One of the most critical site selection factors for any project is occupancy and construction costs. Although it is one of the biggest expenses a company faces during a relocation or expansion, it is a fairly predictable cost that is generally not complex to determine and factor into budgets.
There are also some key options associated with occupancy and construction — it may be more cost-efficient to move into an existing building compared to constructing a new facility, for example. It is also easier to get up and running when leasing or purchasing an existing facility, compared to waiting on a construction project — especially if funding is a challenge. However, if a company is highly specialized, it may prefer constructing its own building that totally fits its needs. Construction costs — including site acquisition, site preparation, and installing infrastructure — can often be discounted through incentives from local and state governments. Land may even be donated to the company for the project.
Construction Labor & Material Costs
The larger the rehabilitation or construction tab, the more important the cost differences become in the site selection process. Construction costs are mostly tied to labor and material costs. As a result, the main difference from location to location will be labor costs for construction, since material costs are about the same across the country. Construction labor costs can also be impacted by whether the area is experiencing a construction boom or is struggling economically. Construction labor costs can vary by up to 10 percent or more depending on the region — this difference can have a big impact on an expansion/relocation budget.
Site selection experts often consult the RS Means Construction Cost Index for the latest material and labor costs across the country. Presented by Reed Construction Data, the index tracks construction cost trends from January through December, with reports issued every quarter. Cities that show higher construction cost trends over the last year or two may have more difficulty competing with other locations on the short list.
Variable Across Regions
Just like construction costs and labor costs, occupancy costs also vary dramatically from region to region. For example, according to CBRE’s December 2012 Prime Office Occupancy Costs report, occupancy costs in downtown San Francisco increased to $90 per square foot from September 2011 to September 2012 — a 36 percent jump. In Seattle the increase was closer to 22 percent. These trends are driven by the resurgence of high-tech companies in these areas as the economy improves.
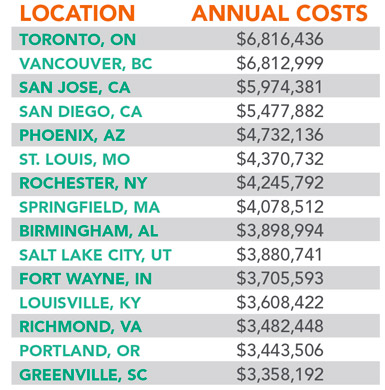
Often times, site selection consulting firms maintain their own proprietary occupancy costs databases. The Boyd Company of Princeton, N.J., put together such a database for a manufacturing client in the metalworking sector. Overall costs can range significantly regionally when all inputs are considered.
Oftentimes, site selection consulting firms maintain their own proprietary databases. The Boyd Company of Princeton, N.J., put together such a database for a manufacturing client in the metalworking sector. Key considerations included a work force of 225 people, land acquisition (25 acres of fully serviced, industrially zoned land), construction of a 140,000-square-foot light industrial building, and local property and sales taxes. Land and construction costs were amortized over 25 years at 5 percent interest. According to Boyd’s database, annual occupancy costs (land, construction, property, and sales taxes) for this project ranged from a high of $6.8 million in Toronto to a low of $3.3 million in Greenville, South Carolina.