Cost is king, and time is money. You’ve done everything you can to remove all waste from the system, and everything is humming along the way that it should.
But you’re starting to see some interesting news stories about this unusual flu that you had never heard of before, which is being seen in a part of China. Clearly, it won’t have any implication for you, right?
Roots of the Problem
So, let’s back up slightly, and remind ourselves of just how flat the world has become in the past four decades or so. Manufacturers worked hard over that time to both produce goods in the lowest-cost locations and reduce waste and minimize the need for large warehouses full of inventory in favor of more nimble supply chains that deliver just what is necessary.
This shift from centralized, scale-driven production minimized the need for warehouse inventory, meaning firms only maintained enough safety stock to overcome minor delays. Over time, manufacturers came to rely on a continuous flow of goods and money, with constant communication between sections in a supply chain.
This worked well under typical circumstances. However, problems began when the systems designed to handle this “just-in-time” (JIT) manufacturing lacked the necessary adaptability in sourcing and moving goods to address the cascading series of imbalances that started to affect global trade.
At the outset of COVID, Hillebrand (freight forwarder) wrote, “countries implemented lockdowns, halting economic movements and production…[leading to] carriers [reducing] the number of vessels out at sea.” These effects lowered import and export volumes and also led to empty containers being stranded and not returned to their points of origin.
Manufacturers worked hard over [the last four decades] to both produce goods in the lowest-cost locations and reduce waste and minimize the need for large warehouses full of inventory. This became a significant problem for Asian traders, who couldn’t retrieve empty containers from North America. Then Asia, as the first hit by the pandemic, was also the first to recover, creating a further complication. While China resumed exports earlier than the rest of the world, other nations were (and still are) dealing with restrictions, a reduced workforce, and minimal production.
The results are extremely visible in the reporting of trade patterns. For example, the accompanying graphic is a measure of the container imbalance for the current year, and two years prior for reference. Values greater than 0.5 indicate an imbalance between inbound and outbound containers (causing an accumulation of unmovable containers).
There has been a huge influx of imports to the U.S. as the pattern of consumer demand pivoted from local spending to retail and e-commerce shopping requiring deliveries. This makes sense if you remember that families were required to quarantine, frightened to be in closed environments of stores and restaurants, and eventually changed their behaviors to embrace the convenience of home deliveries. Without enough workers in warehouses and trucks to efficiently move those goods, delays ensued, and containers were left taking up space in ports and warehouses.
This confluence of events resulted in an overall shortage of containers — combined with more ships waiting offshore to unload cargo due to insufficient port space — and then, in turn, led to even fewer vessels and containers available, cascading to reduce overall capacity. This shortage of capacity has resulted in reports that the cost of shipping a container from China to the West Coast has exploded to as much as 400 percent–600 percent over historical values (or more).
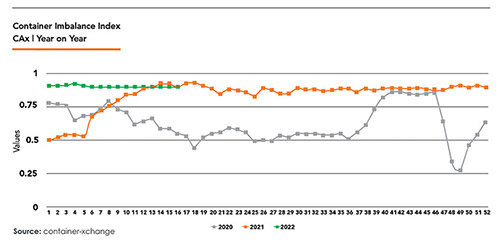
But what does this mean for our “flat-earth” global economy? Are we looking at an end or at least a slowdown of a globalized economy?
Probably not. As much as we may wish to have production capacity (and manufacturing jobs) come back to North America, the simple truth remains that for the short and medium term it is easier and less costly to create inventory than it is to re-create the infrastructure, capital investment, and workforce needed for substantial manufacturing. And this hypothetical rebuilding certainly cannot be done on the same cost basis as in other globally competitive locations.
However, there are circumstances that will keep forms of JIT as a preferred strategy for manufacturing. Professor Yossi Sheffi of the MIT School for Transportation and Logistics points out that JIT systems have preserved flexibility for manufacturers and given them the ability to react to shortages by quickly altering their supply chains and to avoid the historical problems of being tied to a large, pre-negotiated inventory of goods in the face of sudden shifts in demand.
There has been a huge influx of imports to the U.S. as the pattern of consumer demand pivoted from local spending to retail and e-commerce shopping requiring deliveries. In addition, near-shoring and reshoring, which reduce the distance between links in a supply chain, are also discussed as a potential solution, along with re-evaluating safety inventory stock levels. Each of these reactions can serve to alter the pattern of trade costs being expressed: reducing distance-related costs, altering the geography and concentration of partners to increase resilience, or increasing software integration to enable smoother planning and reaction to changes in conditions.
U.S. Transportation Secretary Pete Buttigieg has announced a novel pilot data exchange program called “Freight Logistics Optimization Works” (FLOW), which will involve stakeholders from all facets of goods movement from transportation to port operation to warehousing. This public-sector effort is centered around providing more continuous streaming of goods movement data to allow for real-time intelligence as a cost-saving and performance-enhancing mechanism.
This approach has already been taken up by individual companies in their pursuit of supply-chain resilience. Toyota has spent the past several years digging their way multiple levels into their supply chains to better understand not only their OEM and Tier 1 suppliers’ logistics, but even the logistics of Tier 2 and 3 suppliers, to better understand their risk and attempt to diversify supplier options.
There will be obstacles along the way. Broader adoption of mass data-sharing platforms such as FLOW will be slow and rife with pitfalls, especially given the sensitive nature of the data involved and the driving fear by firms of misuse for competitive gains. Many businesses will likely seek to privately invest in their own supply chains and not work in a broader integrated process, despite the benefits of scale participation. In this sense, development of new technologies and approaches may be more sporadic and occur at an individual firm level.
What Can We Do Now?
Responsible government agencies should and will look for ways they can assist in both reducing regulatory barriers and nurturing the development of new approaches — such as creating best practices in goods movement as well as protecting each company’s proprietary data.
A novel pilot data exchange program called “Freight Logistics Optimization Works” (FLOW) will involve stakeholders from all facets of goods movement from transportation to port operation to warehousing. FLOW may be an important first step toward trying to create a more adaptive and resilient future — but federal action as a data sharing coordinator is not the only way that the public sector can look toward future-proofing resilience issues.
The ability to look at vulnerabilities stemming from logistics operations both domestic and foreign, from a planning context, is of direct relevance to public agencies. The U.S. is a data-rich environment that allows companies to synthesize novel lines of thought for identifying, valuing, and managing risk. The ability to identify at-risk regional economies and industry — and then assess their relative risks from disruptions at border ports and along goods movement routes — can enable more informed prioritization of investments and identification of supporting strategies. These models can support more informed discussions with local business leaders and further help in planning for a more resilient future.
In the end, the more valuable outcomes that may result from this crisis are more likely to come in the form of technology and supply-chain diversification than to result in a wholesale change in where products are made. However, creatively addressing these problems will allow for a truly global economy to move to its next and more resilient stage.