To Cluster or Not to Cluster…That is the Question!
Although clusters are here to stay in some sectors — think life sciences — other industries — among them EVs and semiconductors — are geographically branching out.
Q3 2022
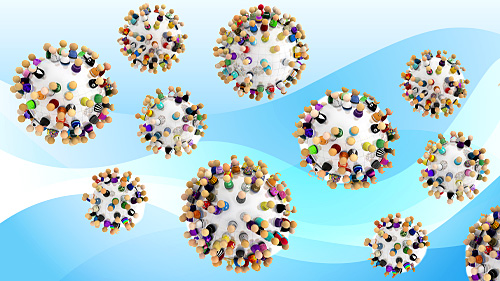
Disruption has created opportunity for U.S. manufacturing. Following various supply chain disruptions and lengthy logistics logjams beginning in 2020, many manufacturers have been near-shoring or on-shoring their manufacturing operations and reconfiguring their supply chain networks.
Shifting Manufacturing and Supply Chain Footprints
No wonder JLL Research finds that demand for U.S. manufacturing-related facilities soared 93 percent year-over-year from the first quarter of 2021 to the first quarter of 2022. More than 1,800 companies reshored manufacturing in 2021, and reshoring is expected to create 350,000 new U.S. jobs by the end of 2022, up from 260,000 in 2021, according to The Reshoring Initiative®’s IH 2022 Data Report.
To be clear, the shifts are not limited to the United States. Manufacturers with customers around the world are looking to keep operations close to customers to reduce the risk of future supply chain delays and facilitate product delivery. Moving manufacturing closer to consumers — whether in the Americas, APAC, or EMEA — also helps mitigate risk and the impact of high shipping costs. In some sectors, traditional industry or logistics clusters are less important than they have been at any point in the past.
Many companies also have diversified their supplier networks to avoid over-dependence on any single company or country. The life sciences, pharmaceuticals, heavy equipment, electronics, and semiconductor industries, in particular, suffered serious impacts when supplies became unavailable as the pandemic disrupted manufacturing and business activity in APAC.
Meanwhile, the conflict between Russia and Ukraine has disrupted global energy markets and added pressure to skyrocketing energy costs, with particular impact on chemicals, resins, plastics, fertilizers, paper, and pulps industries reliant upon natural gas. The United States and Canada have emerged as countries of choice and highly attractive locations for high energy, gas-reliant manufacturers.
Within the United States, however, the industries most affected by current trends are not necessarily locating in or near industry clusters. Multiple factors are pushing manufacturers beyond the traditional cluster markets. The tight market for labor — in particular for skilled manufacturing jobs — has made access to labor more of a challenge than in that past, driving manufacturers to areas with available labor pools. Tax incentives are always a factor, as is access to rail, highways, and other shipping infrastructure. Large developable land sites are also harder to come by, as manufacturers are often competing with logistics companies for major parcels.
The Dispersed Footprint of EV Manufacturing
EV manufacturing, in particular, is not developing around the historic automotive centers of Detroit. While some EV manufacturing has settled in Michigan, the largest U.S. manufacturing developments are under way in 17 different states, including Arizona, Texas, Georgia, Ohio, Tennessee, and Indiana.
EV manufacturing, in particular, is not developing around the historic automotive centers of Detroit. The United States is becoming a location of choice for companies producing electric vehicles (EV) and EV batteries as major domestic automakers shift production to EVs in response to soaring global demand. Recent federal legislation — including the 2021 Infrastructure Investment and Jobs Act (IIJA) and the 2022 Inflation Reduction Act (IRA) — has provided funding and expanded tax credits to accelerate the transition to clean energy infrastructure and EV vehicles for public transit and the commercial and consumer markets.
It is hard to “cluster” big manufacturing operations, such as EV and EV-related manufacturing, when each plant requires large ready-to-develop land sites, supply chain infrastructure, access to labor, as well as tax and economic incentives. EV manufacturers also are attracted to areas with comparatively low energy costs to reduce production costs.
Semiconductors Nationwide
With factories coast-to-coast in 18 states, the U.S. semiconductor industry is another that is not clustered around a particular location, according to the Semiconductor Association’s 2021 State of the U.S. Semiconductor Industry report. Semiconductor manufacturing is resurging in the United States, with new manufacturing facilities planned in locations far beyond the industry’s roots in Texas and Silicon Valley. Intel, for example, is expanding its U.S. footprint by investing billions of dollars into two chip production plants in Arizona and two in Ohio, and an advanced packaging facility in New Mexico.
In 2020, TSMC also announced plans to build a factory near Phoenix, Arizona, to be near the talent and suppliers already supporting Intel. Meanwhile, Samsung Foundry announced in late 2021 that it is building a plant near Taylor, Texas. Near Sherman, Texas, Texas Instruments began construction on a new facility in May 2022. GlobalFoundries also is expanding its U.S. manufacturing, investing in additional capacity at its Malta, New York, headquarters. The U.S. semiconductor industry is another that is not clustered around a particular location.
Most recently, Idaho-based Micron announced that it will invest up to $100 billion to build semiconductors in New York State — reportedly the largest semiconductor fabrication facility in the history of the United States and possibly the largest in the world. The state is providing $5.5 billion in state tax incentives for the project, which is also likely to tap CHIP tax credits.
Clusters Here to Stay in Some Industries
As some industries develop in diverse locations, others continue to benefit from logistics clusters. Life sciences organizations, for example, continue to cluster in such markets as the San Francisco Bay area, New Jersey, San Diego, Boston, and Raleigh-Durham. Manufacturers of petrochemical products, resins, and plastics tend to cluster around ports to streamline exports.
As some industries develop in diverse locations, others [e.g., life sciences] continue to benefit from logistics clusters. One reason is that clustering reduces the cost and time of delivering product to end-users. With proximity to multiple downstream manufacturers, suppliers can exploit economies of scale while offering customers faster, lower-cost deliveries. Clustering also can produce a labor pool with specialized industry knowledge — which is a major reason why life sciences companies tend to cluster around major life sciences research organizations. In addition, geographic proximity can spur innovation as small entrepreneurs and established manufacturers come together in economic activity as well as research and development.
Whatever the industry, a myriad of factors enter into site selection decisions for manufacturing operations. With access to strong labor pools, logistics infrastructure, energy, and large shovel-ready sites among the primary concerns, companies are willing to look outside traditional industry clusters with regard to their strategic U.S. manufacturing location decisions.
Project Announcements
MR6 Tech Services Plans Huguley, Alabama, Manufacturing Operations
07/29/2025
Adient Plans Normal, Illinois, Production Operations
07/29/2025
UK-Based WB Alloys Plans Danville, Virginia, Manufacturing Operations
07/29/2025
L3Harris Technologies Expands Camden, Arkansas, Production Operations
07/25/2025
Baltimore Fabrication Expands York County, Pennsylvania, Manufacturing Operations
07/25/2025
Mueller Streamline Expands Wynne, Arkansas, Manufacturing Operations
07/25/2025
Most Read
-
20th Annual Area Development Gold and Silver Shovel Awards
Q2 2025
-
In Focus: AI Is Changing Incentives Math
Q2 2025
-
Optimizing Your Rail-Served Transportation Network: Strategy Before Steel
Q2 2025
-
How to Choose the Right Site for Your Factory in 2025’s Volatile Landscape
Q2 2025
-
From Silicon to Server: Mapping the Data Center Supply Chain
Q2 2025
-
Tariffs, Talent, and U.S. Expansion
Q3 2025
-
First Person: David Robey, Co-CEO of QTS Data Centers
Q2 2025