorn’s former 170,000-square-foot facility.
Evansville, Ind.-based Berry Plastics Group, Inc. has added 150,000 square feet and an on-site quality lab to its Phillipsburg, N.J., facility. The expansion will help serve its growing healthcare and personal care packaging market.
Another major consideration for plastics manufacturers seeking a new plant location is proximity to a vibrant market, Pineda says, since proximity to customers means lower shipping costs.
With that in mind, proximity to automakers has been profitable for Oji Intertech, Inc., a Japanese-owned automotive and industrial packaging company, which plans to expand its operations in North Manchester, Ind. The company, a subsidiary of Tokyo-headquartered Oji Interpack Co. Ltd., will invest $4.5 million to double its 80,000-square-foot facility.
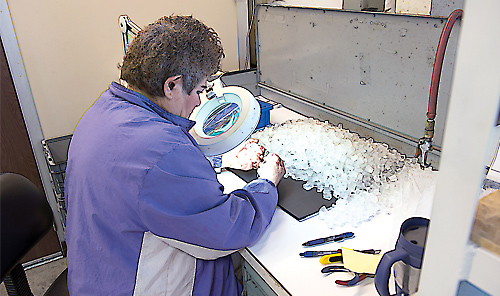
Along with new and expanded facilities, plastics manufacturers are also making sizable investments in processing equipment. For example, Canada-based IPL Plastics recently announced that it is spending $18.9 million in Forsyth, Ga., to add eight injection presses that will lower production costs with modernized technology. IPL, which makes sustainable packaging, is a 79-year old company that went public in June.
Packaging, in particular, is showing especially strong growth, according to Pineda, due to the growth of e-commerce. With the rapid growth of the middle class in Asia and elsewhere, the packaging sector should remain strong, he says. U.S. exports of polyethylene plastic to Asia will increase by more than five times by 2020, with China as the primary destination, according to research company IHS Markit Ltd.
The U.S. housing market is expected to stay in recovery mode, meaning the outlook for plastics materials in building and construction will remain stable. Nonresidential construction has also returned to pre-recession levels, meaning continuing plastics demand in that end market.
Automakers are another customer group that will continue to show strong growth for plastic-makers, says Jeff Forsythe, a Greenville, S.C.-based site selection consultant. “With automakers continuing to reduce the weight of the vehicles they make, lightweight plastics are going to continue to be maximized.” Across all sectors, “I don’t see any drawbacks to the continued growth of plastics, especially with natural gas costs being so low in the U.S. For the plastics industry, the only potentially negative trend on the horizon may be the developing, global trade war,” Forsythe adds.
“Tariffs will undoubtedly have an impact on the industry, which has global reach both upstream and downstream,” Pineda says. “Imposing higher import duties on U.S. plastics companies changes the industry’s supply chain dynamics in a way that impacts both businesses in plastics and businesses that depend on or serve plastics. Higher tariffs on plastic materials and products ultimately reduce the industry’s competitive advantage internationally, and so it is in the best interest of the plastics industry, and the U.S. economy as a whole, that plastics trade is allowed to flourish.”