How VW Achieved LEED Platinum-Rated Construction
Volkswagen of America earned LEED® Platinum certification due in part to recycled and regional materials and construction waste management.
Q2 / Spring 2013
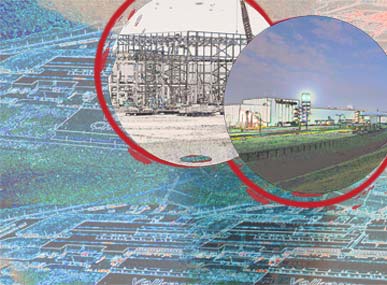
The first and only LEED Platinum automotive manufacturing plant in the world, the $1 billion, 2.7-million-square-foot facility was awarded 52 points, which included eight points in the critical categories of recycled content, regional materials, and construction waste management. Recycled content and regional materials each comprised more than 45 percent of total building materials, and the construction team salvaged or recycled nearly 78 percent (4,602 tons) of construction and demolition waste.
Those eight points represented more than 15 percent of the total points required to achieve Platinum certification. The awarding of the credits depended on general contractors for documentation of material content and site accountability for construction waste management. Even though the LEED requirements in these three areas have become best practices for sustainable construction, the documentation is not a standard construction practice.
Volkswagen achieved this Platinum rating with detailed planning, research, modification of standard construction practices, and contractor oversight guided by a dedicated on-site LEED coordinator on the A/E/CM (architecture/ engineering/construction management) team.
The Role of On-Site LEED Coordinator
Although some general contractors have experienced LEED-accredited professionals on staff, the success of a complex project may well depend upon a single point of responsibility to research the local market, provide guidance and insights in planning, oversee contractors in the documentation process, and manage the LEED submittal.
In the case of the Volkswagen project, a coordinator from SSOE Group fulfilled the single point role throughout the lifecycle of the project. Before beginning the LEED certification process, SSOE created a handbook for contractors that condensed the U.S. Green Building Council’s reference manual into the practical requirements to fulfill each checklist item. The LEED coordinator included the results of advance research to identify local companies that could supply specific materials and buy specific types of construction waste.
Since this was such a large facility, more than 40 separate contracts were issued. Each contractor had different responsibilities, based on its scope of work. SSOE’s LEED coordinator then created a spreadsheet that identified every Volkswagen contractor package, including the associated LEED requirements; specific criteria — e.g., percentages and weights of recycled and regional materials; and documentation status. This system allowed SSOE to verify that documentation was submitted in a timely manner and that each contract package was on track to fulfill the requirements. This data was uploaded to LEED online on the contractors’ behalf, which streamlined the submittal process and ensured accuracy. Because accuracy is critically important when preparing the submittal, errors can trigger a time-consuming audit and jeopardize LEED accreditation. In the Volkswagen project, attention to document accuracy helped the team complete the LEED submittal and review process quickly and cleanly.
Documenting Recycled Content and Regional Materials
The LEED categories of “recycled content” and “regional materials” recognize the significant environmental impact of using such materials, eliminating the extraction process of virgin materials and reducing transportation. However, their documentation poses a serious challenge. These categories include calculations of materials as percentages of the total cost of building materials, along with verification that these percentages will meet LEED requirements. To capture and verify documentation requires careful planning, a well-managed process, and linkage between documentation and contractor compensation.
Contractors must obtain documentation of all recycled and regional materials directly from the manufacturers and submit documentation at specified intervals throughout the construction phase of the project. This requirement must be understood and satisfied from the outset: first in project planning, then in the RFP, and finally as condition of contract payment applications.
For materials that compose a large percentage of the total project construction cost, verification of manufacturers’ statements is particularly important. For example, steel and concrete are the big-ticket materials in an industrial manufacturing facility like the Volkswagen plant. Moreover, not only must pre- and post-consumer recycled content be separately calculated, but the documentation must also be provided by the manufacturers to the general contractors — and there is no standard format. In the Volkswagen project, the on-site LEED coordinator carefully interpreted the manufacturers’ statements and calculated the specific percentages of pre- and post-consumer recycled content of each type of recycled material. She then calculated the percentage that each material contributed to the total cost of building materials. Similarly, the coordinator interpreted and verified the manufacturers’ statements about the sources and percentages of regional materials composing each regional construction material and the percentages of total construction materials.
Linking contractor compensation with submittal of the documentation was the final step. Contractors were contractually obligated to gather and submit the required documentation. As an incentive for timely submissions, the approval of their monthly invoices was made contingent upon receipt of this documentation. For the Volkswagen project, the LEED coordinator tracked the contractors’ progress on documentation as invoices were submitted and issued reminders when necessary.
Site Accountability for Construction Waste Management
According to the 2009 study from the EPA, 160 million tons of debris are generated from the construction industry each year. A recycling program included with construction waste management diverts construction materials and demolition debris from landfills.
For construction waste management, site accountability is the major challenge in meeting the LEED requirements because separation and recycling a high percentage of construction waste is not standard construction practice on conventional construction projects. Without someone effectively encouraging a construction waste management program, materials that could be recycled often end up in landfills or incinerators. A contractor may improperly utilize the dumpsters of another contractor, and this would cause cross contamination, unnecessary waste, or both.
Although it would be beneficial to award a single contract for construction waste management, it is typically the responsibility of each contractor. Contractors are working hard, and often overtime, to meet the schedule and fulfill their obligations, and construction waste management may not be high on their list of priorities. On a large project with a thousand workers on-site, it’s time consuming to separate and properly recycle all waste. It requires careful oversight by each contractor, and it takes the support of the construction management team and owner to follow and document waste management protocols. This is the only way to secure the maximum LEED credits.
During the Volkswagen project, individual contractors monitored and protected their containers. Their strategies included fencing their containers, moving their containers to more remote locations, posting a worker to sort materials, and even partnering with other contractors to consolidate small amounts of particular waste materials in a single container. SSOE’s on-site construction management team periodically observed the process of separating and distributing waste among the various containers. The on-site LEED coordinator monitored the monthly submittals of construction waste documentation to identify instances when corrective action was needed.
The overall success of a LEED project is based on many participants, including owners, designers, and contractors. The vision may begin with the owner and the design team, but will not be successful without the dedication and cooperation of the contractors building the project. On this project, Volkswagen, with a practical commitment to sustainability, considered sustainable design and construction a social responsibility. Teaming with hardworking and like-minded companies, they achieved the highest standard achievable. The result was Platinum!
Project Announcements
Apex Plastics Opens Expanded Production Plant In Brookfield, Missouri
09/22/2014
Japan-Based Bridgestone Rubber-BSA Opens Biorubber Process Research Center In Mesa, Arizona
09/22/2014
SpencerARL Expands Its Plattsburgh, New York, Manufacturing Facility
09/22/2014
Hill International, Inc. Relocates Corporate Headquarters To Philadelphia, Pennsylvania
09/22/2014
Prysmian Group Plans $8.2 Million Expansion At Abbeville County, South Carolina, Manufacturing Center
09/22/2014
Japan-Based Kowa Kentucky Plans $8.3 Million Manufacturing Facility In Corbin, Kentucky
09/22/2014
Most Read
-
Tariffs, Talent, and U.S. Expansion
Q3 2025
-
What We’re Getting Wrong About Gen Z’s Future in the Skilled Trades
Q3 2025
-
A New Course for U.S. Shipbuilding
Q3 2025
-
Optimizing Your Rail-Served Transportation Network: Strategy Before Steel
Q2 2025
-
Data Center Demand Stabilizes Amid Changing Market Forces
Q3 2025
-
In Focus: AI Is Changing Incentives Math
Q2 2025
-
Rewriting the Rules of Warehouse ROI
Q3 2025