Fixing the Supply Chain with AI and Robotics
Automation, industrial robots, and other technology solutions have allowed manufacturers to shorten their supply chains, while also making them more efficient and reducing labor costs.
Q4 2022
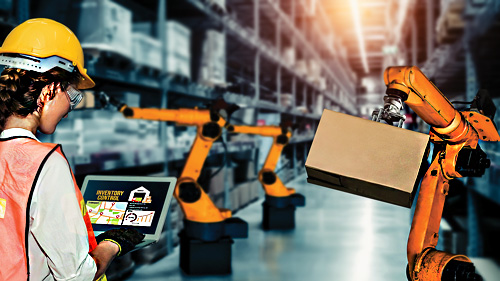
“With COVID, the level of volatility in supply chains rose to a level that was unprecedented and caught a lot of people by surprise — and not in a very good position,” says Claudio Knizek, global leader of Advanced Manufacturing and Mobility at EY-Parthenon. “There’s always been interest and appetite to understand and predict the supply chain, but now more than ever many companies are looking for technologies and software to predict supply chain issues before they happen.”
Technology solutions range from an ever-increasing use of industrial robots to tapping into more powerful uses of data, artificial intelligence, and machine learning to gain effective insights. Organizations are looking for new ways to run their manufacturing and distribution operations with fewer people, while making more prescient decisions that can help avert shortages.
Adding Automation to the Supply Chain
The digital technology conglomerate ABB surveyed hundreds of American and European business executives on topics including supply chain plans. Just under half said they plan to use robotics and automation to build supply chain resiliency.
Technology solutions range from an ever-increasing use of industrial robots to tapping into more powerful uses of data, artificial intelligence, and machine learning. A key aim, of course, is increased efficiency, and one result of relying a bit less on human efforts is added flexibility when making location decisions. A big factor in the recent supply chain turmoil has been the increasingly global reach of operations. If finding cheaper labor was a big driver behind overseas operations, automation can make it more feasible to locate operations closer to home.
Indeed, the ABB survey found that more than a third of executives were making plans to bring production back to the U.S., and a third said they’d look at nearshore locations for new operations. In all, the survey found that 70 percent of companies are considering reshoring or nearshoring projects.
“There is an increased appetite to bring manufacturing and supply chains closer to end markets, closer to the U.S.,” Knizek says. “There are benefits to having sourcing closer to the U.S., Mexico, or South America.”
To be sure, costs remain lower in China and Southeast Asia, he says, and China has noteworthy supplier infrastructure advantages. “But increasingly, firms are looking to find ways to move production back to U.S. but need to lower costs and make the return on investment work.”
“Around 2015 to 2016, technology kind of finally caught up to a certain extent with promises it was making,” says Jason Bergstrom, Deloitte’s Smart Factory Go-To-Market leader and a partner in the firm’s manufacturing practice. Manufacturing, he says, has really started to shift from a human-centered operation to a process that’s increasingly automated. “We’ve seen technology really catch up and advance at an exponential rate and have made that shift to what we now think of as a hybrid — humans and machines operating together.”
The Future of Automation
Automation is getting better and cheaper all the time, on the production line and in the warehouse, according to Bergstrom. “The level of the bar between what should be done by a human and what can be done by a machine continues to fall on a cost basis and rise on a capability basis,” he says. “What made sense to automate in 2015 looks very different today because of the continually falling costs to automate combined with the fact that you can now do so much more as you transition from weak automation to strong automation.”
Less than a decade ago, he says, “you’d see just the automating of transactional, discrete tasks that required really no logic,” he explains. “A series of steps…a human used to do them, now a machine does them — easy to codify, with almost no logic.”
To use an automotive manufacturing example, imagine having a piece of plastic move into a fender press, and rather than have a human run that press, a machine conveys the plastic through and sends a fender out the other side. That was typical automation circa 2015, he says.
Automation can make it more feasible to locate operations closer to home. “Fast forward to today for that same operation,” Bergstrom continues. “It’s still automated, but with more advanced learning capabilities and vision capabilities. You take that same piece of plastic, use vision systems to do quality scans in an automated way, and kick out components and raw materials that don’t meet specs to eliminate quality issues downstream.”
Plainsight Corp., based in San Francisco, is one of many companies offering this kind of AI-powered computer vision capabilities in manufacturing. It promises such benefits as process automation and risk reduction, safety and productivity monitoring, precision counting along the assembly line, automated product and packaging inspections, quality monitoring, and defect detection.
“Currently, clever machines are used to improve and automate production processes, influencing quicker decision-making, better safety precautions, and high-quality improvements,” according to a white paper produced by Heriot-Watt University in Scotland. “With every manufacturer’s goal being to reduce risks and improve production efficiency, the role of artificial intelligence in this sector will continue to intensify.”
It’s no longer simple automation with robots assembling widgets, Knizek says. “You have intelligent robots, ‘cobots’ (collaborative robots) able to work side-by-side more effectively. You’re improving processes through more use of Big Data, predictive maintenance to reduce downtimes, or finding ways to anticipate process disruptions,” he says. “Firms able to leverage all of these technologies concurrently will be best positioned.”
“In the supply chain, AI can be used as a virtual assistant for robotic process automation and predictive analytics,” according to Ryan Prindiville, partner at the technology and consulting firm Armanino. “In today’s digitally connected world, AI is not just a nice-to-have; it’s an imperative to stay competitive. According to Gartner, supply chain organizations expect the level of machine automation in their supply chain processes to double in the next five years.”
Better Insights into the Supply Chain
Aside from employing more physical automation on the factory floor and at distribution centers, technology can enable a healthier supply chain by providing more visibility into operations and potential problems. A couple of key concepts, says Knizek, are supply chain control tower and digital twin solutions.
“Essentially you are trying to monitor the full end-to-end supply chain in an integrated and holistic manner, and trying to anticipate shortages before they occur,” he says. “This field has advanced significantly. You have firms that are still susceptible to issues in transportation and shortages of labor, but they are better able to get a handle on it.”
Technology can enable a healthier supply chain by providing more visibility into operations and potential problems. A supply chain control tower is essentially a dashboard of data and metrics. But to really provide the kind of visibility and insights that organizations need, it can’t just be a display of numbers. It must tap into advanced technologies such as AI with machine learning.
Extending control tower functionality with AI and machine learning can cut down on manual processes and offer the most actionable information. “Companies further along in this journey really use these tools on a day-to-day basis, and can anticipate problems weeks before they happen,” Knizek says.
Similarly, a supply chain digital twin is basically a simulation model of the actual supply chain. It brings in real-time data to help predict how the supply chain will behave and what unusual situations lie around the corner. It’s good for spotting bottlenecks before they become a problem, optimizing inventory, planning transportation, and testing any changes that might be planned for the supply chain.
The Impact on Location
The supply chain challenges of recent years have put the spotlight on the downsides of sourcing goods and materials from all over the planet. Onshoring and nearshoring are great remedies to some of those problems, but then you’re faced with costlier labor and the worker shortages happening closer to home. Automation can come to the rescue, Knizek says.
“It’s very hard for U.S. firms that have production overseas to bring production to the U.S. without putting in any kind of automation technology or artificial intelligence and machine learning that improves your efficiency,” he says. “There are still significant labor costs, and with inflation the way it is in the U.S., labor rates will go up. People will pay attention to tools they can use to lower the costs, to make them more in line with costs overseas.”
That doesn’t mean you have to match costs exactly when moving back closer to home, he adds. “The U.S. will never be able to compare with places like Vietnam and Indonesia,” he says. But if through automation you can get the total costs close enough, some of the benefits of producing goods closer to home start to win the day.
Beyond mitigating potential supply chain disruptions, those benefits include the elimination of international shipping costs, according to Saman Farid, CEO of Formic Technologies, speaking on a Thomas Industry Podcast. “We think that we can match, if not exceed, the kind of productivity of a Chinese factory here in the U.S. through technological innovation, and that innovation is in the form of drastically better automation, used at a much greater scale.”
Increasing automation may mean fewer humans, but it doesn’t mean no humans. Increasing automation may mean fewer humans, but it doesn’t mean no humans, Bergstrom points out. Deloitte has clients visit its “Smart Factory” in Wichita, Kansas, which is a showcase of production capabilities maximizing such technologies as AI, machine learning, Big Data, robotics, and vision solutions. “We intentionally talk to them about the machine-human interface that will never go away. The lion’s share of everything manufactured will always have a human component.”
That said, it requires a different labor mix to run such facilities. “Instead of a low-cost hourly person, you now have a different mix of people — developer, coder, maintenance. Although you are replacing an operation with an automation step, you have support roles that come into play,” he says.
“Right now, there’s a real need to hire people with more advanced skills such as mechatronics — you can’t hire enough of these folks,” Knizek says. “There’s a tremendous need for data scientists, and those are even harder to come by. There’s a real challenge right now in the manufacturing space to really get enough people with these skills.”
Bergstrom notes that in the past, manufacturing that wasn’t offshored was often set up in rural parts of North America, to achieve lower operating costs. That isn’t as easy to do with a more automated facility. “You’re actually seeing manufacturers get closer to urban centers than in the past, for that very reason,” he says. “Through automation and what we’re doing, it requires capabilities you’re not going to find in rural environments.”
“That drives all kinds of second-order questions,” Knizek says. “Where do you recruit? Do you set up your own training program? Do you need to raise wages to attract these people?”
Workforce development is always a vital topic in location decisions, but this reality is adding new twists, he says. “Any government looking to really position itself as a manufacturing hub with advanced manufacturing needs to be investing in all these topics.”
Project Announcements
Little Leaf Farms Plans Coffee County, Tennessee, Production Operations
07/02/2025
White Rock Truss & Components Expands Lee County, Virginia, Operations
07/02/2025
Fox Tank Company Plans Coshocton, Ohio, Operations
07/02/2025
Ascentek Expands Shreveport, Louisiana, Operations
07/02/2025
ProBio Establishes Hopewell, New Jersey, Gene Therapy Operations
07/02/2025
22nd Century Technologies Expands Fairfax County, Virginia, Headquarters Operations
07/02/2025
Most Read
-
20th Annual Area Development Gold and Silver Shovel Awards
Q2 2025
-
First Person: Joe Capes, CEO, LiquidStack
Q2 2025
-
The Legal Limits of DEI in Incentives Agreements, Hiring, and Contracting
Q2 2025
-
From Silicon to Server: Mapping the Data Center Supply Chain
Q2 2025
-
39th Annual Corporate & 21st Annual Consultants Surveys: What Business Leaders and Consultants Are Saying About Site Selection
Q1 2025
-
Rethinking Life Sciences Site Selection in a Resilient and Dynamic Market
Q2 2025
-
First Person: David Robey, Co-CEO of QTS Data Centers
Q2 2025