The tune is not exactly the same when non-U.S. companies seek American locations. Labor factors are not typically the primary drivers of foreign direct investment in the United States, admits Robert Hess, executive managing director of consulting with Newmark Grubb Knight Frank Global Corporate Services. “They’re coming for market access. They’re coming here because they have to come here.”
“Companies are coming here because their market is substantially here,” agrees W. Lee Thuston, managing partner with Burr Forman and a veteran of foreign direct investment deals in the southeastern part of the United States. “It’s the primary driving force.”
Global players quickly find out that organized labor in the United States is quite a different thing than can be found elsewhere.
“They see opportunities here in the States,” adds Dr. David Lewin, managing director and head of the Labor and Employment practice at Berkeley Research Group. “Otherwise it might not make sense to do foreign direct investment.”
Labor Due Diligence
That said, even though the cost of labor might have been enough of a concern to shift jobs away from the U.S. in past years, labor issues need not be a barrier to success for international companies planning American operations. There are, in fact, labor advantages that go hand-in-hand with U.S. locations. But it’s critical that global companies really do their homework as they search for sites. The U.S. labor situation can be vastly different from what’s the norm in other countries, and some traditional ways of thinking aren’t always the most suitable options anymore.
For example, in the past, it has often made sense for companies to seek locations in the proximity of other companies with similar operations. Seeking clusters of likeminded employers certainly seems like a reasonable approach from a labor perspective, because such locations already are home to many qualified workers, but the “herding effect” can be dangerous.
Why? These days there can be too much competition. “People in the U.S. have choices again,” Hess says. Job growth continues to recover following the Great Recession, which means job-seekers have increasing options and they’re more willing to look around for better situations. According to the U.S. Bureau of Labor Statistics, the unemployment rate in February was down to 5.5 percent nationally, more than a full percentage point below what it was a year earlier. Sector clusters have many advantages, but as the employment situation improves, the competition for labor can be increasingly troublesome.
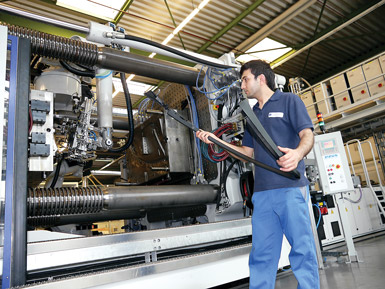
Obviously, finding a “best-kept secret” kind of location isn’t the best option for everyone. Still, with careful research and a firm understanding of U.S. labor markets, regulations, and training opportunities, finding an adequate supply of skilled labor is eminently doable. “Virtually all of the companies we’ve worked with here have not had trouble getting fresh labor as long as they can train them,” says Marcel Debruge, partner with Burr Forman.
Unionization and Right-to-Work Laws
That understanding begins with the acknowledgment that the United States is a collection of 50 states, with widely varying characteristics and regulatory environments. That’s not a bad thing, of course, because global site selectors have just as widely varying requirements. Consider the subject of unionization. “Some want to have an open shop, some like to have unions, and some are neutral and have to bring that neutrality here,” Thuston says.
Global players quickly find out that organized labor in the United States is quite a different thing than can be found elsewhere. As Lewin points out, such concepts as work councils and co-determination are a way of life in many European locations, but “we don’t have co-determination and we don’t have work councils.”
In fact, he points out, the U.S. doesn’t have nearly as many unionized workers as it used to. “If you’re coming into the U.S., you’re coming into a country with one of the lowest private-sector unionization rates in the world,” he says. As of 2014, the private-sector unionization rate was 6.6 percent, according to the U.S. Bureau of Labor Statistics, and the overall rate including both public- and private-sector employment was 11.1 percent.
That’s a far cry lower than it was as recently as the 1980s, when the waves of international auto manufacturing operations were beginning to hit American shores. “When they first started coming to the U.S., the unionization rate was on the order of 25 percent, and in the auto industry it was considerably higher,” Lewin says. “Now almost 94 percent of the private-sector workforce is nonunion.”
For companies that would prefer to avoid unionization, that would seem to simplify matters; but, in a way, says Lewin, it makes it all the more important to really pay attention to labor laws and regulations, which apply whether or not a union is in the picture. There are federal laws that are in force universally across U.S. sites, but there are also 50 sets of state laws governing selection, hiring, promotion, and a host of other labor topics, he observes. “There are a lot of specific things that you shouldn’t do and some specific things that you should do,” he says.
Among the differences between states is the concept of “right-to-work.” In many states, unions and employers may require all workers at a unionized facility to help pay for the collective bargaining and representation services provided by the union — union members and nonunion members alike. The rationale is that all workers, even those who have chosen not to join the union, benefit from the presence of the union.
About half the states, however, have enacted “right-to-work” laws that prohibit compulsory fees for nonunion members. In general, the “right-to-work” concept is most prevalent in the South, but as Debruge points out, “Wisconsin has recently become right-to-work, and Indiana and Michigan have become right-to-work.”
“Right-to-work” laws tend to drive down unionization rates, which may in turn lead to lower wage rates. Be that as it may, cheaper labor isn’t everything, he says. “What companies are looking for is not necessarily the lowest labor cost, but dependability and the capability of delivering quality.”
Lewin adds that while many companies — including many of the non-U.S. automakers that have sought U.S. sites in recent years — instinctively seek to avoid unionization, others feel less threatened by organized labor. “You can run a unionized operation and do very well in business. In some industries the highest-performing companies are highly unionized.”
Training Resources
The ability of workers to deliver quality has a lot to do with training. Resources supporting training can vary significantly from one U.S. site to another. Community colleges have opportunities that range from scheduled coursework to customized programs tailor-made for individual companies. “I think a lot of foreign companies don’t realize how these [programs] can supply them with competitive advantages,” says Hess, who adds that there’s “great diversity in the quality from one place to another.”
Many global companies will bring seasoned staff to new U.S. sites to lead training efforts, at least at the beginning. Such efforts may be combined with community college resources and training-focused incentives from state governments. Thuston points out that site selectors must determine how much money states are going to give companies for training. “You’ve got to have the money and capability to do a massive amount of training,” he explains.
That piece of the labor puzzle is big, and it has the attention of site selection consultants and economic development agencies across the U.S., according to Thuston. “The number-one issue is workforce development,” he says. “You’re got to have a basic level of understanding to train to make cars or aircraft or whatever you’re making.”
Even after a site is chosen, global players would be wise to choose human-resources leaders who are completely familiar with hiring and operating in U.S. locations, Thuston says. Upper management in a U.S. outpost may move in from the home country, along with many of those involved in finance and the initial rounds of training. But as for HR, he says, “You have to hire experienced Americans who understand training and benefits and work performance.” Debruge concurs: “They need to find the right local management that’s going to be able to select and hire.”
Competitive Wage Rates
Overall, non-U.S. companies are finding their way to U.S. sites in increasing numbers. The World Investment Report 2014 from the United Nations Conference on Trade and Development found that foreign direct investment in 2013 was up 10 percent globally over the year before, but was 17 percent higher in the United States. Foreign companies made $188 billion in U.S. investments in 2013. Among greenfield investments, the biggest U.S. recipients were California and Texas, according to the report.
Lewin points out that the international companies making these investments are finding wage rates are more competitive now than they have been in recent years. Those better labor deals that U.S. companies found elsewhere in the past are, in many cases, no longer what they used to be. “In 1960, my recollection is that Japanese manufacturing wages in relation to the U.S. were about 10 cents on the dollar,” he says. These days the rates are practically neck-and-neck, according to the Bureau of Labor Statistics. Manufacturing wages in Mexico remain lower, but the gap is narrowing, Lewin says.
Meanwhile, manufacturing wages are higher across much of Europe than they are in the United States, according to the Bureau of Labor Statistics, and the difference has increased in a number of locations. It would seem that those labor-cost arguments that in the past were part of the equation for moving jobs away from America are diminishing, and in some cases vanishing entirely.
Debruge adds that the international companies choosing U.S. locations are finding eager workers ready to join their labor force. “I’m in these plants all the time, and people are glad to have these jobs,” he says. “People want to learn, and they want to be part of a company that’s successful. There’s a lot of enthusiasm.”