“Companies must seek new ways to find the right talent, develop skills, and share expertise,” says Mike Ettling, president of UK-based HR Line of Business at SAP in a recent article on Forbes.com. “One of these strategic approaches is the growing reliance on consultants, intermittent employees, or contingent labor.”
Once only considered as a last resort by companies to reduce labor costs, contingent workers are now used by manufacturers on an increasingly regular basis. For example, Accenture indicates that contingent workers comprise up to one-third of the U.S. workforce.
“Businesses are increasing their dependency on contingent labor — even if the global economy is improving,” adds Ettling. “According to Workforce 2020, a study conducted by Oxford Economics and sponsored by SAP, 83 percent of executives indicate they’re increasingly using contingent workers — at any time, on an ongoing basis.”
With this kind of impact, contingent workers must be more thoroughly integrated into HR’s long-term planning.
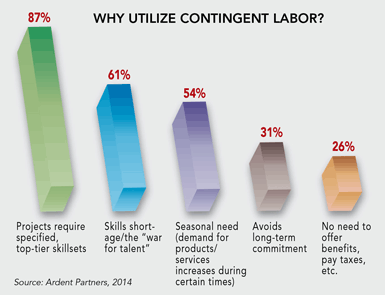
Ardent Partners predicts that, by 2018, nearly 45 percent of the world’s total workforce will be contingent. The company’s research indicates that the overwhelming driver behind hiring contingent labor is the pressing necessity to acquire the required top-tier skillsets needed to get the job done.
As a result, more manufacturing companies are turning to staffing firms that specialize in providing workers with high levels of industry-specific training. In the medical-device industry, for example, part-time workers who are properly trained in current good manufacturing practices (cGMP) and other industry-specific standards are much more productive when they start work, with a far shorter learning curve.
“When an OEM is ramping up for a new product, labor requirements typically fluctuate significantly for its contract manufacturer,” states Terry Hamm, vice president of Quality Assurance/Regulatory Affairs for GW Plastics USA in Bethel, Vermont. “Using cGMP-trained, part-time employees who have been thoroughly trained to produce and assemble medical devices improves quality, reduces risk, and lowers overall cost.”
“Compliant” Labor Boosts Efficiency
A staffing firm that provides highly trained contingent workers for healthcare product manufacturers is Operon Resource Management in Lowell, Massachusetts. Although not a manufacturer itself, Operon decided to become ISO 13485-certified (an international standard for quality management systems for medical device companies) so it could better align with the needs of its medical-device manufacturing clients at the deepest possible level.
“Developing a well-defined and documented quality management system allows us to understand the stringent quality requirements of this highly regulated industry and bring more value to our clients,” says Steve Sawin, president of Operon Resource Management.
Hamm agrees: “Compliant labor allows managers to focus on planning for continuous improvement…Using knowledgeable, highly skilled workers on the line who know medical-device manufacturing regulations speeds up production and eliminates many of the issues that cause line stoppage.”