No Easy Fix for Supply Chain Struggles
Labor shortages intertwined with other supply chain issues are creating gridlock at the nation’s ports.
Q4 2021
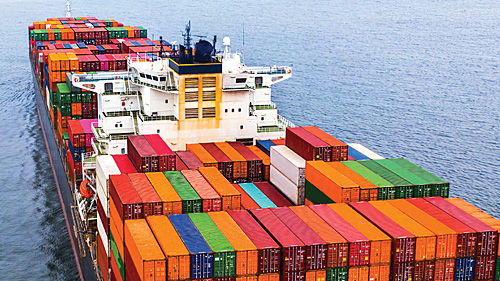
In March 2020, just one month into the pandemic, terminal operators implemented container storage programs, anticipating a short but intense spike in May 2020, when the pandemic was originally expected to end. At the height of the global health crisis, nonessential merchandise was put into storage to make way for critical cargo such as personal protective equipment, medical supplies, ventilators, and other essentials being expedited through the ports. The short but intense spike snowballed into the daunting situation we are facing today.
Globalization has increased dramatically in the last 40 years due to innovations in containerized shipping, concentrated production centers overseas, and a just-in-time fulfillment system that, until recently, delivered what was needed, when it was needed. It is an efficient but fragile system that relies on the seamless transfer of goods from production to consumption — certainly one that was not prepared for this level of economy-wide disruption.
Labor Shortages Among the Concerns
As we’ve witnessed, dislocations at any point of the supply chain result in a bullwhip effect, where relatively small changes set off a chain reaction. Usually, these disruptions are localized, and equilibrium is restored relatively quickly; however, this is not a normal case. And one of the biggest culprits in this mess? Labor shortages.
The unloading of cargo ships is also the third rail of U.S. shipping policy, domestic terminal productivity, and, in effect, the monopoly of longshore dockside labor. The International Longshoremen’s Association, AFL-CIO, the largest union of maritime workers in North America, has long fought the automation of terminals to increase the speed at which ships could be unloaded as a means of preserving high-paying union jobs.
Dislocations at any point of the supply chain result in a bullwhip effect, where relatively small changes set off a chain reaction. Currently at the ports of Los Angeles and Long Beach, ships greater than 6,000 TEUs (20-foot-equivalent units) take an average of 48 seconds to move a container, which is double the amount of time per TEU at automated Chinese ports. Little work can be done to address this issue until after July 2022, when the current labor contract between the dockworkers and terminal operators is set to expire. Should automation be a concession of the next labor contract, it would require hundreds of millions of dollars and years to fully implement before benefits are realized.
The Chassis Issue
While not the only issue, unloading efficiency is one in a long series of interconnected bottlenecks. Once the container is off the boat, it needs somewhere to go. The Harbor Trucking Association, a coalition of intermodal carriers and draymen, is one of the parties responsible for transporting containers from the port to the receiving warehouse. To do this, a chassis is required to haul the container to the warehouse, and another chassis is then returned to the port along with an empty container.
Typically, there is a healthy balance between full and empty containers and the chassis that is needed to haul them. But if there is an imbalance between sending and receiving, there will be a shortage of chassis at the port and goods will pile up until the chassis arrive to haul the goods away. At present, the high container volumes are stretching assets beyond capacity, and the shared pool of chassis used to keep the gears of commerce running is showing strain.
The dwell time of chassis, or the time chassis spend waiting between port trips, has increased to over nine days, due in part to the shortage of drayage drivers. (For reference, dwell times that exceed four days limit their overall availability and negatively impact marine terminal productivity.) Once the container has a chassis and a driver, it is sent to the receiving warehouse where goods are unloaded, broken down, and repackaged for their next destination — retail stores, other warehouses, or the customer’s front porch.
Heightened Consumer Spending/Panic Buying
Orders are typically fulfilled by warehouse workers, commonly referred to as pickers and packers. Oftentimes, these positions are subject to high turnover due to lower wages and few worker protections, though the tide is turning. California Assembly Bill 701, passed in September 2021, regulates warehouse performance metrics and offers protections to workers should they not meet certain productivity quotas. While this type of legislation may reduce turnover, employers are simultaneously faced with rising costs as more workers are needed to fulfill the influx of orders fueled by consumer spending that has surpassed pre-pandemic levels.
If there is an imbalance between sending and receiving, there will be a shortage of chassis at the port and goods will pile up until the chassis arrive to haul the goods away. At the height of the pandemic, 15.7 percent of all retail goods were e-commerce sales. That figure has drifted down to 13.3 percent as restrictions on brick-and-mortar shops have been lifted. In addition to home delivery, retailers are restocking shelves in anticipation of a “normal” holiday shopping season, and in many cases ordering more to replenish supplies that were drawn down over the pandemic. This can be seen in the inventory-to-sales ratio, which is the amount of goods on hand relative to the amount of goods sold.
The inventory-to-sales ratio hit an all-time low of 1.07 in April 2021, meaning retailers sold nearly 100 percent of their existing inventory. This is leading to panic buying as supply chain disruptions are being factored into restocking decisions. More orders of overseas goods lead to more ships docked outside of Los Angeles and Long Beach, which requires more chassis and drayage drivers to haul more containers, which in turn requires more warehouse workers and delivery drivers — all of which are in limited supply.
Some Remedies
In March 2021, the Biden administration created a task force to address growing supply chain issues. The administration met with port stakeholders to adopt 24/7 operations at the Port of Los Angeles to increase throughput of cargo containers. In addition, the administration has secured commitments from Walmart, Target, Home Depot, Samsung, UPS, and FedEx to take extraordinary measures to ensure additional freight movement, including extending hours and even chartering private cargo ships at significant expense to move cargo through less congested U.S. ports.
In March 2021, the Biden administration created a task force to address growing supply chain issues. To address the lack of truckers and draymen, the Biden administration is exploring the possibility of lowering the legal age of interstate truck drivers from 21 to 18. Other potential remedies include adding trucking to the list of jobs exempt from immigration certification and limiting the restriction on fully vaccinated essential workers from Canada and Mexico. In fact, a non-vocational high school in California is offering a truck-driving course to encourage the younger generation’s workforce to pursue a career in the industry. To address a shortage of warehouse workers, Amazon announced it was hiring 75,000 employees in the U.S. and Canada with increased pay, generous signing bonuses, and vaccination bonuses. Amazon is also targeting high school graduates, offering full college tuition for frontline workers.
The entirety of 2022 may not see much relief, and some of the bigger picture issues will persist for years to come, according to U.S. Transportation Secretary Pete Buttigieg’s assessment of the supply chain situation. Over time, new ships, containers, and chassis can be built, but we can’t ignore the human component as we strive to improve supply chain resiliency.
Project Announcements
AVAIO Digital Plans Brandon, Mississippi, Data Centers Operations
08/21/2025
Schütz Container Systems Establishes Kenosha, Wisconsin, Production Operations
08/21/2025
GE Vernova Expands Charleroi, Pennsylvania, Operations
08/18/2025
Busch Vacuum Solutions Plans Tempe, Arizona, Operations
08/18/2025
Made Scientific Establishes Princeton, New Jersey, Manufacturing-Headquarters Operations
08/18/2025
Comcast Establishes West Palm Beach, Florida, Operations
08/17/2025
Most Read
-
Tariffs, Talent, and U.S. Expansion
Q3 2025
-
What We’re Getting Wrong About Gen Z’s Future in the Skilled Trades
Q3 2025
-
A New Course for U.S. Shipbuilding
Q3 2025
-
Optimizing Your Rail-Served Transportation Network: Strategy Before Steel
Q2 2025
-
In Focus: AI Is Changing Incentives Math
Q2 2025
-
Rewriting the Rules of Warehouse ROI
Q3 2025
-
How to Choose the Right Site for Your Factory in 2025’s Volatile Landscape
Q2 2025