For sponsor Raytheon, the object wasn’t to preserve an egg, but to grow a future workforce. “Rocketry requires a strong command of math, a solid foundation of physics, and a tremendous amount of patience and determination,” said Raytheon Chairman and CEO Thomas Kennedy — exactly the qualities the company requires of its scientists, engineers, and technicians.
This is Raytheon’s tenth year supporting the U.S. team at the international air show. “The achievement of these competitors deserves a global stage and we hope to show other students around the world that hard work and a love for science can lead them to great things,” said Kennedy. The program is part of the company’s broadbased MathMovesU® initiative to encourage students to pursue careers in STEM fields (science, technology, engineering, and math). It is also indicative of a larger trend of companies becoming much more proactive in developing the workforces they’ll need in the future.
Community colleges have always been a critical pipeline of talent. By working with employers to actually develop course content, we are able to help students develop high-demand skills in the context of a meaningful academic environment. Dr. Brian Inbody, President of Neosho County Community College A Perfect Storm
Industry benefited from the cornucopia of available workers made possible by the baby-boom demographic bulge. Now, however, they must deal with the rapid deflation of the workforce bubble as the boomers retire. Replacing them are generations X, Y, and millennials who have come of age in an entirely different technological and cultural environment.
In their labor force projections through 2022, the Bureau of Labor Statistics sees slow growth (0.5 percent annually) in the U.S. labor force, but continued declines in the labor force participation rate as baby-boomers age out of their prime working years.
Within 10 years, millennials are projected to comprise 75 percent of the available workforce. As experienced workers retire, they leave with knowledge and skillsets often crucial to meeting customer demands. This perfect storm of departing skills and a younger workforce, perhaps not as enamored of industrial production as their parents or grandparents, presents unique challenges to automotive, aerospace, and many other industries.
Working Collaberatively
On the plus side, changing demographics is bringing a new crop of younger CEOs to the helms of many companies like Boeing and Harley-Davidson. They tend to be focused on talent and technology development, and open to partnerships between educators and corporations. These partnerships can develop a skilled workforce pipeline for companies and relevant curriculum for educators.
One such partnership is just now taking shape through the Boston-based non-profit Jobs for the Future (JFF). The workforce development organization has formed the College Employer Collaborative with four community colleges around the country, online training provider CorpU, and several major employers including AGCO, MetLife, and Boeing.
A unique feature of the Collaborative is that employers, rather than schools, create the educational curriculum, says JFF Senior Program Director Mary Wright. “It’s essentially shifting the supply and demand because we’re saying, now, the employers are going to supply the content. But we are asking the community colleges to provide the structures and support that community colleges are really good at in terms of trying to get people to complete and understand how to work this into their course of study, as well as providing the technology that allows people to be able to access this material. And so, theoretically now, with the employer creating the content, the people who are taking the classes will have both the technical and soft skills that the employers are really looking for.”
The first community colleges to join the Collaborative are Neosho County Community College in Chanute, Kansas; LaGuardia Community College in New York; Alamo Colleges in Texas; and Everett Community College in Washington State.
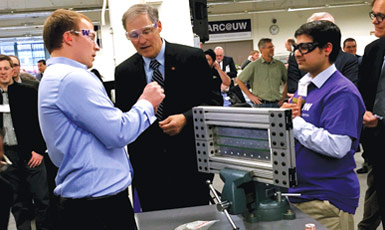
The first courses open this fall. The Collaborative is funded by the Bill and Melinda Gates Foundation, but Jobs for the Future’s business plan anticipates the program becoming self-sustaining as more companies and colleges join. As the course library expands, JFF’s Wright believes companies will use the Collaborative’s courses to train incumbent workers. “If they’re a member of the College Employer Collaborative, they would be able to use those classes on their own workforce at a fraction of what they would have to pay to design something on their own.” Those fees, she believes, will sustain the program once grant funding ends.
K-12 Initiative
Stung by criticism (sometimes warranted, sometimes not) that students are leaving their institutions unprepared for the workplace, schools at various levels are taking the initiative to form partnerships with companies in their areas.
One example in central Ohio is the combination of K-12 schools, a career center, technical college, and four-year university reaching out to area employers in and around Marion, Ohio, to design career paths that make sense for the employers as well as each institution’s students. With two Honda assembly plants, numerous supplier plants, a robotics integrator, and the world’s largest clothes dryer plant within a 40-minute drive, the schools were hearing the lament of the employers.
Marion City Schools Superintendent Gary Barber took the hint: “We’ve spent pretty much a year going around and talking to all of our businesses and industry to really start identifying what are the high demand jobs where we might be able to fill a void. When you’re talking about the automotive industry, or whether it’s Wilson Bohannan Locks, or it’s Nucor Steel, or it’s Whirlpool — what we keep hearing is it’s about students having a skillset to problem-solve, for students to be able to have a skillset to look at processes and be able to make processes better.”
Within 10 years, millennials are projected to comprise 75 percent of the available workforce. With an intermodal facility a mile down the road, one gap identified by Barber was in logistics training. “So, we went out and pursued a Global Logistics Advanced Career Tech program and we’ll be the only school district in Ohio that’s offering that program next year. We already have 15 students signed up for the first year. It’s a two-year program,” explains Barber, “where they’re able to leave with some industry credentials in logistics that will not only make them employable right now, but will allow them to go to college with some of the articulation agreements — to be able to leave with college credit.”
Barber is a product of Youngstown where a collapsing steel industry left the town reeling, so economic displacement and revival are close to his heart. Now, heading a school district of 4,700 students in a once-thriving industrial town, he’s not leaving career prep for high school.
“I think it really has to go down even further, believe it or not, to the middle school,” Barber says. “We are really ramping up our programming at the middle school. Every kid is going to have robotics. Every kid is going to have an allied health field. Every kid will have a business course. The biggest thing is that we need to make sure that our pathways are broad enough that they’re not going to pigeon-hole a student.”
Barber is also reaching out to nearby Tri-Rivers Career Center, whose superintendent, Chuck Speelman, has developed RAMTEC (Robotics & Advanced Manufacturing Technology Education Collaborative) that utilizes equipment supplied by Fanuc, Allen-Bradley and other automation suppliers to deliver advanced manufacturing skills to high-school-age and adult students. The RAMTEC concept has been recognized by Ohio’s Department of Education, which recently awarded $14.99 million to replicate the Tri-Rivers model in eight other career centers around Ohio. They will be tied together in the RAMTEC Consortium where they can share instructors and best practices and serve the training needs of companies around Ohio and beyond.
Academia and Industry
In the state of Washington, aerospace is an $85.7 billion industry accounting for 11 percent of the state’s wages. Some 132,000 people work on the Boeing assembly lines or in supplier plants. With the 777X labor contract sealed, Boeing Commercial Airplanes CEO Ray Conner is now focused on hiring 20,000 to 30,000 younger workers by 2020 to replace aging boomers.
Working with the Washington Aerospace Partnership, a 501(c)4 nonprofit, Conner is creating Germanstyle apprenticeships in high schools. Partnership Director and Secretary of the Governor’s Office of Aerospace Alex Pietsch says, as part of its promise to Boeing, the state is investing heavily with 10 new skill centers created in selected high schools and $8 million in state funding per year for 1,000 new slots in 24 community college aerospace programs.
Cooperation between industry and education can also be found on the University of Washington campus, where Boeing engineers are working as adjunct professors in the new Boeing Advanced Research Center. “In my understanding, that’s the first time anywhere in the country where the company has put its employees on campus working side by side with professors and students,” notes Pietsch.
As companies continue to face the demographic deficit, it is likely the Boeing-University of Washington partnership won’t be the only place where the boundary between academia and industry grows blurry.