Rail Gains Advantage Amidst Supply Chain Snarls
Rail lines, which link international cargo gateways to U.S. population centers, offer companies a cost-effective, sustainable transportation option.
Q2 2022
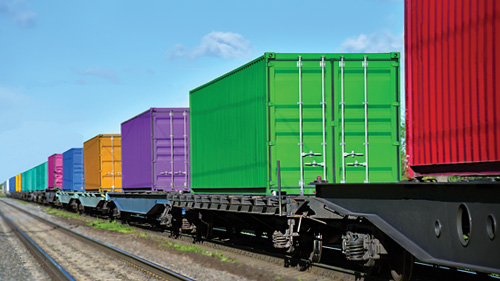
Many companies rushed to stock inventories in 2020, and they now need help distributing goods to consumers. Remarkably, international trade accounts for approximately 35 percent of U.S. rail revenue, 27 percent of U.S. rail tonnage, and 42 percent of carloads and intermodal units, according to the American Association of Railroads (AAR), an industry trade group. The flow of goods arriving or departing by ship has led to record levels of demand and huge year-over-year growth — along with significant congestion — at top U.S. ports.
By 20-foot-equivalent unit (TEU), which is the standard measure of container volume, the top U.S. container ports are Los Angeles/Long Beach, New York/New Jersey, Savannah, and Seattle/Tacoma. Other key U.S. ports by container TEU volume are Houston, Norfolk and Oakland (San Francisco), and Charleston, S.C. From these ports, the majority of consumer goods flow to the interior of the country to inland hubs and distribution nodes.
Interstate highways and rail lines are the barbells that link international cargo gateways to U.S. domestic population centers. Interstate highways and rail lines are the barbells that link international cargo gateways to U.S. domestic population centers. For most companies, trucking is the primary shipping method, and one often combined with rail in intermodal shipping strategies. Unlike a train, a truck does not require a rail terminal at every delivery point and can navigate dense urban markets.
However, rail is gaining advantage as the price gap narrows between freight rail and trucking, and rail becomes more effective from a service perspective. Port congestion has led to very long waits for ships to load or unload cargo containers, and long waits for cargo to be loaded to and from trucks or railcars. Delays add to the costs, as ports charge fees for container storage and other services. Further adding to trucking’s downsides are the chronic truck driver shortage, rising fuel prices, and corporate environmental sustainability concerns.
Freight Rail’s Inland Reach
Inland hubs such as Kansas City, Dallas, Chicago, Memphis, Atlanta, and eastern Pennsylvania benefit from direct rail service from major U.S. seaports. Containers are shipping via expedited unit trains, consisting of cars of a single type, such as tankers, hoppers or intermodal containers, that carry a single type of commodity — all bound for the same destination and often several miles long. These trains typically reduce delays for the end user as containers are only handled or “touched” two or three times between the arrival port and the cargo recipient’s loading dock.
While an increasingly diverse mix of cargo is shipped via intermodal transportation, companies must understand the cargo mix and types of services provided at different terminals to make their real estate decisions. In Chicago, for example, BNSF Logistics Park Chicago in Elwood primarily handles international traffic to and from the West Coast, while the infill City of Chicago Corwith Terminal handles domestic containers to and from California and Dallas/Ft. Worth.
Companies must understand the cargo mix and types of services provided at different terminals to make their real estate decisions. Conversely, Norfolk Southern’s Landers Terminal in Chicago primarily handles double-stacked ocean containers traversing the premier corridor to and from northern New Jersey and Baltimore. Additionally, Norfolk Southern’s Atlanta Inman domestic terminal primarily handles containers headed to and from inland hubs in Croxton, New Jersey, and Rutherford, Pennsylvania.
Panama Canal Expansion Dynamics
The Panama Canal expansion changed the competitive dynamics of shipping by rail from the U.S. West Coast. Shippers and U.S. port authorities have been upgrading near-dock transportation and storage capacity as the key U.S. East Coast and Gulf Coast ports see increased volumes of containerized cargo.
Correspondingly, inland ports have grown in importance, as near-dock coastal land is increasingly valued at a premium and moving containers by rail to an inland port frees up valuable near-shore real estate — improving the flow of goods for bulk or automotive roll-on/roll-off (RORO) traffic. Over the long term, the majority of containerized imports will likely still flow from the U.S. West Coast, but East Coast ports will continue to grow market share.
The re-shoring or “regionalization” of manufacturing is creating new opportunities for intermodal services and logistics real estate, especially in the automotive and industrial goods sectors. The Midwest is unique in that cities such as Chicago, St. Louis, Memphis, and Kansas City benefit from at least three Class I rail providers serving the market, whereas most coastal markets are only served by two individual railroads.
Growing Freight Volumes
To keep inventory moving to its final destination and reduce costs, oftentimes logistics and transportation hubs must transload 20- and 40-foot international containers from the gateway ports and repack the goods into standard U.S. 53-foot boxes. As a rule of thumb, three 40-foot containers can be re-packed into two 53-foot containers that, if double-stacked on a railcar, speed time to market and drive down transportation costs.
As freight costs go up and delivery time or service requirements become more compressed, many companies are deploying distribution facilities closer to their end customers and shifting additional volume to rail — which is why freight volume has been shifting from the nation’s highways to rail over the past decade. The railroad industry has been a major driver of the economy for generations, with Class I railroads moving more than 1.7 billion tons of freight annually over 92,000 miles of track in 47 states.
Today, about 40 percent of U.S. freight is shipped by the U.S.’ seven major railways, and along the country’s 47,500 miles of short-rail lines ranging from one to more than 1,500 miles long — more than any other mode of transportation.
Rail is gaining advantage as the price gap narrows between freight rail and trucking, and rail becomes more effective from a service perspective. Intermodal shipping — combining trains and trucks — has been the fastest-growing transportation mode in the United States since the mid-1990s. The AAR said, during the first half of 2021, railroads handled the highest volume of intermodal traffic ever moved in that period.
Intermodal volumes declined coming into 2021 because of the overall logjams in the global supply chain. However, intermodal shipping continues to be ideal for many kinds of goods, enabling shippers to reach diverse markets and balance the costs — including environmental costs — of trucking and freight rail. It’s all about the ongoing battle to drive costs out of the supply chain while at the same time delivering goods more quickly.
Rail Infrastructure Improvements Are Benefiting Shippers
Having a robust and flexible infrastructure is crucial. Just as the nation’s busiest cargo seaports are investing billions to enhance their operational efficiencies, the continent’s leading rail operators are as well. Unlike trucks and barges, however, freight railroads operate overwhelmingly on infrastructure that they own, build, maintain, and pay for themselves.
Class I railroads are undertaking massive infrastructure and technology improvements, expanding their terminal networks to boost efficiency and position themselves for long-term growth in the intermodal segment. From 1980 to 2020, America’s freight railroads spent nearly $740 billion — averaging approximately $25 billion a year — on capital expenditures and maintenance expenses, according to the AAR.
With improvements in railroad service times and safety records because of signal and communications upgrades, freight rail has become more price-competitive with trucking. The major railroads have anticipated future growth, creating flexibility in their networks to absorb projected population swings in certain regions of the country. Also, track and line improvements are helping to add more capacity via trains with double-stacked containers traveling along key intermodal routes.
As a result, railroads have more reliable schedules than in the past, and parcel carriers are able to move more product via intermodal centers in both trailer on flatcar configuration and in the traditional 53-foot containers. Further investments in rail infrastructure and technology, such as automated gate systems and other advances to improve in-freight matching, as well as more real-time inventory visibility, will add efficiency to intermodal shipping.
Rail’s Sustainability Advantage
Despite carrying 40 percent of the nation’s freight, rail accounts for a mere 0.5 percent of total U.S. greenhouse gas emissions, per U.S. EPA data. Idling trucks, in contrast, contribute to approximately 20 percent of annual U.S. carbon emissions.
Railroads are the most fuel-efficient way to move freight over land, moving one ton of freight more than 480 miles per gallon of fuel, on average. On average, railroads are three to four times more fuel-efficient than trucks. A single freight train can replace several hundred trucks. Railroads are the most fuel-efficient way to move freight over land, moving one ton of freight more than 480 miles per gallon of fuel, on average.
Today’s locomotives are far more fuel-efficient than in the past, emitting fewer pollutants and greenhouse gasses (GHGs) over the past decade. Idling-reduction technology, such as stop-start systems, reduce unnecessary emissions-heavy idle time by 50 percent. Advanced software improves fuel efficiency up to 14 percent by calculating the most efficient speed, spacing, and timing of trains.
Moving freight by rail instead of truck lowers greenhouse gas emissions by up to 75 percent, on average, by AAR analysis. Furthermore, if 50 percent of truck traffic moving at least 750 miles went by rail instead, greenhouse gas emissions would fall by approximately 26.2 million tons. In 2020 alone, U.S. freight railroads consumed 675 million fewer gallons of fuel and emitted six million fewer tons of carbon dioxide than they would have if their fuel efficiency had remained constant since 2000.
Rail Can’t Solve All Supply Chain Issues
While no single freight mode can overcome today’s logistics snarls, the rising economic cycle of consumer spending and imports continues to bode well for freight rail. U.S. rail freight revenues are forecast to advance 4.7 percent per year in nominal terms through 2025, according to market research firm Freedonia Focus Reports. Trucks will, of course, always continue to play an important role in distribution, but rail transportation will continue to grow as a viable, cost-effective, sustainable transportation option for companies in the future.
Project Announcements
MR6 Tech Services Plans Huguley, Alabama, Manufacturing Operations
07/29/2025
Adient Plans Normal, Illinois, Production Operations
07/29/2025
UK-Based WB Alloys Plans Danville, Virginia, Manufacturing Operations
07/29/2025
L3Harris Technologies Expands Camden, Arkansas, Production Operations
07/25/2025
Baltimore Fabrication Expands York County, Pennsylvania, Manufacturing Operations
07/25/2025
Mueller Streamline Expands Wynne, Arkansas, Manufacturing Operations
07/25/2025
Most Read
-
20th Annual Area Development Gold and Silver Shovel Awards
Q2 2025
-
In Focus: AI Is Changing Incentives Math
Q2 2025
-
Optimizing Your Rail-Served Transportation Network: Strategy Before Steel
Q2 2025
-
How to Choose the Right Site for Your Factory in 2025’s Volatile Landscape
Q2 2025
-
From Silicon to Server: Mapping the Data Center Supply Chain
Q2 2025
-
Tariffs, Talent, and U.S. Expansion
Q3 2025
-
First Person: David Robey, Co-CEO of QTS Data Centers
Q2 2025